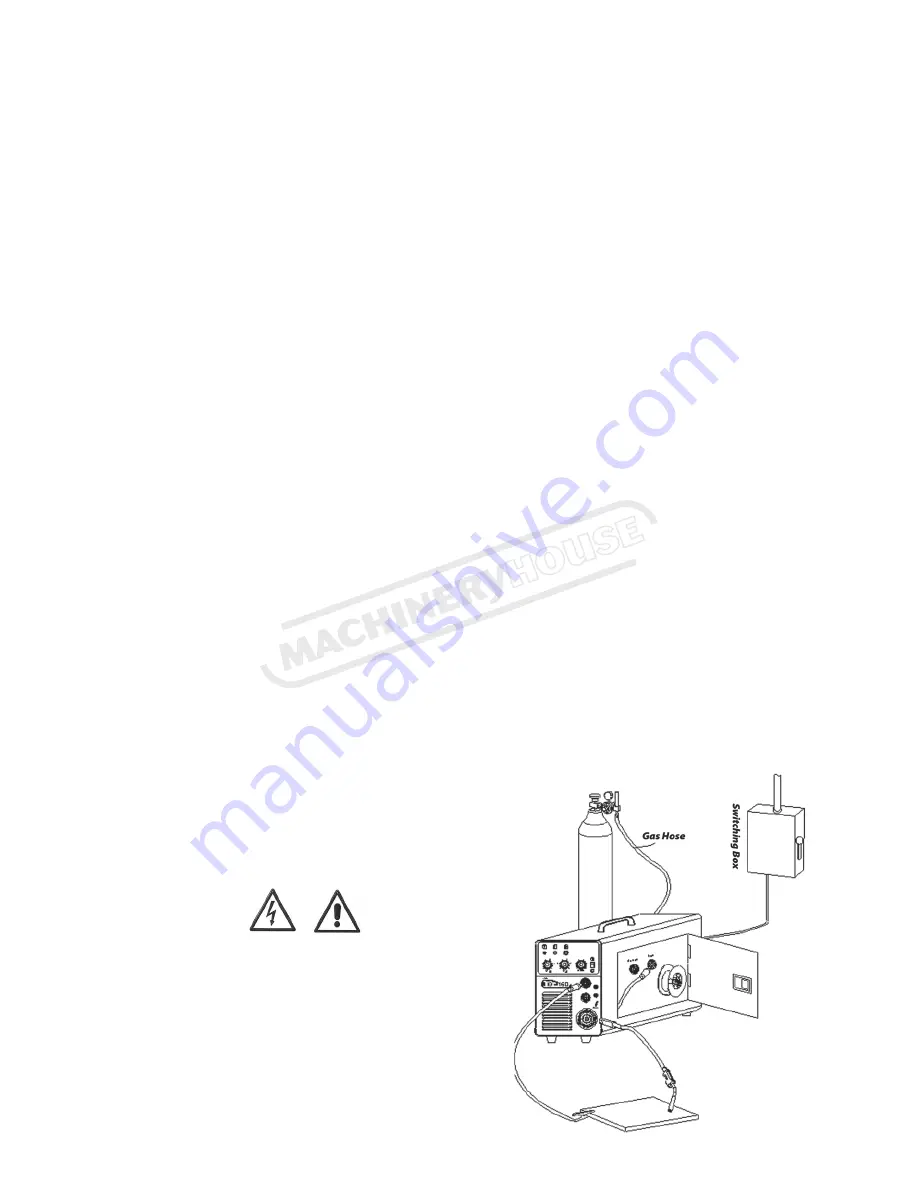
INSTALLATION & OPERATION
Installation of gas shielded arc welding
(1)
Turn the power source on and select the MIG function through the STICK/MIG
selector. (See Panel Structure Diagram Number 7)
(2)
Plug the welding torch into the output socket “10” on the front panel, (See Panel
Structure Diagram Number 10) and tighten it.
(3)
Insert the earth cable plug into the negative socket “8” on the Panel Structure
Diagram, and tighten it clockwise.
(4)
Insert the fast plug on the wire feeder into the output socket “GAS” on the
clapboard, and tighten it clockwise. (See Clapboard Structure Diagram Number 15)
(5)
Remove the right side cover of the unit and push the wire spool onto the spindle.
Make free the end of the wire and cut it smoothly. Unlock the pressure arm and align the
wire into the groove of the drive roll putting a short part of the wire into the torch recep-
tacle. Check that the drive roll and contact tip in MIG torch being used complies with the
wire diameter, replace if necessary. Lock the pressure arm and check that the bearing
roll presses the wire exactly into the groove.
(6)
Press selector switch on for “wire inching” (See Panel Structure Diagram Number 3)
Press and hold until wire is visible at end of torch.
(7)
Tightly connect the gas hose, which comes from the back of the machine to the
brass nipple of supplied regulator, adjust argon regulator to deliver the required litres
per minute.
NOTE. reffer to instruction manual of argon regulator for proper use.
(8)
Adjust the welding voltage adjustment knob and wire feeding speed adjustment
knob according to practical needs to get the desired welding voltage and welding
current. (See Panel Structure Diagram Number 5&6)
(9)
Press the welding torch switch, and welding can be carried out.
(10)
Adjust the burnback time potentiometer on the clapboard to get the desired length
of welding wire stretching into the contact tip after welding.
(See Clapboard Structure Diagram Number 14)
Installation sketch map
WARNING!
Disconnect the Electrode Holder cable
from the machine before using MIG
function. If cable is not disconnected
welding voltage is present and can cause
arcing or
fl
ash.
Page 9
Instruction Manual for MIG-TIG-MMA 250 (W179)
15/12/2014