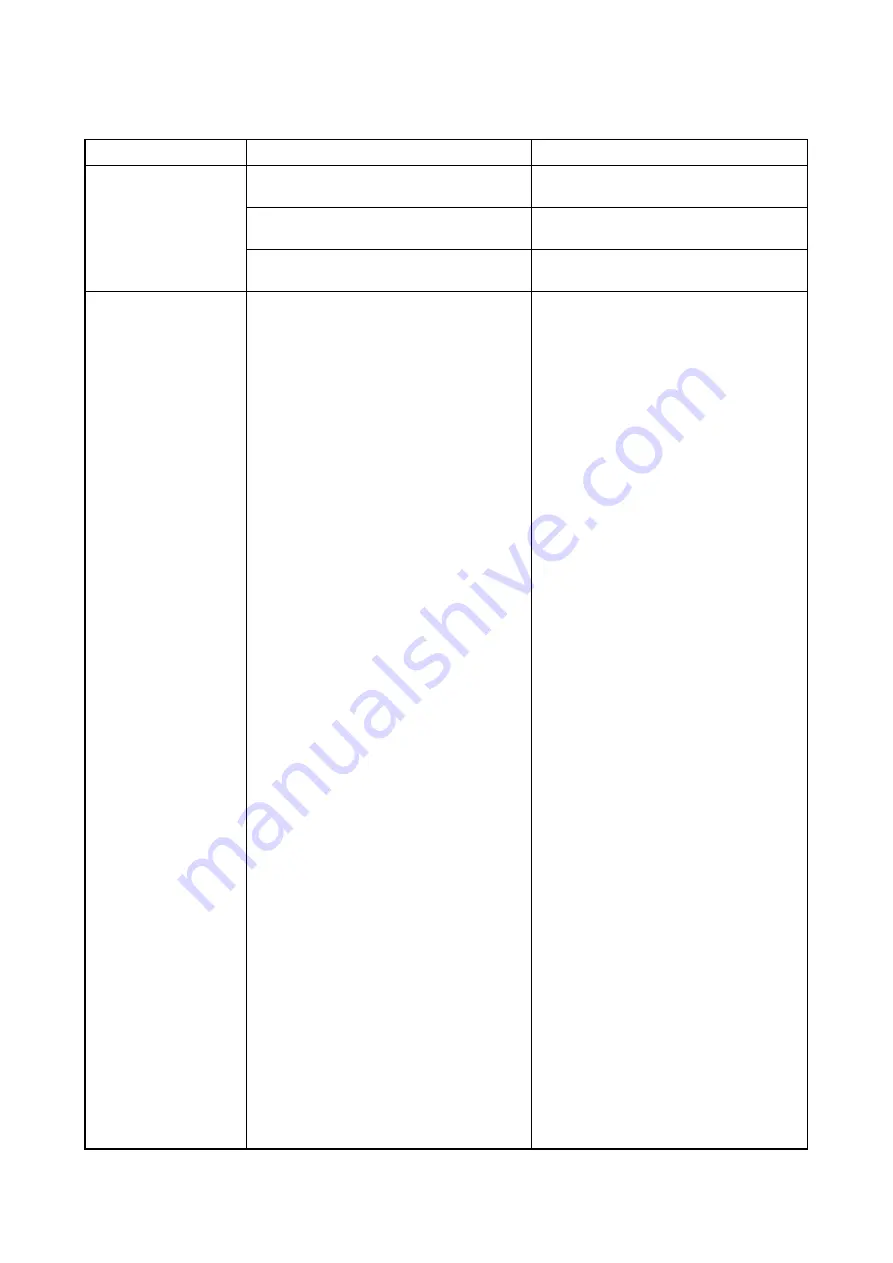
3MJ
1-4-6
1-4-4 Mechanical problems
Problem
Causes/check procedures
Corrective measures
(1)
Paper jams.
Check if the contact between the feedshift
roller and feedshift pulleys is correct.
Check and remedy.
Check if the contact between the feedshift
roller and press roller is correct.
Check and remedy.
Check if the contact between the eject roller
and eject pulleys is correct.
Check and remedy.
(2)
Abnormal noise is heard.
Check if the rollers and gears operate
smoothly.
Grease the bearings and gears.
Содержание DF 420
Страница 1: ...Service Manual Document Finisher DF 420 First Edition Date 04 08 2009 3MJSM060 ...
Страница 2: ...Service Manual Document Finisher DF 420 First Edition Date 04 08 2009 3MJSM060 ...
Страница 4: ...Revision history Revision Date Replaced pages Remarks ...
Страница 5: ...This page is intentionally left blank ...
Страница 11: ...This page is intentionally left blank ...
Страница 13: ...3MJ This page is intentionally left blank ...
Страница 17: ...3MJ 1 1 4 This page is intentionally left blank ...
Страница 21: ...3MJ 1 2 4 3 Remove the tape from the process table Figure 1 2 4 Tape Process table ...
Страница 37: ...3MJ 1 5 4 This page is intentionally left blank ...
Страница 43: ...3MJ 2 1 6 This page is intentionally left blank ...
Страница 47: ...3MJ 2 2 4 This page is intentionally left blank ...