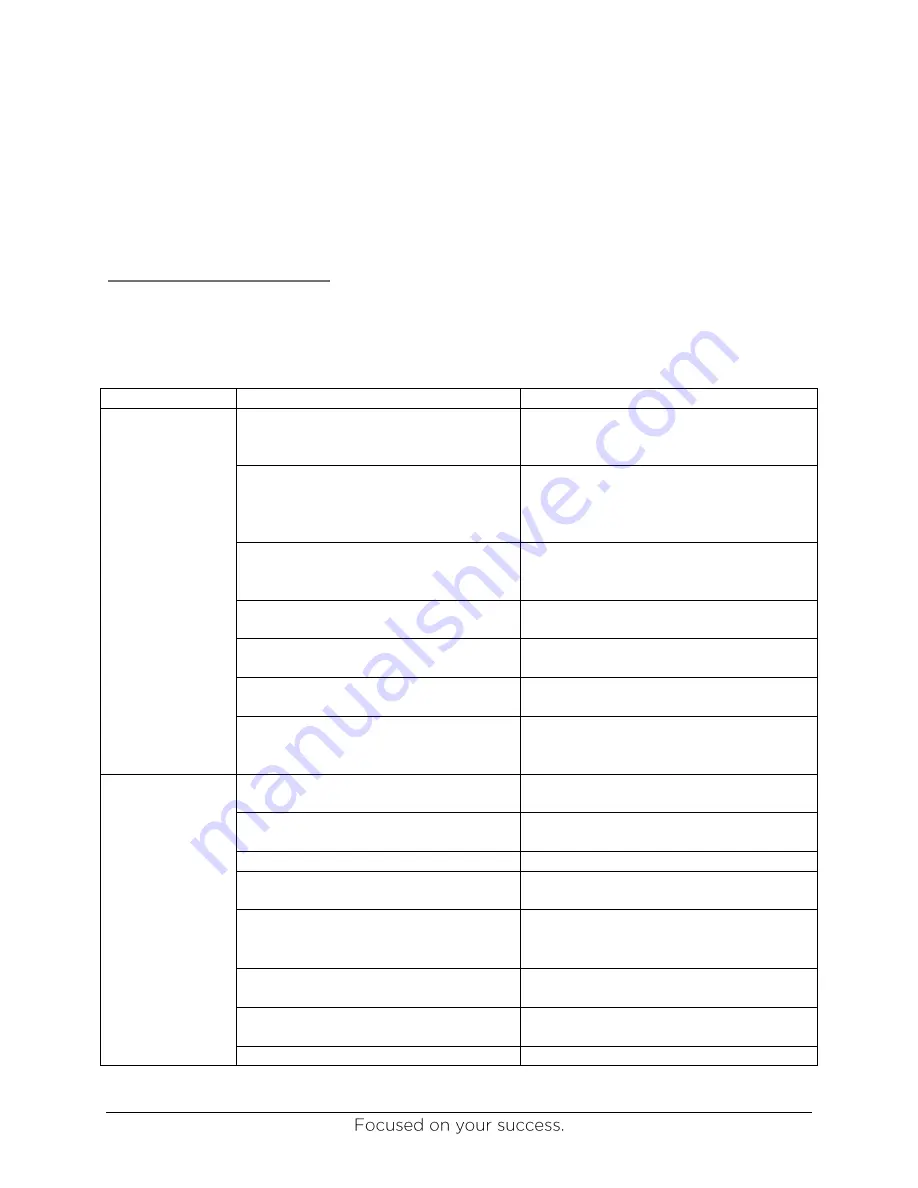
www.ultraoptics.com
page 19
Maintenance
The 44R system is designed to provide many years of reliable and efficient processing of
ophthalmic lenses. Its ability to provide this service is significantly enhanced with proper
maintenance. Due to the many integrated systems within the 44R, it is highly recommended
that service and maintenance is only done by trained technicians. Failure to do so could result
in damaged equipment, increased down time, or injury of personnel.
Scheduled Maintenance
The following table should be used as a guide for performing regular preventative maintenance
on the 44R to maintain ultimate system efficiency and up-time. It is expected that the user of
this machine is capable and performs the following maintenance items at the scheduled
intervals.
Frequency
Maintenance Item
Description
Daily
Wipe wash bowl and drying station
bowl deck.
Dampen a clean cloth with IPA or
Ultra Optics Lens Cleaner and clean
out the inside of the wash bowl.
Wipe inside of coating bowl
Use a lint-free rag dampened with
acetone or IPA to wipe out the inside
of the coating bowl and clean the
screen.
Empty drain tee and clean screen
On bottom of wash bowl is a tee trap.
Remove the bottom plug and clean
out any debris from the trap.
Check coating level in reservoir
Refill as needed such that the coating
level is above the halfway mark.
Check coating fountain height
Fountain should come up to the top
edge of coating bowl.
Check lamp hours and intensity
Lamp should be replaced every 1000
hours or if intensity is less than 70%.
Confirm wash pump is properly
primed
During a wash cycle, count the
number of audible “beats” by the wash
pump. It should “beat” 34 times.
Weekly
Inspect suction cups for debris or
deterioration
Replace as necessary
Check spindle speeds
Refer to setting spindle speed
procedure on page 37 of this manual.
Check lamp cycle time
Should be at 25 seconds
Check air pressure regulator
Both regulators should be adjusted to
read 80 psig.
Clean out top Hepa filter housing
Replace top pre-filter as needed using
a
10” x 10” x 2” filter.
P/N 3923T999
Check vacuum pressure
Go to
Vacuum Diagnostic
screen on
HMI.
Inspect complete vacuum chuck
assembly for dried coating or debris
Clean as needed.
Check air dryer filters
Replace all three if: