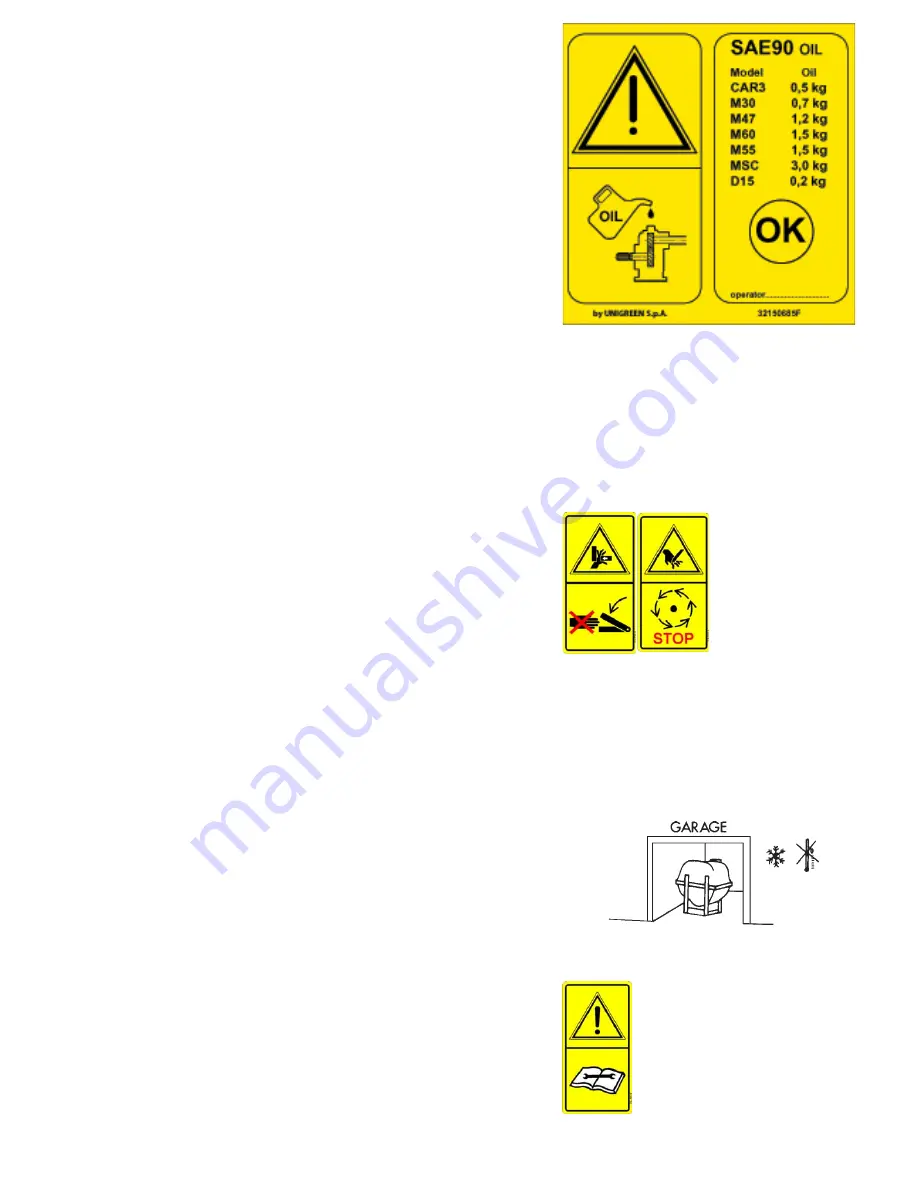
unigreen
23
To prevent chemical attacks we recommend spraying transparent paint on the
parts that are most exposed to the product and equipping the mistblower with
stainless steel pressure gauges.
8.2.1 CLEANING THE NOZZLES
Check the state of wear of the nozzles and replace them when the delivery is
over 30-35% of the theoretical level.
If you notice even a partial blockage of a nozzle proceed as follows:
- drain the pressure and stop the machine
- dismantle the screw or bayonet ringnuts holding the nozzles
- clean with a small brush or compressed air,
don’t use nails, punches or
bradawls
- reassemble the nozzles and the ringnuts, replacing the filters and seals.
8.2.2 LUBRICATION
The moving mechanical components must be lubricated to prevent wear and
overheating. This lubrication can be done with grease or oil: oil allows
significantly higher speeds, in general grease is used to lubricate bearings with
a vertical or inclined axis as it stays in the zone for longer.
8.2.3 MULTIPLIER LUBRICATION
The multiplier and disengaging boxes are normally lubricated in an “oil bath”, in
special cases NLGI n.0 grease is used. The viscosity is an essential
characteristic of a lubricant oil and this is indicated by the SAE (SOCIETY OF
AUTO-MOTIVE ENGINEERS) classification of the oils for gearboxes and
differentials. Special additives improve the capacity of the oil to maintain a
lubricant film also at high pressures and temperatures. We recommended
using SAE 90 oil for the multiplier and disengaging boxes. The quantity of oil is
established by the level cap. A greater quantity of oil doesn’t improve the
conditions of lubrication and can cause overheating in the box. Changing the
oil protects the parts from the dangers associated with wear and the presence
of metallic particles that can be present, especially in the first period of use.
We recommend replacing the oil after the first 50 working hours and then
subsequently every 500 hours.
The quantity of oil needed is indicated on the sticker near the multiplier (FIG.
23)
WARNING: waste oil must not be dispersed in the environment, to dispo-
se of waste oil see paragraph 8.7.1.
8.3
EXTRAORDINARY MAINTENANCE
At the end of a season of intense use, or every two years of normal use, it is a
good idea to have a specialised service technician perform a general check on
the machine.
8.4
REPAIRS
We recommend having the normal UNIGREEN assistance service available
from our reseller perform any repairs or contact a specialised workshop.
During all of the repairs, in particular when welding, the machine and the
circuit must be clean of any residues of chemical product.
If the machine has to be lifted (for example to change a wheel) follow the
instructions in point 4.3 of the present handbook.
Also make sure the machine is stopped, connected to the tractor, and use the
relevant chocks to block the wheel still on the ground.
If you use a jack (manual or hydraulic) make sure you use a jack that is
suitable for the frame so it can’t slip and put it in the right position. The jack
must be placed under the main frame of the machine near the wheel to
change. Make sure the ground is compact: if necessary use wooden beams or
other sufficiently resistant material to broaden the supporting base of the jack.
8.5
STORAGE IN A WAREHOUSE AND TRANSPORTATION
The sprayer must be kept in a closed place away from excessive humidity and
protected from frost. Especially if electrical pressure regulators, electrical
motors, a spraying computer or similar components are fitted.
Before storing the machine, after you have washed it, apply a light coat of oil.
If the temperature might drop to below zero, drain any residual liquid or add
roughly 0.5 L of normal antifreeze for auto vehicles.
To transport the machine follow the instructions in point 4.3 of the present
handbook.
FIG. 23