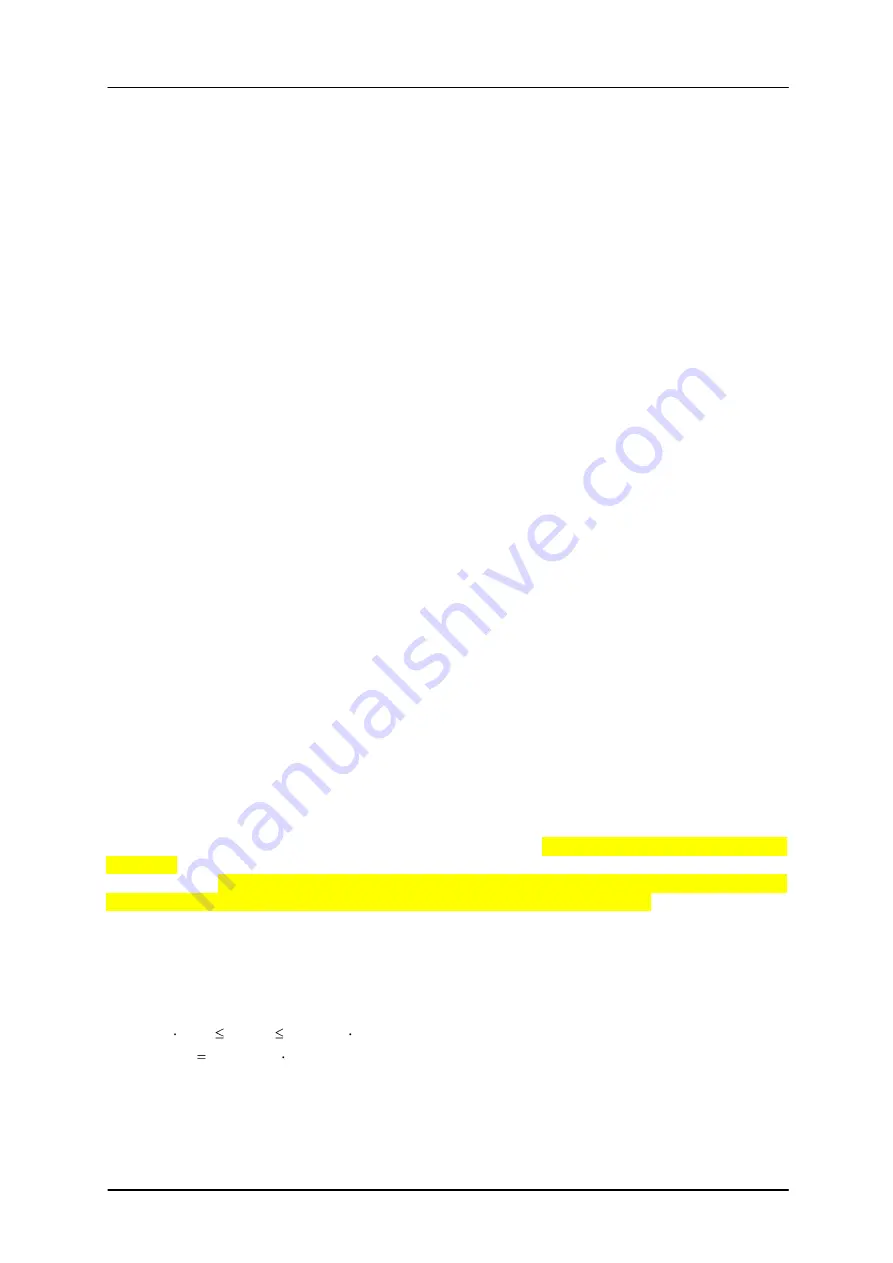
TMCM-078 Manual (V1.03 / September 10th, 2008)
17
Copyright © 2008, TRINAMIC Motion Control GmbH & Co. KG
If in doubt, please start with a lower supply voltage and check motor heating when raising the
voltage.
5.2
Power Supply Requirements
The power supply voltage shall be in the limits as given in the chapter 4 under operational ratings.
Please note that there is no protection against reverse polarity or too high voltage. The power supply
typically should be within a range which fits the motor requirements, as described in chapter 5.1.1.
When using supply voltages near the upper limit, a regulated power supply becomes a must. Please
ensure, that enough power filtering capacitors are provided in the system (1000µF for each ampere of
RMS motor current or more recommended), in order to absorb mechanical energy fed back by the
motor in stalling conditions. In larger systems a zener diode circuitry might be required, when motors
are operated at high velocities.
The power supply should be designed in a way, that it supplies the nominal motor voltage at the
desired maximum motor power. In no case shall the supply value exceed the upper / lower voltage
limit. To ensure reliable operation of the unit, the power supply has to have a sufficient output
capacitor and the supply cables should have a low resistance, so that the chopper operation does not
lead to an increased power supply ripple directly at the unit. Power supply ripple due to the chopper
operation should be kept at a maximum of a few 100mV.
Therefore we recommend to
a)
keep power supply cables as short as possible
b)
use large diameter for power supply cables
c)
if the distance to the power supply is large (i.e. more than 2-3m), use a robust 4700µF or
similar additional filtering capacitor located near to the motor driver unit. Choose the
capacitor voltage rating fitting to the maximum operating voltage.
The overall power rating mainly depends on the motor used and on the mechanical output power, i.e.
the motor velocity and desired torque. As a thumb rule, a 42mm class motor will require a 10W (short
motor) to 20W (long motor) power supply, while a 57mm motor will require 15W to 30W, when
operated at maximum rated current and low velocities. Operation at very high velocities will increase
the power demand up to the double value.
5.2.1
Operating Modes
5.2.1.1
Operating Mode 0 (SPI) / Default Mode
In this mode, the motor coil current is regulated on a chopper-cycle-by chopper-cycle bias. This is the
standard operating mode for most motor drivers. It brings a medium microstep resolution of 16
microsteps and typically works good with most motors and a high range of supply voltage and motor
current settings. A resolution of up to 64 microsteps can be simulated but the motor precision is only
slightly improved compared to 16 microsteps and the same as with 32 microsteps.
The maximum supply voltage (V
S
) of the motor must not exceed 22-25 times the nominal motor
voltage (V
N
), regarding the multiplication of I
COIL, MAX
and R
MOTOR
. A higher value would lead to an excess
of motor rating.
The minimum supply voltage has to be above two times the nominal motor voltage.
MOTOR
MAX
,
COIL
N
N
S
N
R
I
V
V
25
...
22
V
V
2
It uses a chopper frequency of about 36kHz.