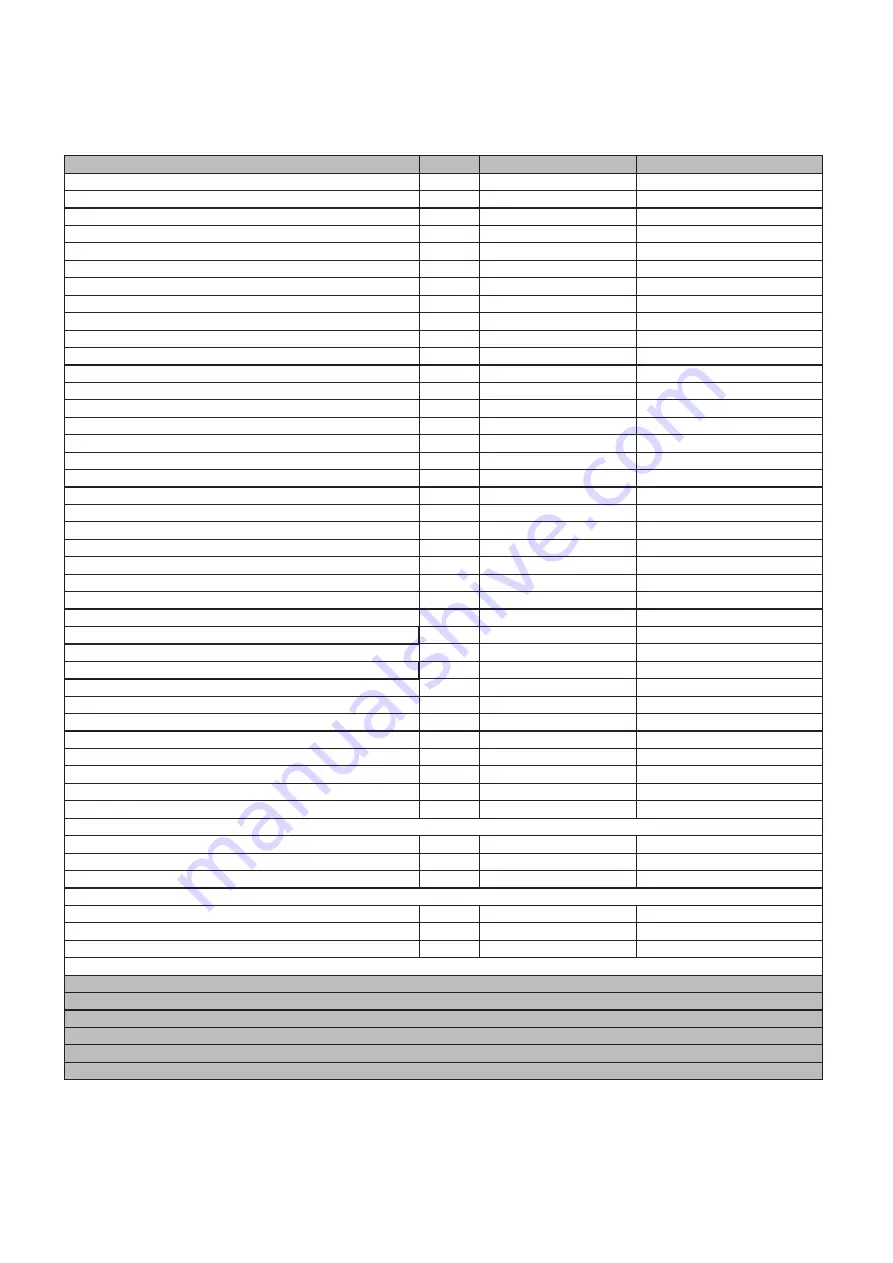
12
KONf 100
KONf 115
Appliance category
II
2H3P
II
2H3P
Modulation Ratio
1 : 5,0
1 : 5,75
Nominal Heat Input on P.C.I. Qn
kW
99,5
115
Minimum Heat Input on P.C.I. Qmin
kW
20
20
Nominal Output (Tr 60 / Tm 80 °C) Pn
kW
98,8
111,5
Minimum Output (Tr 60 / Tm 80 °C) Pn min
kW
19,2
19,2
Nominal Output (Tr 30 / Tm 50 °C) Pcond
kW
105
120,3
Minimum Output (Tr 30 / Tm 50 °C) Pcond min
kW
21,75
21,75
Efficiency at max. output (Tr 60 / Tm 80°C)
%
98,81
97,1
Efficiency at min. output (Tr 60 / Tm 80°C)
%
95,90
95,90
Efficiency at max. output (Tr 30 / Tm 50°C))
%
105,03
104,6
Efficiency at min. output (Tr 30 / Tm 50°C)
%
108,77
108,77
Rendimento al 30% del carico (Tr 30°C)
%
109,3
107,27
Combustion efficiency with nominal load
%
98,05
97,7
Combustion efficiency with minimum load
%
98,28
98,28
Heat loss at casing with burner in operation (Qmin)
%
2,30
2,69
Heat loss at casing with burner in operation (Qn)
%
0,1
0,7
Flue gas temperature tf-ta (min)(*)
°C
35,0
36,0
Flue gas temperature tf-ta (max)(*)
°C
39,4
46,6
Maximum allowable temperature
°C
100
100
Maximum operating temperature
°C
85
85
Flue gas mass flow rate (min)
kg/h
37,71
34,31
Flue gas mass flow rate (max)
kg/h
163,59
184,6
Excess λ air
%
25,53
23
Flue losses with burner in operation (min)
%
1,72
1,87
Flue losses with burner in operation (max)
%
1,95
2,29
Minimum heating circuit pressure
bar
0,5
0,5
Maximum heating circuit pressure
bar
6
6
Water content
l
9
9
