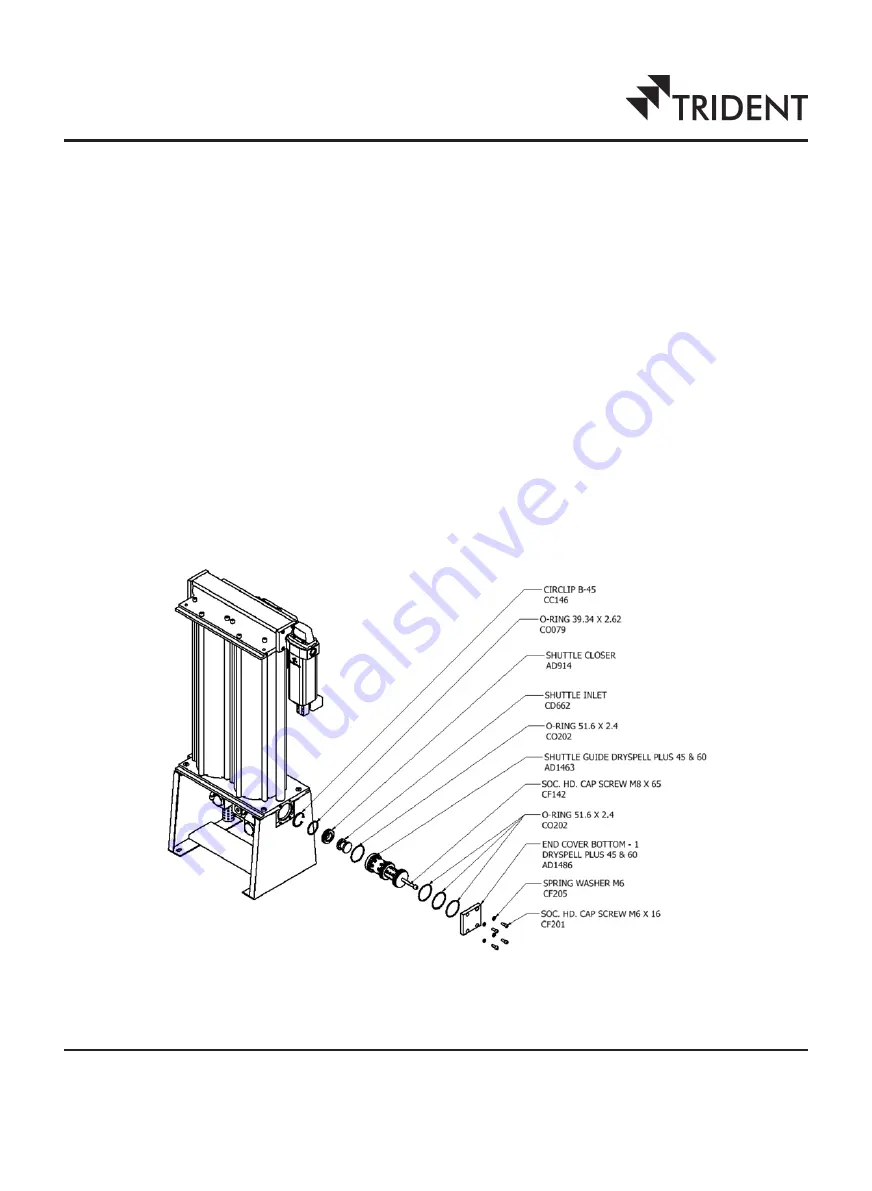
l
Remove the socket head cap screws
l
Remove the top chamber with the filter and controller
l
Remove the top compactor plates (two)
l
Remove the old desiccant bags
l
Replace the drying tower gaskets and the bottom diffuser assemblies with new ones
l
Fasten the towers in the bottom by tightening the screws
l
Filling the Desiccant bag assembly :
Dryspell Plus model 45:
Fill the desiccant bag assembly firstly with a bag of Activated Alumina AD1398 followed by a bag of mixed Activated alumina
and molecular sieves AD1624 as shown in the figure 19.
Dryspell Plus model 60:
Fill the desiccant bag assembly firstly with 2 bags of Activated Alumina AD1398, AD1622, lastly with a bag of Molecular
sieves AD1623 as shown in the figure 20
l
Reassemble the top compactor plates and the drying tower gaskets
l
Fix the top chamber
l
Fasten it by tightening the screws
8.5.3.2 Servicing the bottom shuttle
Figure 21. Exploded view of bottom shuttle-Dryspell Plus models 45 and 60
33
Содержание DRYSPELL PLUS 10
Страница 1: ...DRYSPELL PLUS Desiccant compressed air dryers Models 10 20 30 45 60 100 125 200 250 300 375 MANUAL ...
Страница 4: ......
Страница 38: ...31 DRYSPELL PLUS 60 EXPLODED VIEW Drw No PD241 ...
Страница 44: ...8 5 4 Dryspell Plus models 100 125 37 DRYSPELL PLUS 100 EXPLODED VIEW Drw No PD242 ...
Страница 45: ...INSTRUCTION MANUAL Dryspell Plus Reference Manual Version 38 DRYSPELL PLUS 125 EXPLODED VIEW Drw No PD243 ...
Страница 46: ...8 5 4 1 Changing the desiccant Figure 25 Changing desiccant Dryspell Plus model 100 39 ...
Страница 52: ...8 5 5 Dryspell Plus models 200 250 45 DRYSPELL PLUS 200 EXPLODED VIEW Drw No PD244 ...
Страница 53: ...DRYSPELL PLUS 250 EXPLODED VIEW Drw No PD245 INSTRUCTION MANUAL Dryspell Plus Reference Manual Version 46 ...
Страница 60: ...DRYSPELL PLUS 375 EXPLODED VIEW Drw No PD247 53 ...
Страница 70: ...INSTRUCTION MANUAL Dryspell Plus Reference Manual Version 64 Appendix Conversion tables ...