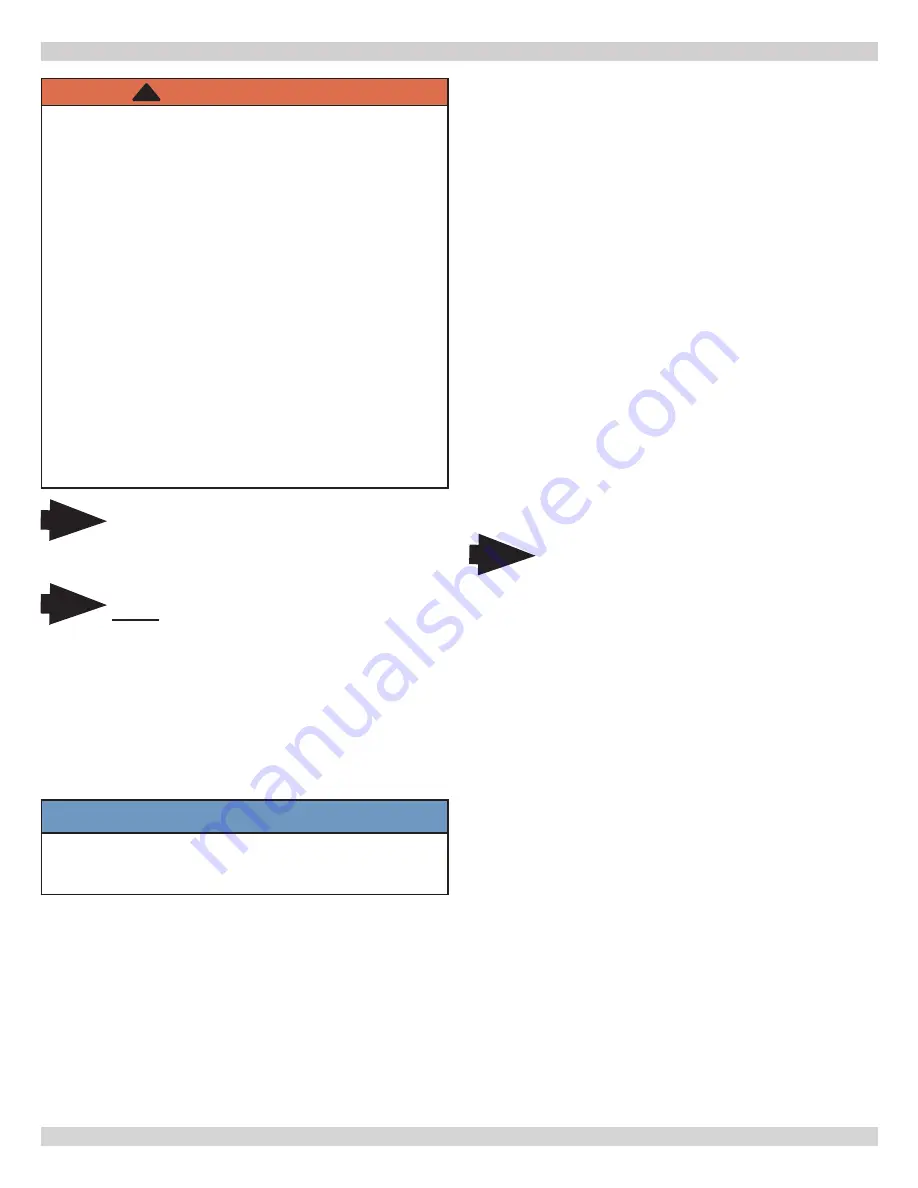
30
6.1 General
• Primary/Secondary piping required.
• Install piping in accordance with authority having
jurisdiction.
• Support system piping and safety relief valve
discharge piping. Boiler's internal piping can be
damaged if subjected to excessive weight.
• Size central heating pump (and domestic hot water
pump, if used) for system requirements only.
Internal heat exchanger pump compensates for
pressure drop through boiler internal piping and
heat exchanger.
•
Thoroughly clean and flush system before
connecting to boiler.
• If oil is present in system water, use approved
detergent to wash system.
• It is necessary to semi-annually check the water
quality of central heating systems.
WARNING
• Poison hazard. Ethylene glycol is toxic. Do
not use ethylene glycol.
• Never use automotive or standard glycol
antifreeze, even ethylene glycol made for
hydronic systems.
• Ethylene glycol can attack gaskets and seals
used in hydronic systems.
• Do not use petroleum based cleaning or
sealing compounds boiler system.
•
Do not fill boiler or boiler system with softened
water.
• Use only inhibited propylene glycol solutions
certified by fluid manufacturer as acceptable
for use with closed water heating system.
•
Thoroughly clean and flush any system that
used glycol before installing new Boiler.
• Provide user with Material Safety Data Sheet
(MSDS) on fluid used.
!
• Manufacturer recommends installation of magnetic
dirt separator in the hydronic system where there
are cast iron or steel components, or where the
previous boiler was a cast iron heat exchanger.
