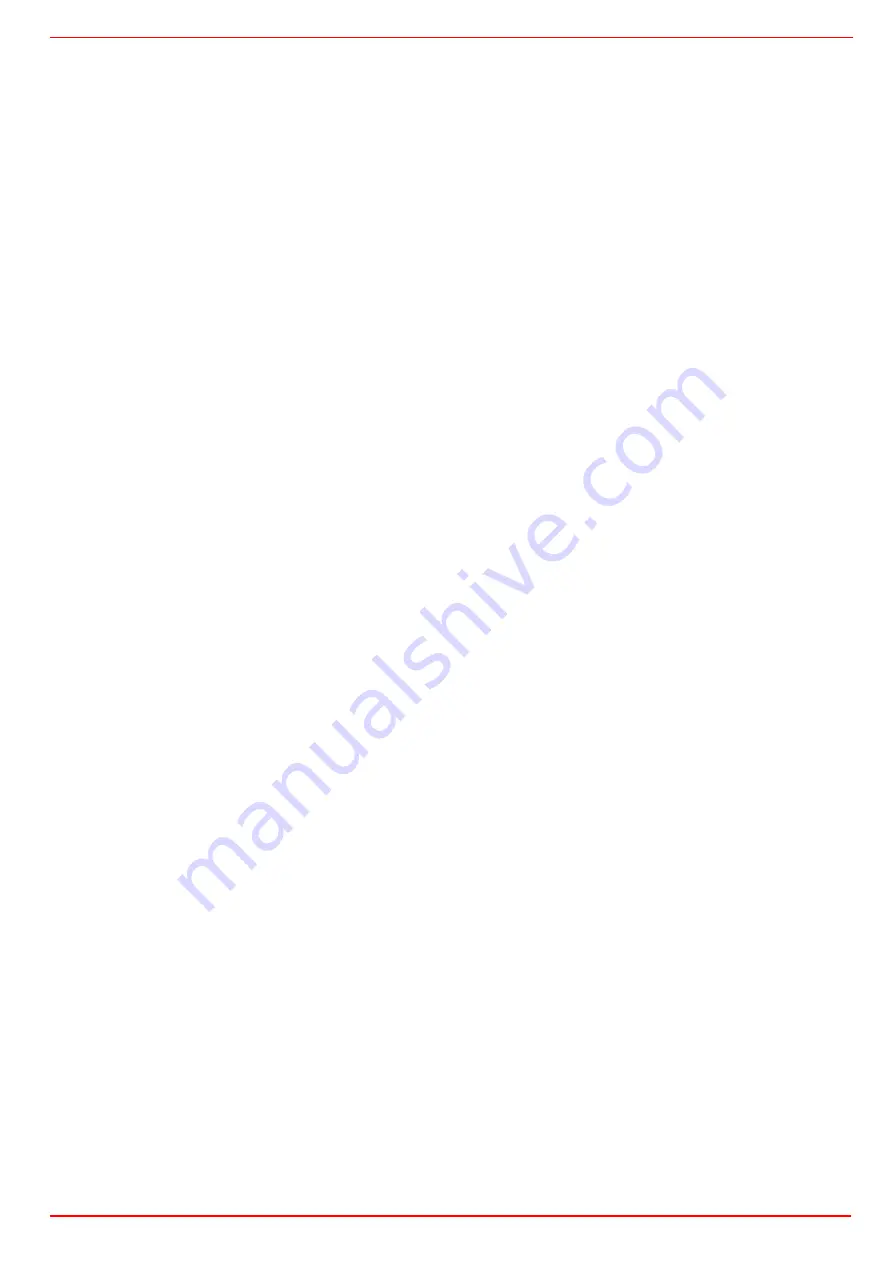
4
3b)
FIRING WITH GAS, LIGHT OIL OR OTHER FUELS
GENERAL
z
The burner shall be installed by qualified personnel and in com-
pliance with regulations and provisions in force; wrong installation
can cause injuries to people and animals, or damage to property, for
which the manufacturer cannot be held liable.
z
Before installation, it is recommended that all the fuel supply system
pipes be carefully cleaned inside, to remove foreign matter that might
impair the burner operation.
z
Before the burner is commissioned, qualified personnel should ins-
pect the following:
a
the fuel supply system, for proper sealing;
b
the fuel flow rate, to make sure that it has been set based on the
firing rate required of the burner;
c
the burner firing system, to make sure that it is supplied for the desi-
gned fuel type;
d
the fuel supply pressure, to make sure that it is included in the range
shown on the rating plate;
e
the fuel supply system, to make sure that the system dimensions are
adequate to the burner firing rate, and that the system is equipped
with all the safety and control devices required by the regulations in
force.
z
When the burner is to remain idle for some time, the fuel supply tap
or taps should be closed.
