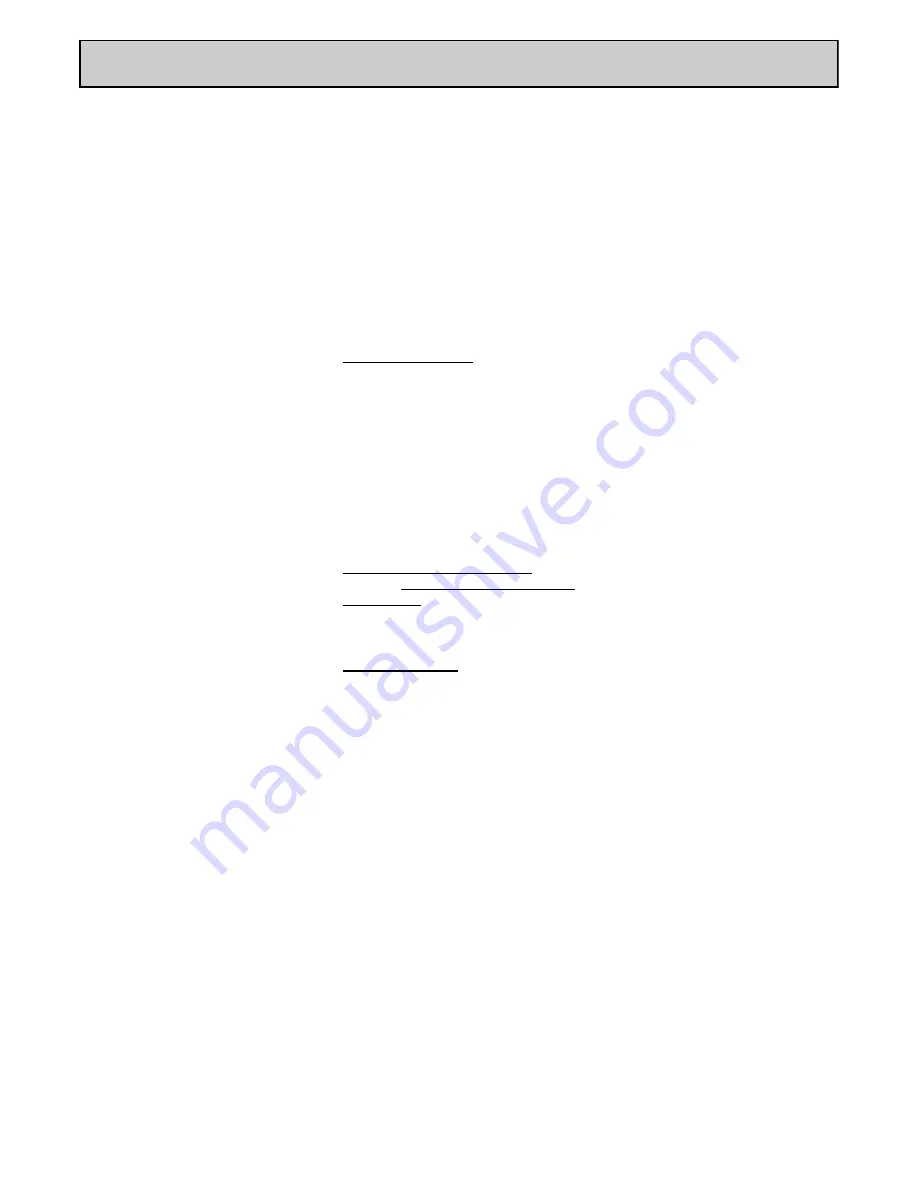
Before operating the tool ensure that
the tool is not near your chin or face.
Safe use of this tool requires a solid
stance and secure foothold; the
operator must adopt a firm and
stable position at all times.
On start up, the vibration reduction
component within the tool will cause
the machine to rise three to four
inches (100mm), to operate the tool
pull the lever towards the handle
grip.
Compactor Version
Let the tool do the work; allow a
period
of
time
to
become
accustomed
to
the
vibration
dampened compaction action. The
tool does not require any down force
to operate; excessive pressure will
prevent the tool from working
effectively and may reduce the
compaction rate.