The abrasive, extremely fine sediment is difficult
to remove and can deposit onto heat exchange
surfaces and accumulate in pump cavities causing
reduced efficiency and premature wear.
• Flush system to remove any solid objects such as
metal chips, fibers, or Teflon tape, etc.
• Flush system until water runs clean and piping is
free of sediment.
•
Use purge valve to flush zoned systems, each zone
separately. If purge valves and isolation valves
are not installed, install them to properly clean the
system.
• When purging installations that include standing iron
radiators and systems with manual vents at high
points, start with nearest manual air vent. Open the
vent until water flows out, then close vent. Repeat
this procedure, working toward furthest air vent.
• Install a basket strainer if large amounts of sediment
is present. Keep basket clear of sediment build up.
• Ensure piping in the heating system has an oxygen
barrier.
6.2 Special Conditions
• System piping exposed to freezing conditions: Use
inhibited propylene glycol solutions certified by fluid
manufacturer for use with closed water heating
system. Do not use automotive or ethylene glycol.
• Boiler installed above radiation level (or as required
by authority having jurisdiction). Integral low water
pressure switch is provided in boiler.
• Boiler used in connection with refrigeration system.
Install piping in parallel with boiler, with appropriate
valves to prevent chilled medium from entering
boiler.
• System piping connected to heating coils located
in air handling unit exposed to refrigerated air
circulation. Install flow control valves or other
automatic means to prevent gravity circulation of
boiler water during cooling cycle.
• Boiler used to provide heat to fan coil unit, which
also contains a refrigeration coil, precautions should
taken to prevent the hot water coil from freezing.
Consider items such as a freeze sensor on the hot
water coil and/or low ambient controls on the air
conditioning unit. It is manufacturer recommended
to install a drip pan whenever there is a risk of
damage to the area below a fan coil as a result of a
water leak.
6 - HYDRONIC PIPING
NOTICE
The intended use of the internal heat exchanger
pump is a boiler loop. Do not use as a primary
system pump.
System pressure above 43 psi [2.96 bar]
WILL
result in boiler shutting down.
Boiler rated at 50 psig (345 kPa)
maximum allowable working pressure.
Boiler provided with 30 psig (206 kPa)
safety relief valve.
Do not expose boiler and condensate
piping to freezing temperatures.
Note
Note
Note
240013371 REV B, [10/01/2021]
Содержание MACF-115
Страница 2: ...MACF 150 ...
Страница 4: ...MAHF 125 ...
Страница 74: ...70 A 1 MODEL 100 Heat Only APPENDIX A WIRING DIAGRAMS 240013371 REV B 10 01 2021 ...
Страница 75: ...71 A 2 MODEL 125 Heat Only APPENDIX A WIRING DIAGRAMS 240013371 REV B 10 01 2021 ...
Страница 76: ...72 APPENDIX A WIRING DIAGRAMS A 3 MODEL 165 Heat Only 240013371 REV B 10 01 2021 ...
Страница 77: ...73 APPENDIX A WIRING DIAGRAMS A 4 MODEL 115 Combi 240013371 REV B 10 01 2021 ...
Страница 78: ...74 A 5 MODEL 150 Combi APPENDIX A WIRING DIAGRAMS 240013371 REV B 10 01 2021 ...
Страница 79: ...75 A 6 MODEL 205 Combi APPENDIX A WIRING DIAGRAMS 240013371 REV B 10 01 2021 ...
Страница 80: ...76 NOTES 240013371 REV B 10 01 2021 ...
Страница 81: ...77 NOTES 240013371 REV B 10 01 2021 ...
Страница 82: ...78 NOTES 240013371 REV B 10 01 2021 ...
Страница 117: ...33 MODEL 100 Heat Only 100 HEAT ONLY WIRING DIAGRAM PN 240012875 REV C 10 01 2021 ...
Страница 118: ...34 MODEL 125 Heat Only 125 HEAT ONLY WIRING DIAGRAM PN 240012875 REV C 10 01 2021 ...
Страница 119: ...35 MODEL 165 Heat Only 165 HEAT ONLY WIRING DIAGRAM PN 240012875 REV C 10 01 2021 ...
Страница 120: ...36 115 COMBI WIRING DIAGRAM MODEL 115 Comb PN 240012875 REV C 10 01 2021 ...
Страница 121: ...37 MODEL 150 Combi 150 COMBI WIRING DIAGRAM PN 240012875 REV C 10 01 2021 ...
Страница 122: ...38 MODEL 205 Combi 205 COMBI WIRING DIAGRAM PN 240012875 REV C 10 01 2021 ...
Страница 127: ...43 LOW WATER CUTOFF DETAIL LOW WATER CUTOFF NO NO YES PN 240012875 REV C 10 01 2021 ...
Страница 132: ...48 3 FAULT SOLUTION SECTIONS PN 240012875 REV C 10 01 2021 ...
Страница 135: ...51 Parameter ID Changed From Changed To Date Reason PARAMETER CHANGE HISTORY PN 240012875 REV C 10 01 2021 ...