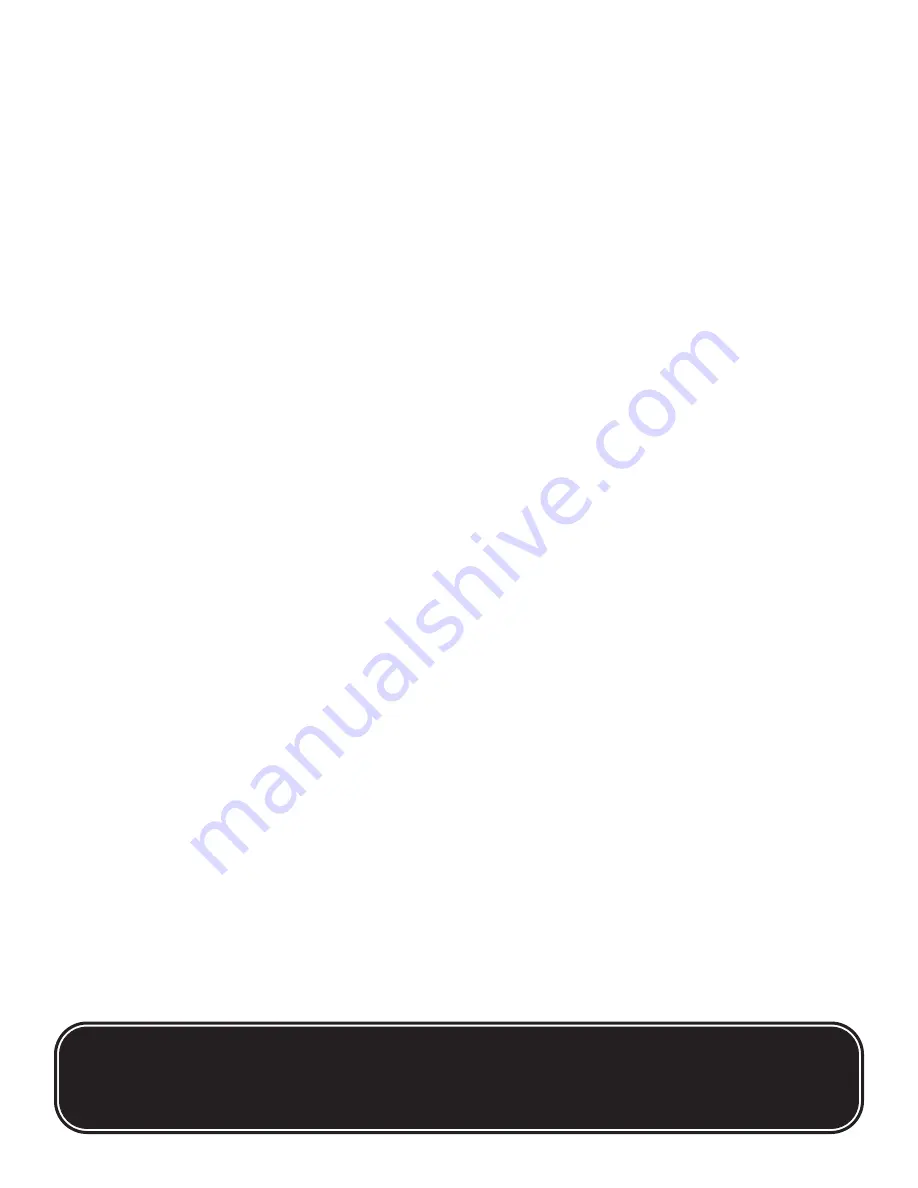
U.S. BLIND STITCH MACHINE CO.
IS A DIVISION OF NEW YORK SEWING MACHINE ATTACHMENT CORP.
2011-15 85th Street, North Bergen, NJ 07047
•
Web: www.usblindstitch.com
Tel: 201-809-2009 • 1-800-225-2852 • FAX: 201-861-9201 • e-mail: [email protected]
11
7. After completing the adjustment, thoroughly oil the feed lever and eccentric, particularly in the
area indicated by “D” in Figure 5; and replace the side cover.
I. REPLACING THE NEEDLE
1. U.S. needles are designed and manufactured specifically to meet the precise sewing requirements
of the U.S. BLIND STITCH MACHINES. Because of the importance of a properly designed needle
in achieving consistent high quality stitching, it is extremely important that only GENUINE U.S.
NEEDLES be used at all times.
2. When it becomes necessary to replace worn or damaged needles, the following procedure
should be followed:
a. Turn the penetration dial to the right (“Less”) three or four numbers to insure that the rib is
lowered sufficiently to clear the needle.
b. Loosen the needle clamp screw (item “C” in Figure 1), slide the clamp rearward sufficiently
to release the old needle, and remove and discard it. Insert the new needle and push it up into the
groove of the needle lever as far as it will go. Make sure that the flat on the shank of the needle
faces rearward and the needle is properly seated in the groove. Tighten the needle clamp screw
and turn the handwheel slowly making sure that the needle passes lightly over the needle guide on
the presser foot and clears the looper. Readjust the needle penetration as described in a previous
section, prior to resuming operation.
3. When it becomes necessary to replace worn or damaged needles, the following procedure
should be followed:
a. Turn the penetration dial to the right (“Less”) three or four numbers to insure that the rib is
lowered sufficiently to clear the needle.
b. Loosen the needle clamp screw (item “C” in Figure 1), slide the clamp rearward sufficiently
to release the old needle, and remove and discard it. Insert the new needle and push it up into the
groove of the needle lever as far as it will go. Make sure that the flat on the shank of the needle
faces rearward and the needle is properly seated in the groove. Tighten the needle clamp screw
and turn the handwheel slowly making sure that the needle passes lightly over the needle guide on
the presser foot and clears the looper. Re-adjust the needle penetration as described in a previous
section, prior to resuming operation.
4. NEEDLES
NEEDLE SIZES AVAILABLE
Use Genuine U.S. BLIND STITCH Needles for Best Results
Long Needles – System 251
Regular Point Sizes
Ball Point Sizes
Spear Point Sizes
00
10
10
10
15
15
15
20
20
20
25
25
25
30
30
35
35
65
40
55
Short Needles Also Available – Ask For List
From
the
library
of:
Diamond
Needle
Corp