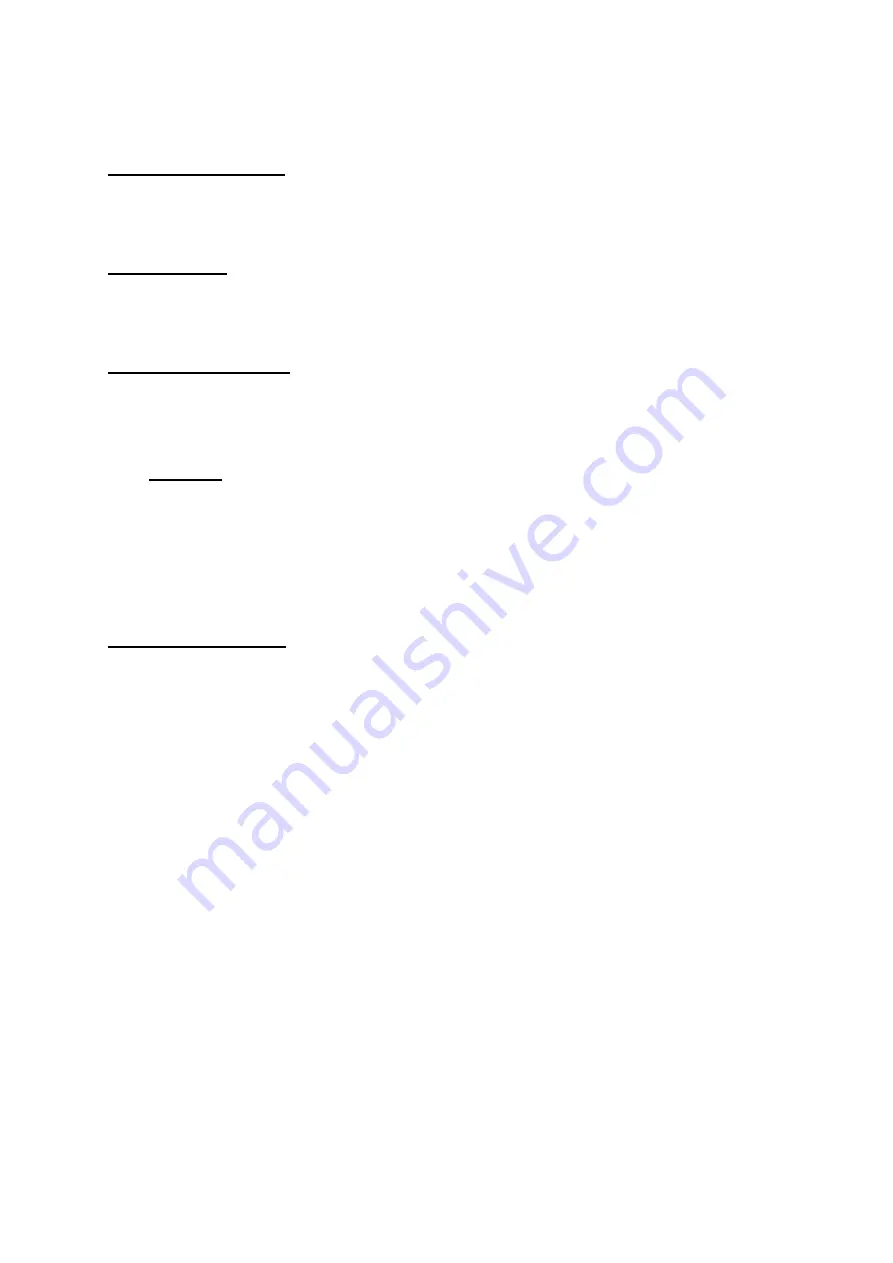
10
3. Placement in operation
3.1 Connections and fuel
−
Use regular petrol (unleaded)
−
Connect cooling water hose or fill water tank
3.2 Water supply
−
Connect the external water hose to the connecting piece of the floor saw
−
Connect the water tank`s connecting piece for diamond blade cooling
3.3 Saw blade installation
−
Take off saw blade protective hood
−
Remove flange nut and thrust washer
−
Install saw blade
Important!
* Flange surfaces must be clean
* Match direction of rotation of the saw blade (arrow on the blade) with arrow
on the saw hood
(synchronized saws)
−
Install thrust washer and flange nut
−
Put on saw blade protective hood
3.4 Preparations for start
−
Move the Floor Saw into position
* Guide bar disk and saw blade are over the cut line
−
Open water faucet
−
Start petrol motor (see operating manual for motor)
−
Set motor to full throttle
−
Slowly initiate downward movement with crank – until the saw blade begins to cut.
Attention!
Is the saw blade getting enough cooling water?
−
Set cutting depth indicator to “zero”
−
Dip saw blade down to the desired cutting depth
−
Slowly start feed movement