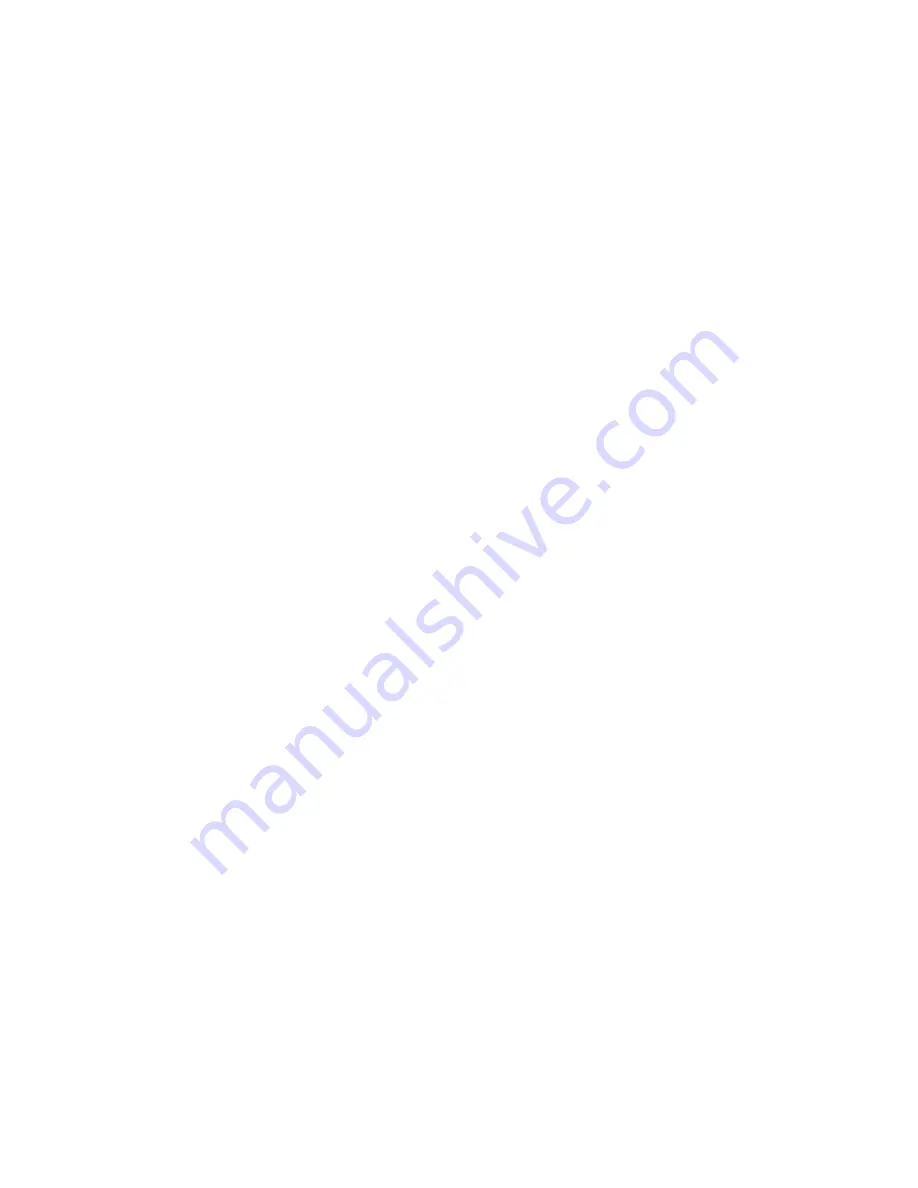
Page 5 of 18
Proper Installation
Unsatisfactory pump installations are usually characterized by poor suction conditions for the specific liquid being handled. Suction
conditions should be minimized to prevent vaporization of the liquid. If vacuum conditions force the liquid to vaporize, cavitation will
occur, resulting in loss of capacity, premature wear and noisy operation. When handling high viscosity liquids, the speed of the pump
must be reduced and the size of the lines increased to prevent cavitation.
Note:
Pipeline friction increases at a rapid rate with an increase in viscosity. For a given pump and motor, larger pipelines are
necessary to maintain the same pump pressure when changing from a thin fluid to a thick one.
Tuthill 4000 Series pumps are supplied with both ports on the same plane. Pumps with this type of porting arrangement should always
be installed with the ports facing upward to insure proper priming. If it is necessary to install the pump with the ports pointing to either
side, it is recommended that the top port be the suction port. This will prevent gravity-induced drainage of fluid through the suction port.
When pipes are installed, an inverted “U” bend should be incorporated into the suction line close to the pump for priming purposes.
Because of its size, the 4108/4128 pump will not mount onto a NEMA 48 frame motor unless the motor is shimmed approximately ¼”.
Viewing the pump from the shaft end, the inlet port is on the right for clockwise rotation and on the left for counter-clockwise rotation.
On pumps with built in relief valves, the adjusting screw of the valve must always be located on the suction side of the pump. Pumps
should be filled with oil at installation and should never be allowed to run dry.
Every pump installation should have a good foundation. Its structure should be sufficiently strong to hold the pump rigid and to absorb
any strain or shock that may be encountered. The installation should be leveled, checked for proper piping alignment, and then
fastened securely.
Method of Drive
Direct drive through a traditional flexible coupling is recommended. However, do not expect the flexible coupling to compensate for
misalignment. Contact the coupling manufacturer to determine the maximum amount of misalignment to which the coupling can be
subjected.
4100 Series pumps can be driven in either direction of rotation, unless outfitted with an internal relief valve. The seal chamber
communicates with the neutral zone and therefore the seal is subjected to approximately one half of the discharge pressure.
All 4300 Series pumps are directional. Rotation must be specified at the time of order. The seal chamber communicates with the suction
side and therefore the seal/packing is subjected to approximately one half of the discharge pressure.
All pump and motor units must be properly aligned during assembly and periodically checked since misalignment may occur later due
to abuse or other conditions. Pipe strain can force the pump and motor shafts out of alignment. Therefore, all piping to the pump must
be properly supported. Do not allow the pump to act as a pipe support.
Provide for proper expansion of pipes when handling hot liquids. Allow pump to reach operating temperature slowly. Rapid temperature
change can result in damage to the cast iron components.
•
Never align a pump and motor supplied with a pin type coupling without first removing the pins
•
Never depend upon sight or feel. Use proper gauges when aligning the pump
•
Never operate the pump without all guards in place.