Gas Consumption Natural (20 mbar) gas G 20 a Qn
m
3
/h
10,57
12,08
Gas Consumption Natural gas (20 mbar) G 20 a Qmin
m
3
/h
2,11
2,11
Gas Consumption G25 (supply pressure 25 mbar) Qn
m
3
/h
12,3
14,0
Gas Consumption G25 (supply pressure 25 mbar) Qmin
m
3
/h
2,46
2,46
Gas Consumption G31 (supply pressure 37/50 mbar) Qn
kg/h
7,76
8,92
Gas Consumption G31 (supply pressure 37/50 mbar) Qmin
kg/h
1,55
1,55
Max. available pressure at the chimney base
Pa
150
150
Max Condensation production
kg/h
8,46
8,46
Emissioni
CO at Minimum Heat Input with 0% of O2
mg/kWh 140
147
NOx at Nominal Heat Input with 0% of O2
mg/kWh 47
47
NOx Class
5
5
Electrical Data
Voltage/Frequency electric power supply
V/Hz
230/50
230/50
Fuse on main supply
A (R)
4
4
Insulation degree
IP
X5D
X5D
Room Temperature = 20°C
(*) Temperatures detected with the unit in operation (Tr 60 / Tm 80°C)
CO
2
(min/max) See table INJECTORS PRESSURES
Seasonal space heating energy 2009/125 CEE (<=400Kw)
η
s
- see ErP table
Stand-by heat loss
∆T 30°C
- Pstb - see ErP table
Consumption in stand-by - Psb - see ErP table
2.5 - OPERATING DATA ACCORDING TO UNI 10348 and GENERAL FEATURES
For the adjustment data: NOZZLES - PRESSURE - DIAGRAMS - FLOW RATES - CONSUMPTION refer to the paragraph ADAP
-
TATION TO OTHER TYPES OF GAS.
Содержание KONf 115
Страница 1: ...100 115 KONf E N G L I S H INSTALLATION AND SERVICING MANUAL...
Страница 10: ...10 2 3 DIMENSIONS Front view View from above Left Side view...
Страница 38: ...38...
Страница 39: ...39...