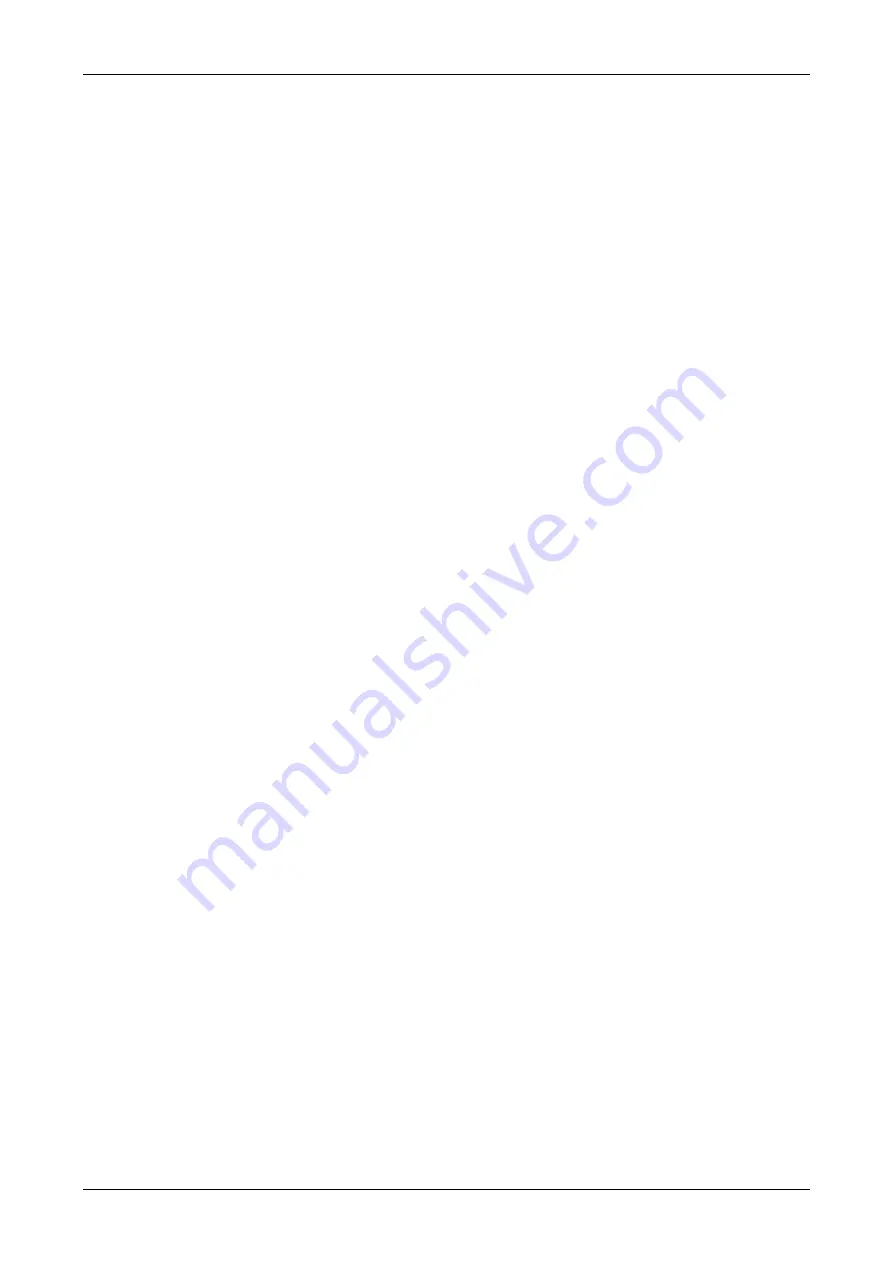
TMCM-111-56 Manual
13
Copyright © 2006, TRINAMIC Motion Control GmbH & Co. KG
5.1.4 TMC249 Motor Driver
The stepper motor drivers used on the TMCM-111-56 module is the TMC249 chip. It controls the current for
the two phases of the stepper motor. It is extended for 64x microstep operation and with high current
MOSFETs plus driver circuitry.
Inspite of the power dissipation of the MOSFETs being very low, some cooling is needed in a typical setup
due to the compact construction. The coils will be switched off automatically when the temperature or the
current exceeds the limits and automatically switched on again when the values are within the limits. Do
not operate at the thermal limit for extended periods of time.
5.2 Power Supply
The TMCM-111-56 is equipped with a switching voltage regulator that generates the 5V supply voltage for
the digital components of the module from the motor power supply. So only one supply voltage is needed
for the module. The power supply voltage can be 15 to 36 V DC. A higher voltage gives higher motor
dynamics. Please note that there is no protection against reverse polarity or too high voltage. Thus,
especially when operating at 36V, a regulated power supply is mandatory.
The power supply should be designed in a way, that it supplies the nominal motor voltage at the desired
maximum motor power. In no case shall the supply value exceed the upper / lower voltage limit. To ensure
reliable operation of the unit, the power supply has to have a sufficient output capacitor and the supply
cables should have a low resistance, so that the chopper operation does not lead to an increased power
supply ripple directly at the unit. Power supply ripple due to the chopper operation should be kept at a
maximum of a few 100mV. This also is important in order to make the users application compatible to any
applicable EMC guidelines.
Therefore we recommend to
a) keep power supply cables as short as possible
b) use large diameter for power supply cables
c) if the distance to the power supply is large (i.e. more than 2 - 6m), use a robust 2200µF or larger
additional filtering capacitor located near to the motor driver unit.
5.3 Communication Interface
The communication between the host and the module takes place via its host interface. This can be either
RS232, RS485, IIC or CAN. Communication with the TMCM-111-57 module is done using TMCL commands. The
interface the module is equipped with is ready-to-use, so there are no external drivers or level shifters
necessary. The unused interface pins should be connected to ground to avoid failures.
Please see chapter 3.3.3 for the pin assignments of the interfaces.
To use the TMCL IDE with CAN interface either the Trinamic CANnes card or the Trinamic USB2X interface is
needed. To use the IIC interface with the TMCL IDE the Trinamic USB2X interface is needed.
5.4 Reference Switches
Two digital reference / stop switch inputs are provided (StopL= stop left and StopR = stop right). They are
used as an absolute position reference for homing and to set a hardware limit for the motion range. The
inputs have internal pullup resistors. Either opto-switches or mechanical switched with normally closed
contact can be used. The 5V output can be used as an supply for opto-switches.