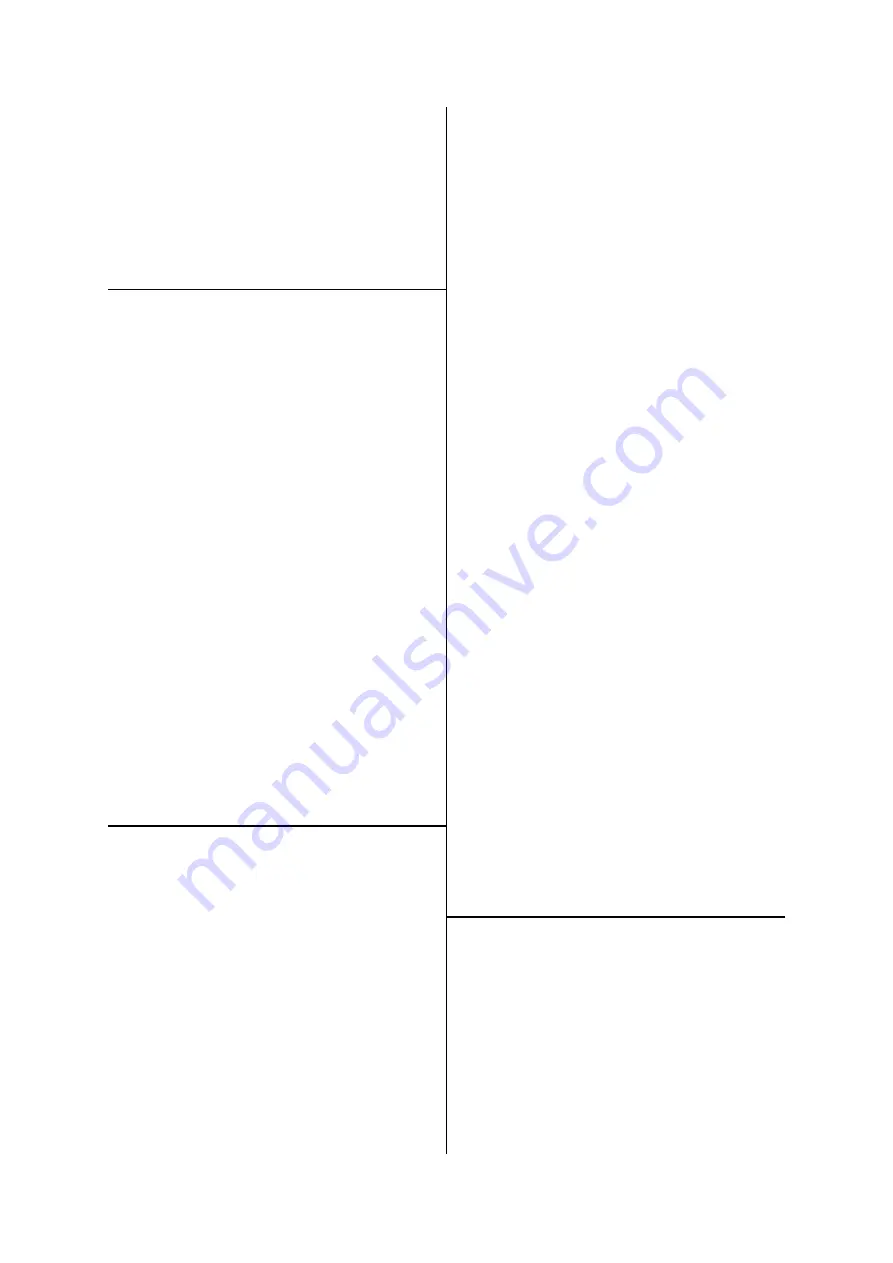
Dismantling & Assembly Instructions
Disconnect tool from air supply.
The drill chuck (1) may be removed from the assembly by
placing the drill chuck key in the drill chuck securely and giving
the chuck key a sharp tap with a hammer in the direction to
loosen a right hand threaded joint. If this fails to remove the
chuck then remove after the gearbox assembly has been
removed from the drill assembly. (See later).
Place the motor housing (42) in a vice fitted with soft jaws with
the handle section pointing upwards, unscrew hose adaptor
(46) and remove 2 off screws (45) and take off exhaust muffler
(44). Unscrew clamp nut (2) and remove the gearbox assembly.
If the drill chuck has not successfully been removed as it is too
tightly fitted, then remove internal gear (3) and lever off bearing
(25) and grip planet cage (8) so as to be able to unscrew the drill
chuck (1). Continue to dismantle the gearbox by taking off
bearing chuck spacer (5) and bearing (4) and fibre washer
(6)from planet cage (8). Remove retaining ring (7). Push out 2 off
planet pins (9) and slide out 2 off planet gears (10) with 22 off
needle rollers (11). Pull out the motor assembly from motor
housing (42).
To dismantle the motor assembly grip the front end plate (27)
by hand and tap the splined end of rotor (28) with a non metallic
or soft metal (lead or aluminium) hammer to drive the rotor
through the front end plate (27) and bearing (26) assembly.
Remove cylinder (30) and 4 off rotor blades (29) from rotor (28).
