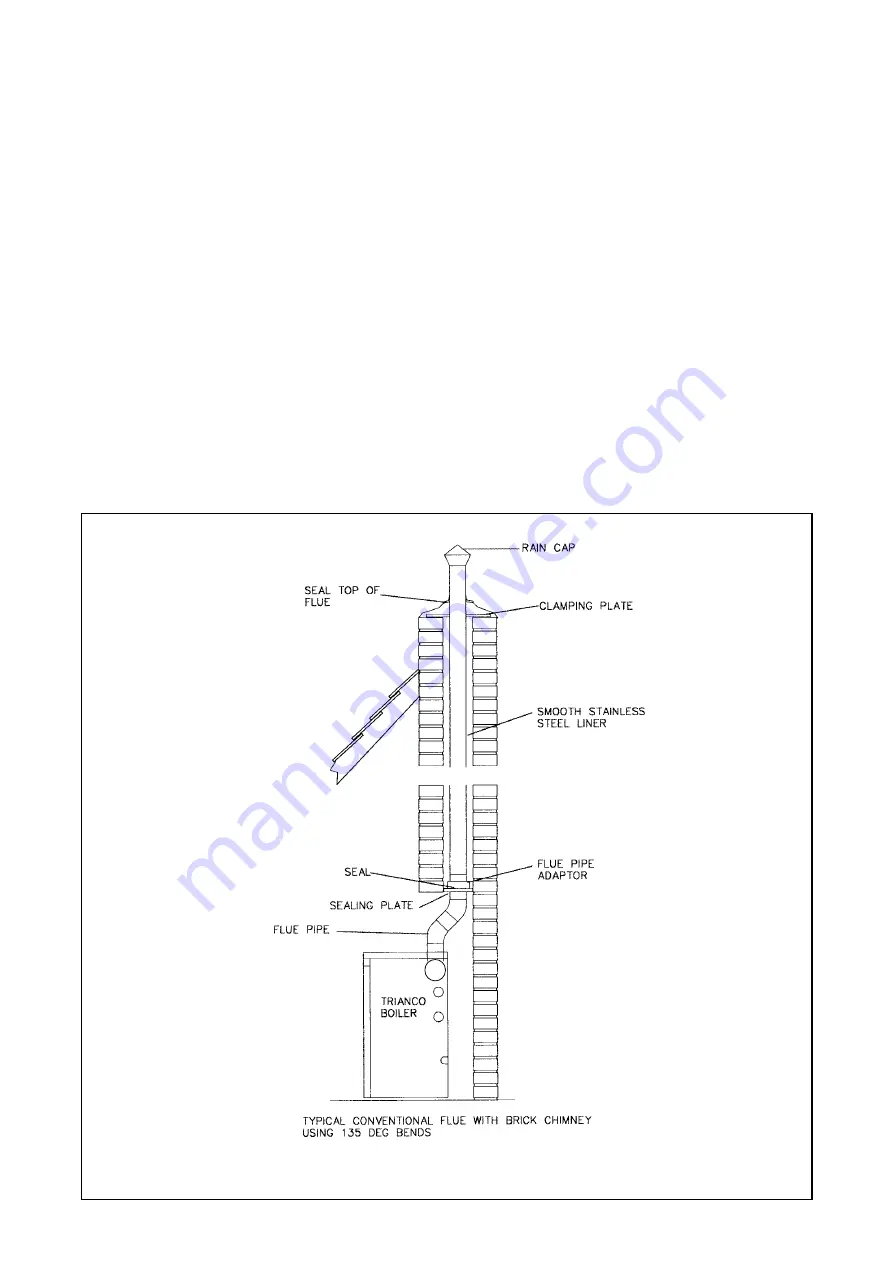
6. FLUE SYSTEMS
To evacuate the products of combustion safely and
thoroughly, the boiler must have an efficient flue system.
Under no circumstances should the boiler be installed
using an existing flue system.
All components used in the flue system should be suitable
for wet flues. The design and construction of the Trianco
balanced flue kits take these factors into account so the
following guidance notes are for conventional chimneys.
Reference should also be made to BS 5410 Part 1 if further
information is required on conventional chimneys.
Conventional chimney (Fig. 14)
Trianco condensing boilers operate at high efficiencies
with low flue gas temperatures. The flue system used on
this boiler must be suitable for low flue gas temperatures
and condensation.
1 The chimney should rise as vertically as possible and
terminate at a point not subject to down draughts or
wind effects.
2 The condensation produced in the flue system can be
allowed to run back in to the boiler. No separate drain
at the base of the flue system is required
3 Where an existing chimney is to be used it must be lined
with a stainless steel liner that is approved for use on
an oil fired condensing boiler. Note: Before fitting a flue
liner the chimney must be thoroughly cleaned free
from all traces of soot and scale.
4 If a rigid flue is to be fitted externally a twin wall flue
must be used. The flue must be constructed with a
stainless steel inner skin (suitable for condensation),
insulation and incorporate seals and be weather proofed.
5 The internal flue diameter must be 100 mm (4 in)
minimum.
6 The flue pipe between the boiler and the chimney must
be manufactured from 316 stainless steel or higher.
Aluminum or plastic must not be used on any part of the
flue system.
7 The in-built flue gas resistance of the Eurostar is such
that it allows the boiler to operate reliably over the wide
range of chimney draughts encountered from typical
domestic chimneys. Under normal draught conditions,
the flue should terminate with a standard cowl.
IMPORTANT
Ensure that all the joints on the flue system are sealed
and that no condense can escape.
15
FIG.14
Содержание EuroStar Premier 100/125 Condensing
Страница 10: ...FIG 5 WIRING DIAGRAM 7...
Страница 21: ...Fig 19 19 7 18...