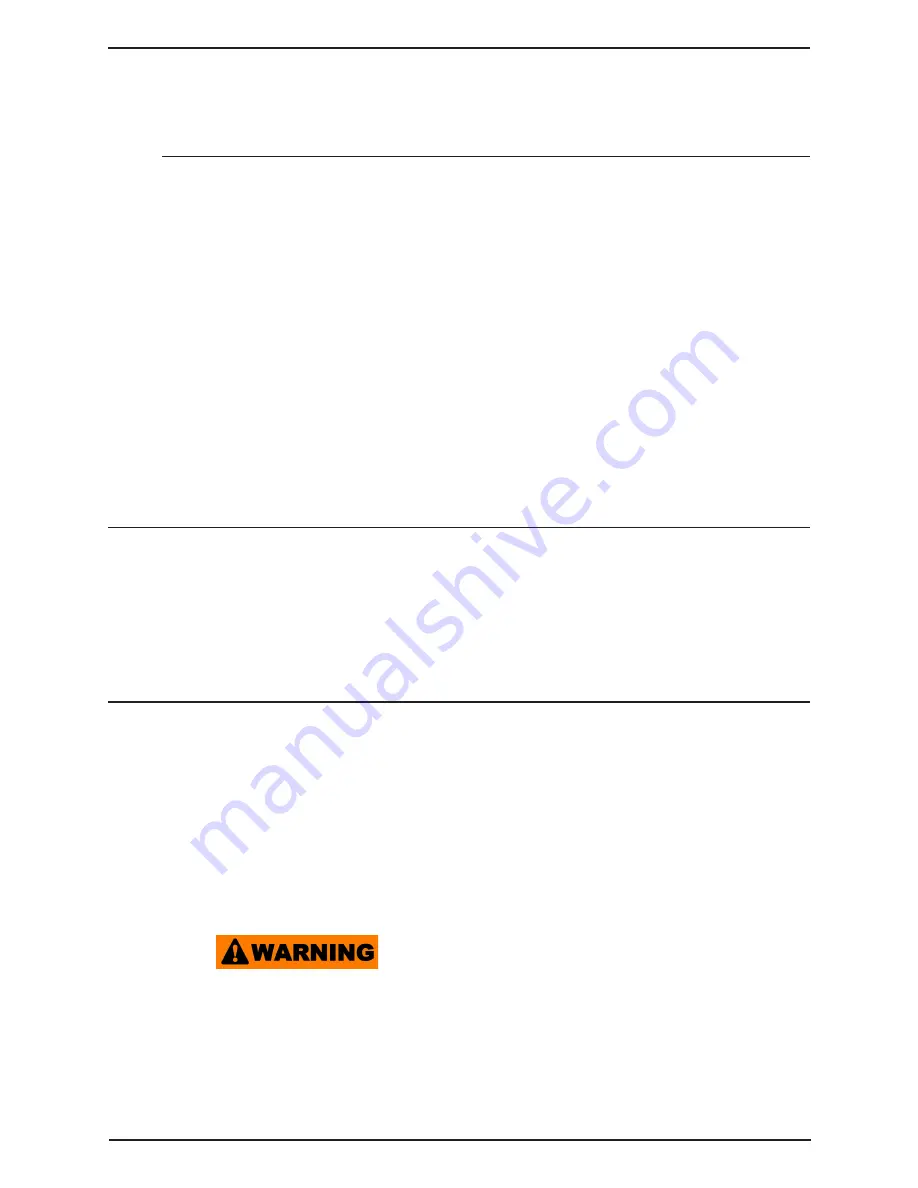
2
©2019 Twin Disc, Incorporated
Introduction
Pump Drive Operator’s Manual #1033752
Parts Shipment
Furnish the complete shipping information and postal address. All parts
shipments made from the factory will be FOB factory location, USA. State
specifically whether the parts are to be shipped by freight, express, etc. If
shipping instructions are not specified, the equipment will be shipped the
best way, considering time and expense. Twin Disc, Incorporated will not
be responsible for any charges incurred by this procedure.
Twin Disc, Incorporated, having stipulated the bill of material number on
the unit’s nameplate, absolves itself of any responsibility resulting from
any external, internal or installation changes made in the field without
the express written approval of Twin Disc. All returned parts, new or old,
emanating from any of the above-stated changes will not be accepted for
credit. Furthermore, any equipment which has been subjected to such
changes will not be covered by a Twin Disc warranty.
Safety
Safe practices must be employed by all personnel operating and servic-
ing this unit. Twin Disc, Incorporated will not be responsible for personal
injury resulting from careless use of hand tools, lifting equipment, power
tools, or unaccepted maintenance/operating practices.
Important Safety Notice
Because of the possible danger to person(s) or property from accidents
which may result from the use of manufactured products, it is important
that correct procedures be followed. Products must be used in accor-
dance with the engineering information specified. Proper installation,
maintenance, and operation procedures must be observed. Inspection
should be made as necessary to assure safe operations under prevailing
conditions. Proper guards and other suitable safety codes should be pro-
vided. These devices are neither provided by Twin Disc, Incorporated nor
are they the responsibility of Twin Disc, Incorporated.
To prevent accidental starting of the engine when performing routine
maintenance, disconnect the battery cables from the battery and
remove ignition key from the switch.
Содержание AM080
Страница 1: ...Document Number 1033752 Pump Drive Model AM080 Operator s Manual TWIN DISC INCORPORATED T D WIN ISC ...
Страница 3: ...Document Number 1033752 Revision B May 2019 Pump Drive Operator s Manual ...
Страница 10: ...4 2019 Twin Disc Incorporated Introduction Pump Drive Operator s Manual 1033752 NOTES ...
Страница 14: ...8 2019 Twin Disc Incorporated Operation Pump Drive Operator s Manual 1033752 Table 2 Tower Ports ...
Страница 22: ... 1033752 TWIN DISC INCORPORATED RACINE WISCONSIN 53403 U S A 262 638 4000 262 638 4482 FAX WWW TWINDISC COM ...