SPECIAL INSTRUCTIONS FOR USING GAS
Have qualified personnel inspect the installation to ensure that:
a
the gas delivery line and train are in compliance with the regulations
and provisions in force;
b
all gas connections are tight;
c
the boiler room ventilation openings are such that they ensure the air
supply flow required by the current regulations, and in any case are
sufficient for proper combustion.
z
Do not use gas pipes to earth electrical equipment.
z
Never leave the burner connected when not in use. Always shut the
gas valve off.
z
In case of prolonged absence of the user, the main gas delivery
valve to the burner should be shut off.
Precautions if you can smell gas
a
do not operate electric switches, the telephone, or any other item
likely to generate sparks;
b
immediately open doors and windows to create an air flow to purge
the room;
c
close the gas valves;
d
contact qualified personnel.
z
Do not obstruct the ventilation openings of the room where gas
appliances are installed, to avoid dangerous conditions such as the
development of toxic or explosive mixtures.
DIRECTIVES AND STANDARDS
Gas burners
European directives:
- Directive 90/396/CEE - Gas Appliances;
-
Directive 2006/95/EC on low voltage
;
-
Directive
2004/108/CEE
on electromagnetic compatibility
Harmonised standards
:
-UNI EN 676 (Gas Burners;
-CEI EN 60335-1(Household and similar electrical appliances - Safety.
Part 1: General requirements;
- EN 50165 (Electrical equipment of non-electric appliances for house-
hold and similar purposes. Safety requirements.
Light oil burners
European directives:
-
Directive 2006/95/EC on low voltage
;
-
Directive
2004/108/CEE
on electromagnetic compatibility
Harmonised standards
:
-CEI EN 60335-1(Household and similar electrical appliances - Safety.
Part 1: General requirements;
- EN 50165 (Electrical equipment of non-electric appliances for house-
hold and similar purposes. Safety requirements.
National standards
:
-UNI 7824: Monobloc nebulizer burners for liquid fuels. Characteristics
and test methods
Heavy oil burners
European directives:
-
Directive 2006/95/EC on low voltage
;
-
Directive
2004/108/CEE
on electromagnetic compatibility
Harmonised standards
:
-CEI EN 60335-1 Household and similar electrical appliances - SafetyPart
1: General requirements;
- EN 50165 Electrical equipment of non-electric appliances for household
and similar purposes. Safety requirements.
National standards
:
-UNI 7824: Monobloc nebulizer burners for liquid fuels. Characteristics
and test methods
Gas - Light oil burners
European directives:
- Directive 90/396/CEE Gas Appliances;
-
Directive 2006/95/EC on low voltage
;
-
Directive
2004/108/CEE
on electromagnetic compatibility
Harmonised standards
:
-UNI EN 676 Gas Burners
-CEI EN 60335-1(Household and similar electrical appliances - Safety.
Part 1: General requirements;
- EN 50165 Electrical equipment of non-electric appliances for household
and similar purposes. Safety requirements.
National standards
:
-UNI 7824: Monobloc nebulizer burners for liquid fuels. Characteristics
and test methods
Gas - Heavy oil burners
European directives:
- Directive 90/396/CEE - Gas Appliances;
-
Directive 2006/95/EC on low voltage
;
-
Directive
2004/108/CEE
on electromagnetic compatibility
Harmonised standards
:
-UNI EN 676 (Gas Burners;
-CEI EN 60335-1(Household and similar electrical appliances - Safety.
Part 1: General requirements;
- EN 50165 Electrical equipment of non-electric appliances for household
and similar purposes. Safety requirements.
National standards
:
-UNI 7824: Monobloc nebulizer burners for liquid fuels. Characteristics
and test methods
Содержание PG60
Страница 32: ...PG60 G PR ...
Страница 33: ......
Страница 34: ......
Страница 35: ......
Страница 36: ...PG60 G MD ...
Страница 37: ......
Страница 38: ......
Страница 39: ......
Страница 40: ......
Страница 41: ...PG70 PG81 G PR ...
Страница 42: ......
Страница 43: ......
Страница 44: ......
Страница 45: ...PG70 PG81 G MD ...
Страница 46: ......
Страница 47: ......
Страница 48: ......
Страница 49: ......
Страница 53: ......
Страница 54: ......
Страница 55: ......
Страница 56: ......