Do not remove 2 off pins (47) from front end plate (27) and rear
end plate (48) unless replacements are required. Prise out rear
bearing cap (12) and remove retaining ring (33). Support the
rear end plate (48) in a piece of tube with a bore diameter as
close as possible to the maximum diameter of the rotor and tap
the non splined end of the rotor to drive it through the rear end
plate (48) and bearing (49) assembly. With a suitable punch
drive out bearing (26) from front end plate (27) and rear bearing
(49) from rear end plate (48).
Drive out pin (41) and slowly and carefully so as not to damage
the seals, grip the trigger and pull out the control valve
assembly. Unscrew set screw (34) and take off trigger (35) from
valve stem (36). Remove spring (43) and slide valve stem (36)
through valve bushing (39). Remove O-ring (37) from valve stem
(36) and O-rings (38) and (40) from valve bushing (39). Take out
O- ring (38) from motor housing (42).
Reassembly
Clean all component parts and examine for wear before
reassembling. Use only manufacturer or distributor supplied
spare parts. Check in particular for wear and cuts on O-rings and
wear on rotor blades. Lightly coat all parts with a suitable
pneumatic tool lubricating oil preferably one incorporating a rust
inhibitor. Pack all bearings and gearbox with a lithium or
molybdenum based general purpose grease and reassemble in
the reverse order (see note below).
For the motor assembly ensure that the front and rear end plates
that abut the cylinder are clean and free from burrs and surface
marking. If necessary lap faces that abut the cylinder on a flat
fine grade of abrasive paper. Press bearings into front and rear
end plates, support the bearing in the rear end plate on its inner
ring and tap the rotor on its splined end with a soft metallic
hammer into the bearing until the rotor locates against the rear
end plate. Support the inner face of the end plate as close as
possible to the largest diameter of the rotor and tap the non
splined end of the rotor until a clearance of 0.0015" (0.040mm)
0.0025" (0.065mm) is obtained between the inner face of the
rear end plate and the rotor. This clearance to be checked when
pulling the rotor away from the rear end plate and bearing
assembly. Spin rotor to ensure that it will rotate freely in the rear
end plate bearing. Locate the cylinder by the locating pin to the
rear end plate checking that the ports in the end plate match
with those in the cylinder. Insert the four rotor blades into the
rotor and locate correctly the front end plate to the cylinder
using the locating pin. Ensure that the rotor will spin freely in the
assembly. This is best checked by placing the motor assembly
in a vee block and squeezing the front and rear end plates
against the cylinder. Fit retaining ring (33) and insert rear bearing
cap (12) into rear end plate (48).
pressing the trigger on the tool. Disconnect the air line and pour
into the intake bushing a teaspoonful (5ml) of a suitable
pneumatic motor lubricating oil preferably incorporating a rust
inhibitor. Reconnect tool to air supply and run tool slowly for a
few seconds to allow air to circulate the oil. If tool is used
frequently lubricate on daily basis and if tool starts to slow or
lose power.
It is recommended that the air pressure at the tool whilst the
tool is running is 90 p.s.i./6.3 bar. The tool can run at lower and
higher pressures with the maximum permitted working air
pressure of 150 p.s.i./10.3 bar.
Page No 2
Safety Rules When Using A Drill
1) Read all the instructions before using this tool. All operators
must be fully trained in its use and aware of these safety rules.
All service and repair must be carried out by trained personnel.
2) Always select a suitable cutting, abrasive device suitable for
use with this drill.
3) Always shut off the air supply to the drill and depress the
trigger to exhaust air from the feed hose before fitting, adjusting
or removing the device. Remove drill chuck.
4) Always adopt a firm footing and/or position and be aware of
torque reaction developed by the drill.
5) Use only correct spare parts.
6) Check hose and fittings regularly for wear. Do not carry the
tool by its hose and ensure that the hand is remote from the
Operating
Select suitable drill bit, insert the shank into the drill chuck as far
as possible and tighten chuck with key supplied making sure
that the shank of the device is securely clamped centrally
between the three chuck jaws. Remove chuck key.
When drilling holes of all sizes it is advised to use a pointed
punch to mark the centre at which the hole is to be drilled as
this will provide a starting point for the drill tip. This procedure
will prevent the drill bit from skidding, ensure that the hole is
drilled where intended and help to prevent drill breakage when
using small drills. When drilling, particularly with small diameter
drills, always try to ensure that load applied to the drill is such
that the drill bit is always at right angles to the hole being drilled.
Do not force the drill but allow it to cut.
When drilling always adopt a firm posture to be able to
counteract any sudden movement of the drill due to torque
reaction. Such torque reaction can occur when the drill stalls
due to a too heavy load being applied or the material being too
hard or tough. The torque reaction can occur when the drill
breaks through the material being drilled, particularly on sheet
metal. Always use eye protection and hand protection is
advised, particularly when drilling holes in metals where the
material being removed from the hole is in the form of long
sharp strips. Do not tie the drill chuck key to the drill as the
attaching device i.e. string or chain could become entangled
with the rotating chuck and bit etc.
If using an abrasive device, drilling stone or performing any
operation where dust is created, it is recommended to use a
breathing mask.
Always ensure that the material to be drilled is firmly fixed to
prevent its movement.
It is also recommended that when drilling holes of large
diameter to first pre drill a hole of smaller diameter as this will
reduce effort required to drill the hole and minimise torque
reaction.