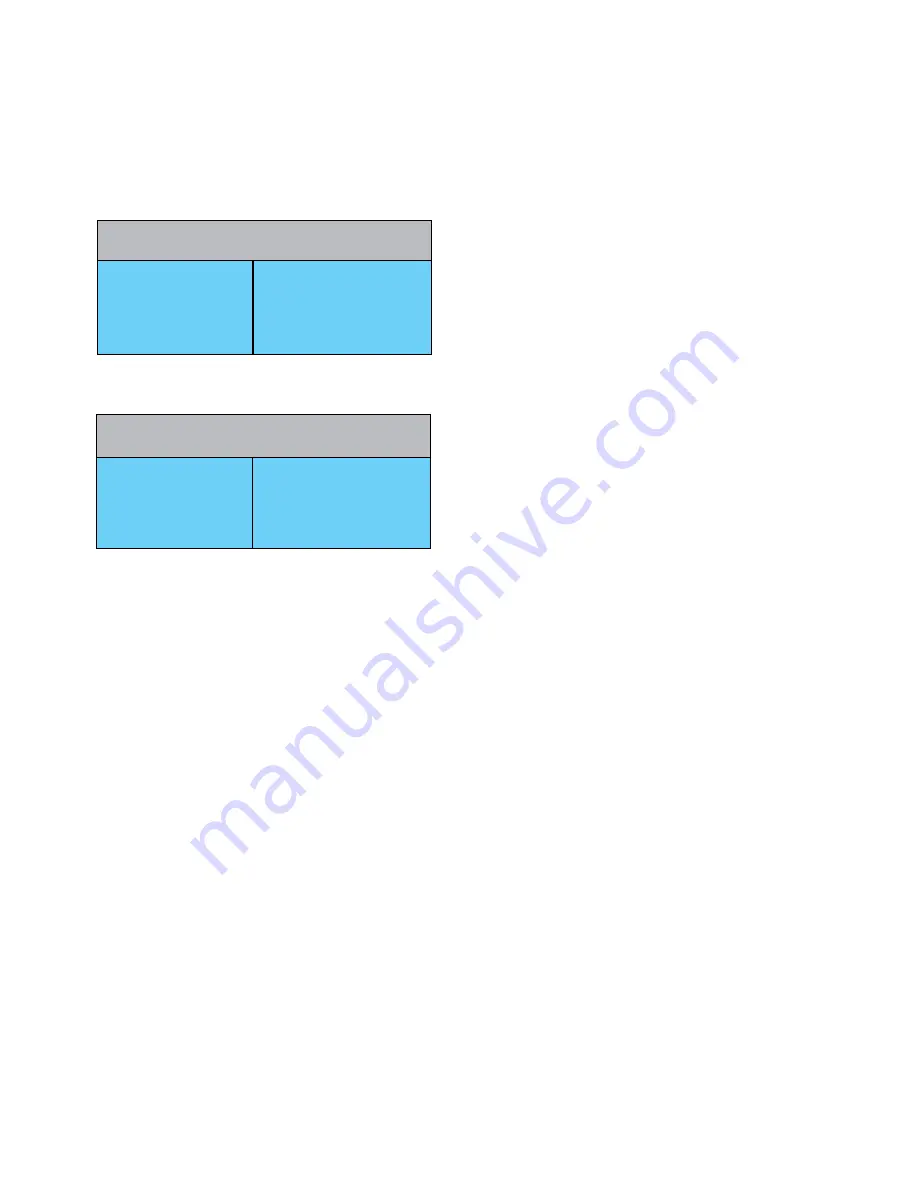
11
11
Electrode Size
Average Thickness Maximum Recommended
of Material
Electrode Diameter
1.0 - 2.0mm
2.5mm
2.0 - 5.0mm
3.2mm
5.0 - 8.0mm
4.0mm
8.0 - > mm
5.0mm
The size of the electrode generally depends on the
thickness of the section being welded, and the thicker
the section the larger the electrode required. The table
gives the maximum size of electrodes that maybe used
for various thicknesses of section base
ed
on using a
gen
eral purpose type 6013 electrode.
Correct current selection for a particular job is an im-
portant factor in arc welding. With the current set too
low, dif culty is experienced in striking and maintaining
a stable arc. The electrode tends to stick to the work,
penetration is poor and beads with a distinct rounded
pro le will be deposited. Too high current is accompa-
nied by overheating of the electrode resulting undercut
and burning through of the base metal and producing
excessive spatter. Normal current for a particular job may be considered as the maximum, which can be
used without burning through the work, over-heating the electrode or producing a rough spattered surface.
The table shows current ranges generally recommended for a general purpose type 6013 electrode.
Arc Length
To strike the arc, the electrode should be gently scraped on the work until the arc is established. There is a
simple rule for the proper arc length; it should be the shortest arc that gives a good surface to the weld. An
arc too long reduces penetration, produces spatter and gives a rough surface nish to the weld. An exces-
sively short arc will cause sticking of the electrode and result in poor quality welds. General rule of thumb
for down hand welding is to have an arc length no greater than the diameter of the core wire.
Electrode Angle
The angle that the electrode makes with the work is important to ensure a smooth, even transfer of metal.
When welding in down hand, llet, horizontal or overhead the angle of the electrode is generally between 5
and 15 degrees towards the direction of travel. When vertical up welding the angle of the electrode should
be between 80 and 90 degrees to the work piece.
Travel Speed
The electrode should be moved along in the direction of the joint being welded at a speed that will give the
size of run required. At the same time, the electrode is fed downwards to keep the correct arc length at all
times. Excessive travel speeds lead to poor fusion, lack of penetration etc, while too slow a rate of travel
will frequently lead to arc instability,slag inclusions and poor mechanical properties.
Material and Joint Preparation
The material to be welded should be clean and free of any moisture, paint, oil, grease, mill scale, rust or
any other material that will hinder the arc and contaminate the weld material. Joint preparation will depend
on the method used include sawing, punching, shearing, machining, ame cutting and others. In all cases
edges should be clean and free of any contaminates. The type of joint will be determined by the chosen
application.
Welding Current (Amperage)
Electrode Size
Current Range
ø mm
(Amps)
2.5mm
60 -
100
3.2mm
100 - 130
4.0mm
130 - 165
5.0mm
165 - 260
Electrode Selection
As a general rule, the selection of an electrode is straight forward,in that it is only a matter of selecting an
electrode of similar composition to the parent metal. However, for some metals there is a choice of several
electrodes, each of which has particular properties to suit speci c classes of work. It is recommend
ed
to
con
sult your welding supplier for the correct selection of electrode.
MMA (Stick) Welding
General Description
Содержание Arclite KUMJRAL140
Страница 26: ...26 Notes...
Страница 27: ...27 Notes...