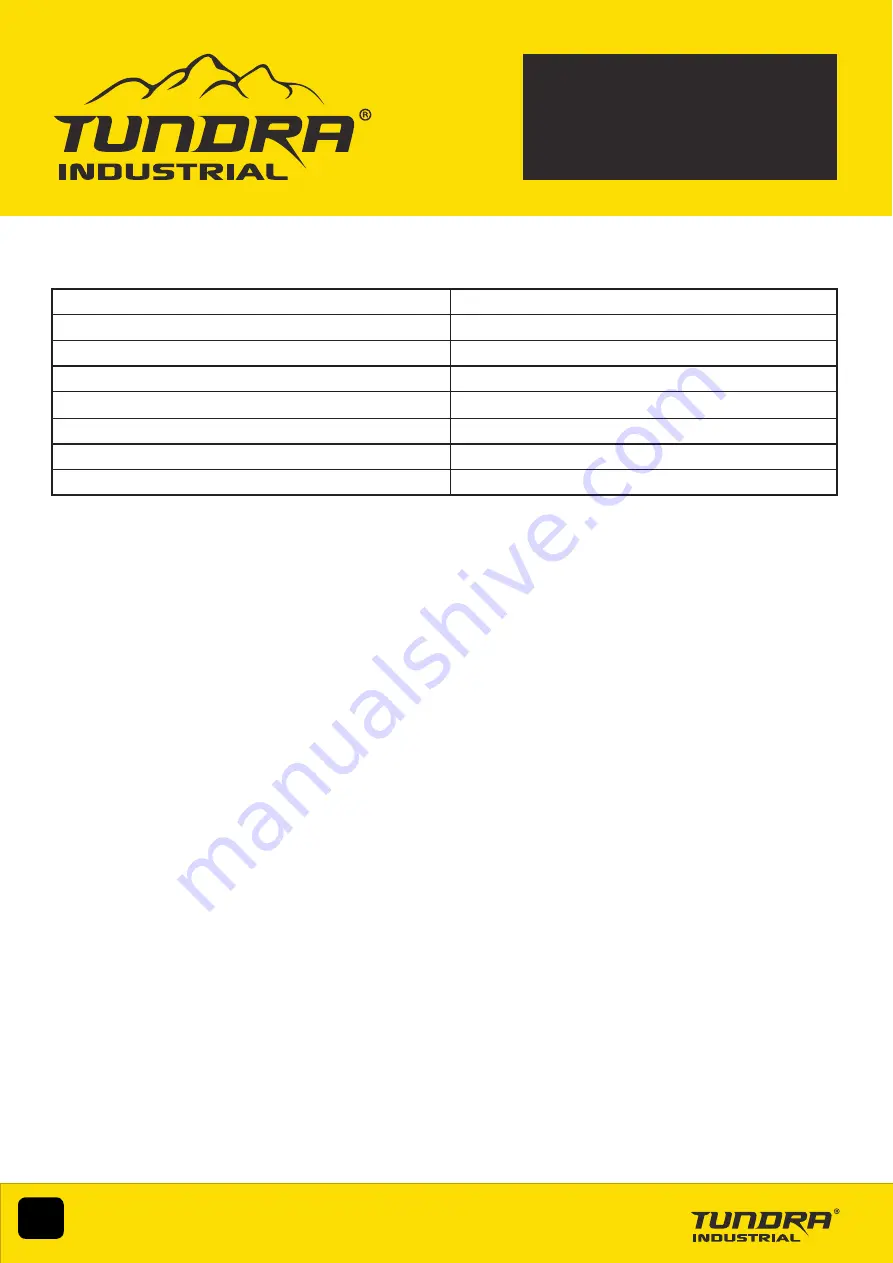
USER MANUAL
4
TUNSHPR30
2. SPECIFICATIONS
Model Number
TUNSHPR30
Maximum Load:
30 Tonne
Ram Stroke:
152mm / 5.9"
Lateral Ram Travel:
200mm
Operating Range:
40 -1050mm
Rack / Working Width
535mm / 28.5"
Weight:
164kg
Assembled Dimensions: (L x W x H)
795 x 700 x 1801mm
3. DESCRIPTION
This industrial bench shop press is designed for automotive, engineering workshops and repair shops where pressing, bending,
straightening and forming is required. Features include:
•
H-frame 30 Tonne hydraulic shop press
•
Sliding ram mechanism with V-blocks
•
Floor mounting type with industrial grade hydraulic system
•
Fully-welded steel frame for maximum rigidity and strength
•
Manual hand pump offers more control for delicate applications
4. ASSEMBLY
Use the parts list and exploded drawing included on the following pages as a reference to help you to assemble this equipment.
•
Remove all components from the packaging and ensure that anything stowed within the main frame is removed before the
frame is raised to the vertical position.
•
The base sections (feet) and supports must be attached before the frame is raised into the vertical position.
•
Attach a base section
(05)
to both posts and lower cross member
(07)
using bolts
(08)
, washers
(02)
, lock washers
(03)
and
nuts
(04)
.
•
Attach two supports
(06)
diagonally to each of the post and base sections. Use bolts
(01),
washers
(02)
, lock washers
(03)
and nuts
(04)
at each end of the supports. (See inset
Fig.2
)
•
Lifting from the upper cross members end, lift the press into an upright position.
•
WARNING!
- Ensure help is available and use slings and a suitable hoist or gantry to raise the press to an upright position.
•
Insert the lower two bed frame pins
(09)
at the level required into the holes in each of the posts, ensuring that they are both
on the same level. With the help of an assistant insert the bed frame
(11)
into the press frame and rest it onto the pins. Attach
a circlip
(10)
to each end of each lower pin. Insert the two upper pins
(09)
through both the bed frame and the posts and attach
a circlip
(10)
to each end of each upper pin.
•
Within the right hand end of the upper cross members is a platform to which the pump assembly
(32)
should be attached us-
ing three bolts
(18)
and three washers
(02)
. (See inset
Fig.4
).
•
Bolt the gauge fitting
(22)
to the upper cross member using a nut
(24)
. Screw the pressure gauge
(13)
onto the fitting ensuring
you include the nylon sealing ring
(23)
. Attached to the pump is a hydraulic hose which should be connected to the back of the
gauge. (See inset
Fig.3
).
•
The sliding ram assembly is factory mounted to the upper cross members. The hydraulic hose
(27)
is already attached to the
ram. Connect the free end
(A)
to the union on the pump (also labelled
'A'
on the diagram on the opposite page).
•
Slide the two handles
(28 & 17)
into their respective sockets and retain in place with bolts
(31)
.
•
Place the two heel blocks
(12)
onto the bed frame
(11)
Содержание TUNSHPR30
Страница 1: ...30 TONNE HYDRAULIC SHOP PRESS USER MANUAL TUNSHPR30 ...
Страница 5: ...5 USER MANUAL TUNSHPR30 ...
Страница 9: ...9 USER MANUAL TUNSHPR30 ...
Страница 11: ...11 USER MANUAL TUNSHPR30 ...
Страница 16: ......