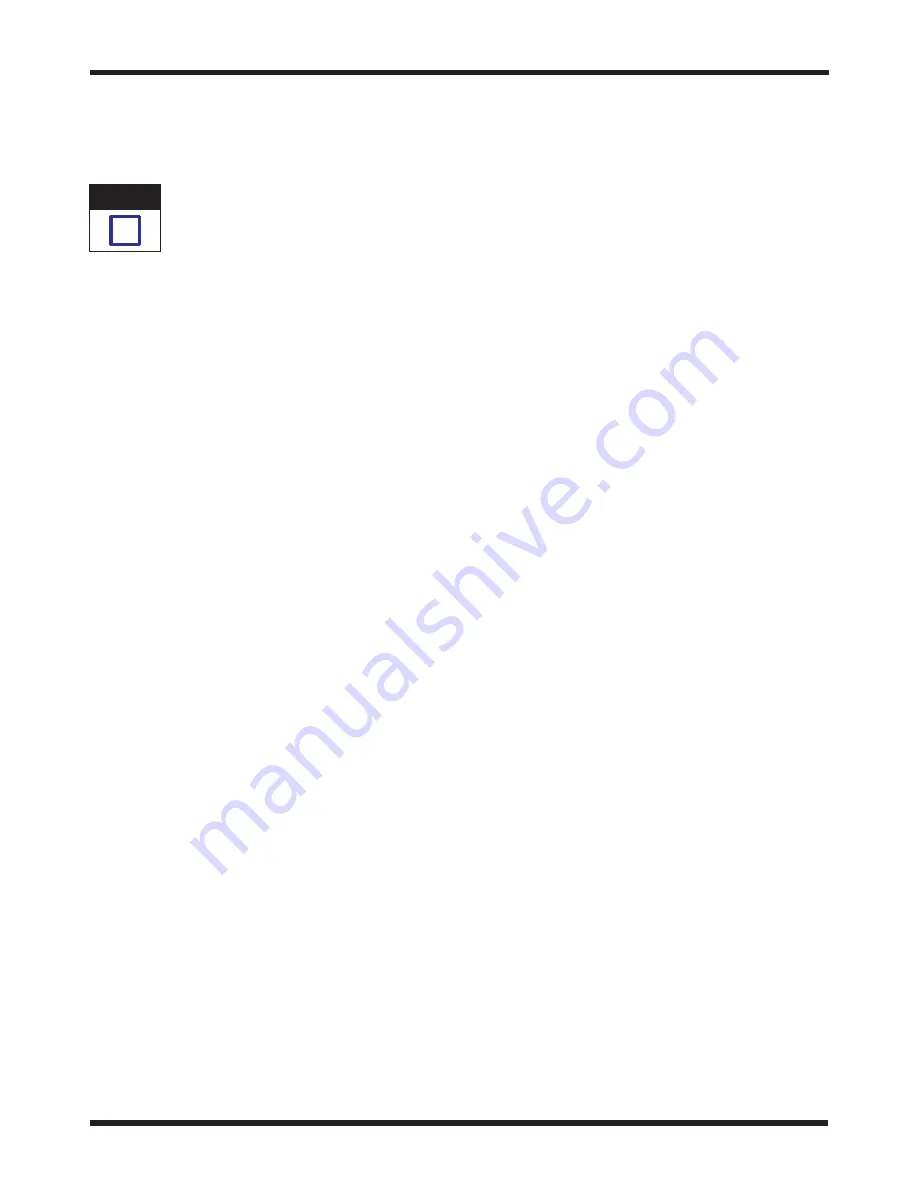
408-1610
T"-HEAD Crimping Tools
Rev G
8 of 10
Tyco Electronics Corporation
7.4. Gaging the Crimping Chamber
Each tool is inspected for proper die closures before
packaging. An inspection should be performed
periodically to check the tool die closures for
excessive wear.
The following plug gaging information for
insulation crimping chambers is provided for
customers specifically requiring this information.
If plug gaging is not required, inspect the die
closures using an alternate procedure, i.e.,
performing the Insulation Crimp Adjustment"
(see Section 5) and Visual Inspection" (see
Paragraph 7.2).
This inspection requires the use of plug gages
conforming to the dimensions listed in Figures 9 and
10. Tyco Electronics does not manufacture or market
these gages.
To gage the crimping area(s), refer to Figure 11 and
proceed as follows:
1. Clean oil or dirt from the crimping chamber and
plug gage.
2. Close handles of tool until wire barrel dies are
bottomed. Do not apply additional pressure to tool
handles.
3. With wire barrel dies bottomed, inspect the wire
barrel crimping chamber using the proper plug
gage. Lift the spring–loaded locator up and hold
gage in straight alignment with the crimping
chamber. Carefully try to insert, without forcing, the
GO element. See Figure 11, Detail A. The GO
element must pass completely through the
crimping area.
4. Try to insert the NO–GO element. The NO–GO
element may enter partially, but must not pass
completely through the crimping area.
5. Set insulation adjustment indicator in Position 1.
Measure both insulation crimping chambers with
the proper GO plug gages in the same manner as
Steps 2 and 3. See Figure 11, Detail B.
6. Set insulation adjustment indicator in Position 4.
Measure both insulation crimping chambers with
the proper NO–GO plug gages in the same
manner as Steps 2 and 4. See Figure 11, Detail B.
If the crimping areas conform to the gage inspection,
the tool is considered dimensionally correct. If the
crimping areas do not conform to the inspection, the
tool must be repaired. Refer to Section 8,
REPLACEMENT AND REPAIR.
7.5. Ratchet Control Inspection
Obtain a .025–mm [.001–in.] shim that is suitable for
checking the clearance between the bottoming
surfaces of the crimping dies. To inspect the
CERTI–CRIMP hand crimping tool ratchet control:
1. Perform a crimp using the largest wire size for
your tool.
2. While holding the wire in place, squeeze the tool
handles together until the ratchet releases. Hold
the tool in this position, maintaining just enough
pressure to keep the dies closed.
3. Check the clearance between the bottoming
surfaces of the crimping dies. If the clearance is
.025 [.001] or less, the ratchet is satisfactory. If
clearance exceeds .025 [.001], the ratchet is out of
adjustment, and must be repaired. Refer to Section
8, REPLACEMENT AND REPAIR. If the tool
conforms to these inspection procedures, lubricate
it with a THIN coat of any good SAE 20 motor oil
and return it to service.
8. REPLACEMENT AND REPAIR
Replacement parts are listed in Figure 12. Parts other
than those listed in Figure 12 should be replaced by
Tyco Electronics to ensure quality and reliability of the
tool. Order replacement parts through your Tyco
Electronics Representative, or call 1–800–526–5142,
or send a facsimile of your purchase order to
1–717–986–7605, or write to:
CUSTOMER SERVICE (38–35)
TYCO ELECTRONICS CORPORATION
P.O. BOX 3608
HARRISBURG, PA 17105–3608
For tool repair service, please contact a Tyco
Electronics Representative at 1–800–526–5136.
9. REVISION SUMMARY
Since the previous release of this sheet, the following
changes were made:
S
Updated document to corporate requirements
S
Added NOTE to Figure 12
NOTE
i