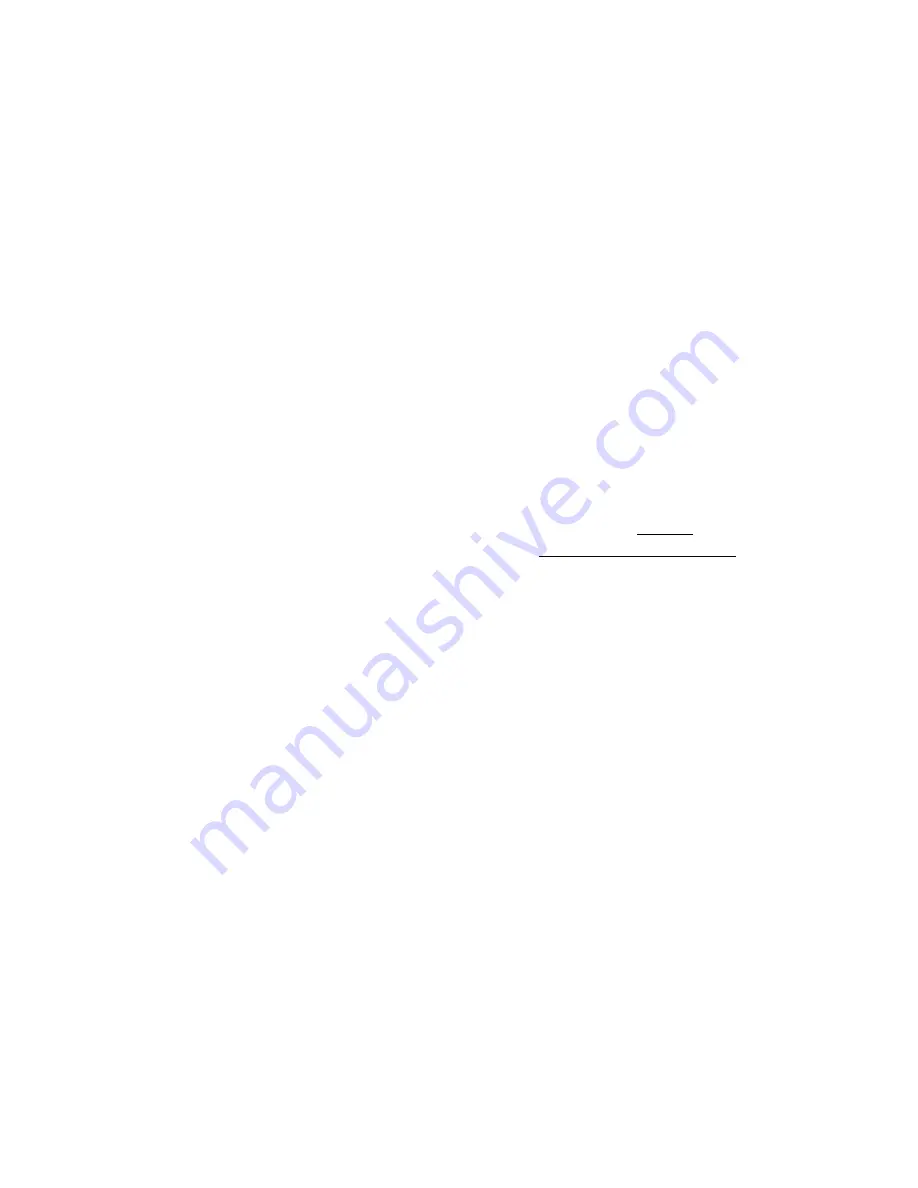
3.
Once the engine has been turned off, disconnect the coil wires from the coil of
the engine, and remove all of the spark plugs.
4.
Remove the oil dipstick, radiator cap, and disconnect one end of the PCV hose.
If the engine has a carburetor, remove the air cleaner and open the carburetor
throttle all the way. If the engine is fuel injected, remove the air cleaner or
throttle.
5.
Remove all of the spark plugs, and position the cylinder to be tested at TDC (Top
Dead Center) on the compression stroke so that both valves are closed. The
following indicates how to properly position the cylinder:
A.
The rotor points to cylinder coming up on compression.
B.
A “whistle”(not included) is available from automotive suppliers that whistles
on the compression stroke and stops at approximately TDC. The whistle
can be quickly coupled to the Extension Hose (part #6) of the Cylinder
Leakage Tester.
6.
Make sure the Regulator Knob (part #5) is turned fully counterclockwise, and
connect the Cylinder Leakage Tester to an air compressor.
NOTE: set
the
air
compressor’s regulator from 45 to 100 PSI. Do not exceed 100 PSI.
(See Assy. Diagram.)
7.
Turn the Regulator Knob (part #5) clockwise until its’ Gauge reads zero at the
end of the Yellow Band.
(See Assy. Diagram.)
8.
Hand screw the Extension Hose (part #6) into the spark plug hole. Then, con-
nect the male coupler end of the Extension Hose onto the Cylinder Leakage
Tester.
(See Assy. Diagram.)
9.
The amount of leakage will now show on the Leakage Gauge (part #4) as a
percentage loss. Follow the instructions given in the “
PRODUCT OVERVIEW”
section to locate the source of the leakage if it is excessive.
10.
Test the remaining cylinders, and compare leakage to determine which cylinders
are bad and why.
SKU 04317
PAGE 6
INSPECTION, MAINTENANCE, AND CLEANING
1.
BEFORE EACH USE,
inspect the general condition of the Cylinder Leakage
Tester. Check for cracked or broken parts, damaged Extension Hose (part #6),
Brought to You by Augusta Flint