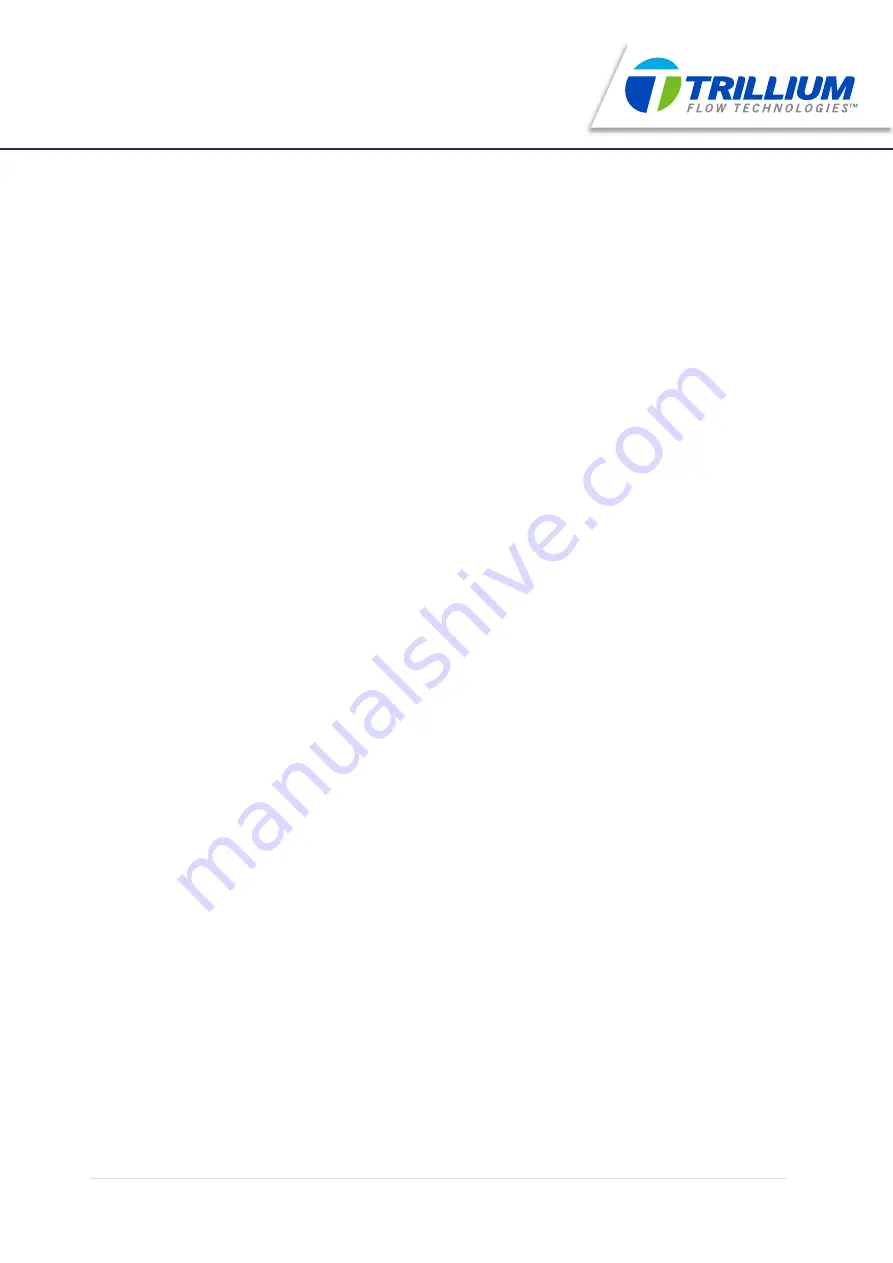
• MAIN VALVE PARTS INSPECTION & MAINTENANCE
8.1.1
GENERAL
RECOMMENDATIONS
We recommend to carefuly stock the disassembled valves per serial number not to mixup parts during
inspection and maintenance. Changes from one valve part to another can be invisible to the eye and may
compromit perfect valve operation during its whole life cycle.
The tools to use must be adequate in order to prevent the part damage. It is particularly true with soft good
materials, sliding surfaces and sealing ones.
8.1.2
PART
INSPECTION
• Main valve body (1)
Inspect the body for any cracks, erosion, pitting. Outlet flange gasket seating area shall be in proper
condition without any impact marks. If the body has such defects it shall be replaced.
The upper body gasket seating surface roughness shall be of about Ra 1.6µm (64 RMS). Scratches
can be removed with abrasive paper grade 1000 or higher.
• Main valve boltings (1)
Studs and nut shall be free of rust, and threads free of deformation and impact marks. If studs and
nuts are not in perfect shape the defected ones shall be replaced.
• Main valve cover (2)
Inspect the Cover for any cracks, erosion, pitting. If the cover has such defects it shall be replaced.
The lower cover gasket seating surface roughness shall be of about Ra 1.6µm (64 RMS). Scratches
can be removed with abrasive paper grade 1000 or higher.
Check the dome internal diameter and inlet chamfer where the piston slides. If surface is galled,
scratched, corroded or pitted the cover shall be replaced.
• Main valve guide (9)
The gasket seating surfaces (in green) roughness shall be of about Ra 1.6µm (64 RMS). Scratches
can be removed with abrasive paper grade 1000 or higher.
Check the internal diameter (in green) where the disc-holder slides. If surface is galled, scratched,
corroded or pitted the guide shall be replaced.
• Nozzle seat
• Inspect the nozzle seat. Any scratch or impact mark more than 0.5mm deep on the
seating surface shall be removed by lapping. The remachining of the nozzle seating
surface is recommended if there is any impact mark deeper than 0.5mm.
• Lap the nozzle seat as deemed necessary.
• Final roughness of the seating surface of the disc shall be Ra 0.4µm (16 RMS).
Planeity of the lapping machine shall have been checked.
•
Inspect nozzle seating surface after lapping / machining operations.
Touch check the roughness of lapped seating surfaces according to ISO 2632 (or
equivalent) test specimen.
Final roughness of the seating surface of the nozzle shall be Ra 0.4µm (16 RMS).
24
|
www.trilliumflow.com
78 SERIE SAFETY RELIEF VALVE
SARASIN-RSBD
™
Содержание SARASIN-RSBD 78 Series
Страница 1: ...78 SERIES Installation Operation Maintenance Manual...
Страница 32: ......
Страница 33: ......