The
optimum
speed
for
a
compaction pass is approximately
ten seconds per linear meter; it will
achieve optimum compaction after
four passes, using an average depth
of 150mm (6”) of un-compacted
MOT Type 1 granular fill.
Scabbler Version
Let the tool do the work; allow a
period
of
time
to
become
accustomed
to
the
vibration-
dampened action. The tool does not
require any down force to operate;
excessive pressure will prevent the
tool from working effectively.
Bush Hammer style headed pistons
are best suited to concrete reduction
and for laitance removal; these may
reduce the likelihood of damage to
the aggregate, ensuring that a
stronger bond is created with the
next layer.
Cruciform headed pistons are suited
to the reduction of concrete or where
a smoother finish is required; these
will reduce the aggregate as well as
the concrete surface.
To switch off, simply release the
throttle lever.
OPERATION / MAINTENANCE
Risk of Hand-Arm
Vibration Injury
These tools may cause Hand-arm
Vibration Syndrome injury if their use
is not adequately managed. We
advise you to carry out a risk
assessment and to implement
measures such as; limiting exposure
time [i.e. actual trigger time, not total
time at work], job rotation, ensuring
the tools are used correctly, ensuring
the tools are maintained according to
our recommendations, and ensuring
that the operators wear personal
protective
equipment
[PPE]
particularly gloves and clothing
to
keep them warm and dry. Employers
should consider setting up a
programme of health surveillance to
establish a benchmark for each
operator and to detect any early
symptoms of vibration injury.
We are not aware of any PPE that
provides protection against vibration
injury
by
attenuating
vibration
emissions.
See „
Specifications
‟ section for
vibration emission data.
Further advice is available from our
Technical Department.
Starting Work
Before use, screw the vibration
reducing side handle to the bracket
fitted on the main tube handle and
tighten by hand.
The side handle height can be
positioned for operator comfort; the
lower the side handle is positioned
down the tube the easier it will be to
manoeuvre the tool.
Prior to operating the tool check: -
That all fittings are secure, free from
air leaks and that air hoses are in
good condition.
That all parts of the tool are fully
screwed together and secure, if you
are in any doubt ask your supervisor
before using this equipment.
That the air pressure is correct for
this tool 6.2 bar (90 p.s.i.).
That a liberal amount of lubricant
has been put into the air inlet of the
tool. (See recommended lubricants)
Maintenance
Only a competent person, in a
suitably equipped workshop, must
carry out maintenance.
Disconnect the tool from the air
supply before carrying out any of
the following operations.
Dismantling
Clean all debris from the exterior of
the tool.
Loosen the 8mm caphead screw on
the side handle and slide the side
handle (10) up towards the handle
valve body (4). Hold the body
assembly (18) in a vice, using the
flats provided.
Check to see if the body and cowls
original mating identification dimples
are still visible, if not make a mark
opposite one another on the body
and the cowl to aid assembly.
With a 9mm punch, drive out the 2
securing pins on either side of the
cowl (9). Slide the cowl (8) and the
secondary spring (12) towards the
side handle (10). Unscrew the
locknut (16) by holding the handle
tube (11) in a vice, approximately six
inches (150mm) away from the lock
nut.
Using a cold chisel bend back the
tab washer (16A) from the flats of
the locknut (16).
Using a suitable spanner on the flats
of the locknut (16) unscrew from
handle tube (11). This may need a
sharp blow to break the bond.
Supporting the weight of the body,
unscrew the locknut and remove the
body assembly from the handle tube
(11).
Remove the tube from the vice. Next
hold the body in the vice using the
flats provided. Insert a 4mm steel
rod/bar into the hole on centre shaft,
located near the top of the spring.
Rotate the spring (15) on the shaft
so that it “screws” down the 4mm
rod/bar; rotate until a gap appears
between the spring (15) and thrust
ring (13).
Remove circlip and thrust ring. To
relieve the spring tension wind the
spring in the opposite direction until
the spring is at its free 'unloaded'
length. Withdraw the 4mm pin and
remove the spring (15), locknut (16)
and O' Ring cushion (17).
Содержание VL LRS55
Страница 1: ...VL LRS55 Scabbler VL Compactor Operation and Maintenance Manual www trelawnyspt co uk ...
Страница 6: ...EXPLODED VIEW ...
Страница 9: ...NOTES ...