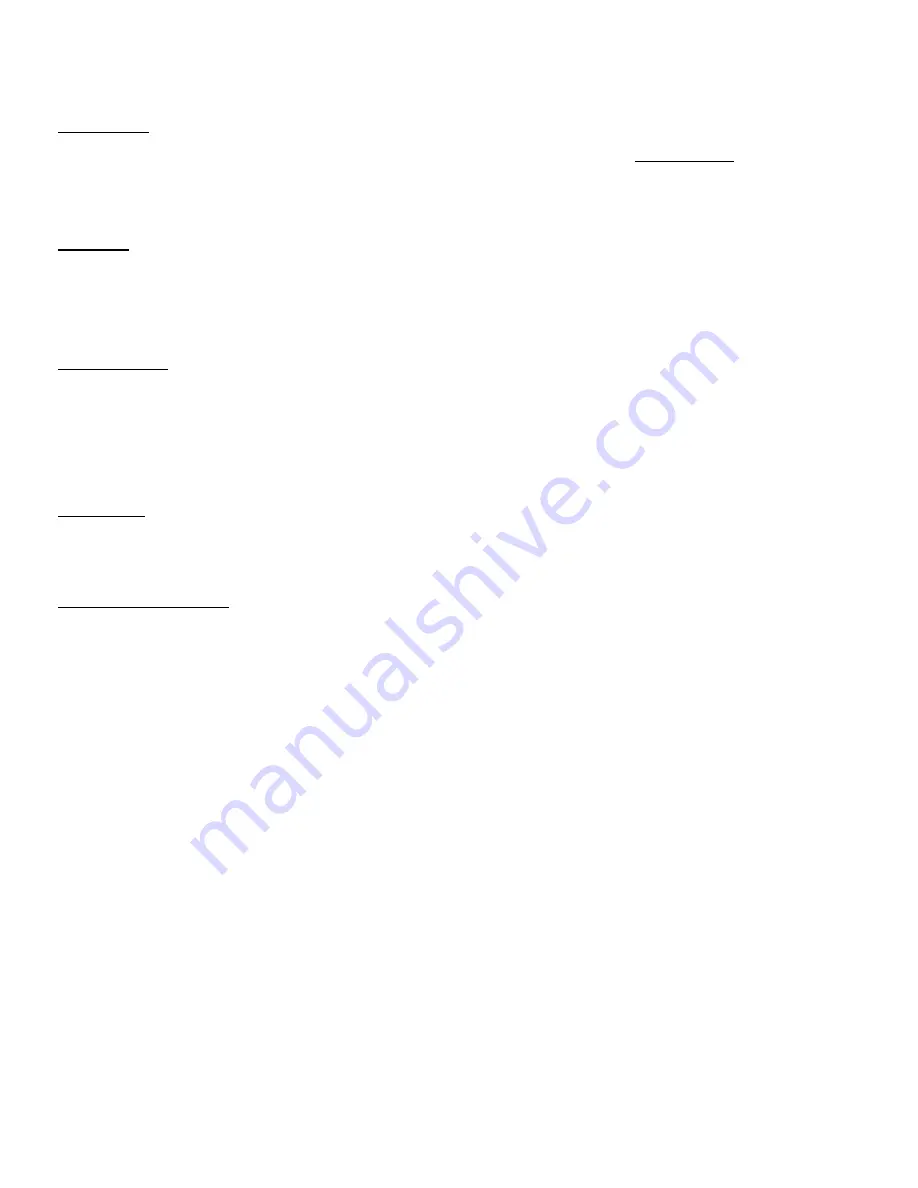
8
GENERAL
UNPACKING
Inspect the box and pump carefully for any signs of damage incurred in transit and report with-in 7 days of receipt. Since all our
pumps are shipped F.O.B. our factory, such damage is the responsibility of the carrier and reported to them. The inlet & exhaust of
the pumps are covered with plastic caps to prevent dirt and other foreign substances from entering the pump. Leave the caps in place
until you are ready to pipe the pump to your equipment.
LOCATION
Locate the pump as near as possible to the equipment being evacuated so that the vacuum, water and exhaust connections can be
conveniently made. Leave 12-18” of access around the pump to allow proper access for routine maintenance. Allow access to the oil
sight glass in order to inspect the oil level and for easy access to change the lubricating oil and exhaust
filter.
INSTALLATION
The pump should be mounted on a rigid foundation, such as a concrete floor. The pump should be made level by shimming or grout-
ing, if necessary. Bolt pump to foundation without putting a strain or twist in the pump housing.
Remove cap from exhaust and intake openings only when ready to make pipe connection. When the pump is to be subjected to tem-
peratures below freezing, drain water jacket through the housing drain plug to prevent cracking the housing, then blow out water jack-
et with compressed air. Follow this same procedure for storage
Cooling water:
The pump comes air cooled as standard with an installed shell & tube oil/water cooler for optional water cooling. If operating the pump
as water cooled, do not allow cooling water to freeze. The water inlet/outlet ports are on each end of the oil cooler. Control the water
flow so the discharge temperature is between 95-110 deg F when incoming water is between 50-70 deg F. Where the water is ex-
tremely cold, control the flow so the pump runs just warm to the touch.
VACUUM CONNECTION
All pipe lines should be as short as possible and should be no smaller in diameter than the inlet to the pump….if it is absolutely
necessary to run a long line, the suction pipe should be increased 50% in diameter. Conductance of long lengths of suction piping
must be checked and the line sized large enough so the pumping speed of the system will not be seriously affected.
Pumps operating in parallel on a common main line should have a manual or automatic shut-off valve or positive acting check valve
installed in the suction line of the pump.
Should the process gas contain dust of other foreign material, a suitable inline particulate filter should be connected to the inlet
port…..contact US Vacuum for recommendations.
When connecting the pump to the system, provide proper piping geometry to prevent dirt from the system from entering the pump and
to prevent back siphoning of pump oil in the system chamber.
The vacuum piping should be designed to insure that no liquids such as condensate or liquid carryover from the process can reach
the pump. If this possibility exists, a knock-out liquid separator should be installed…..contact US Vacuum for recommendations.
The best piping for the vacuum side of the pump is made up with flanges using neoprene/fiber gaskets or O-rings. Flanges may be
welded or threaded to pipe. If threaded connections are used, use a heavy sealing compound to insure no leaks are present.
CAUTION: Make sure the system to be evacuated and connecting lines are clean and free of weld splatter, dirt, or grit.
Foreign matter entering the pump can cause failure and possibly damage the internal parts,
Содержание RP50B-WS
Страница 16: ...16 RP 50B PUMP PARTS 1 2 3 4 5 6 7 8 9 10 11 12 13 14 15 16 17 18 19 20 21 22...
Страница 19: ...19 NOTES...