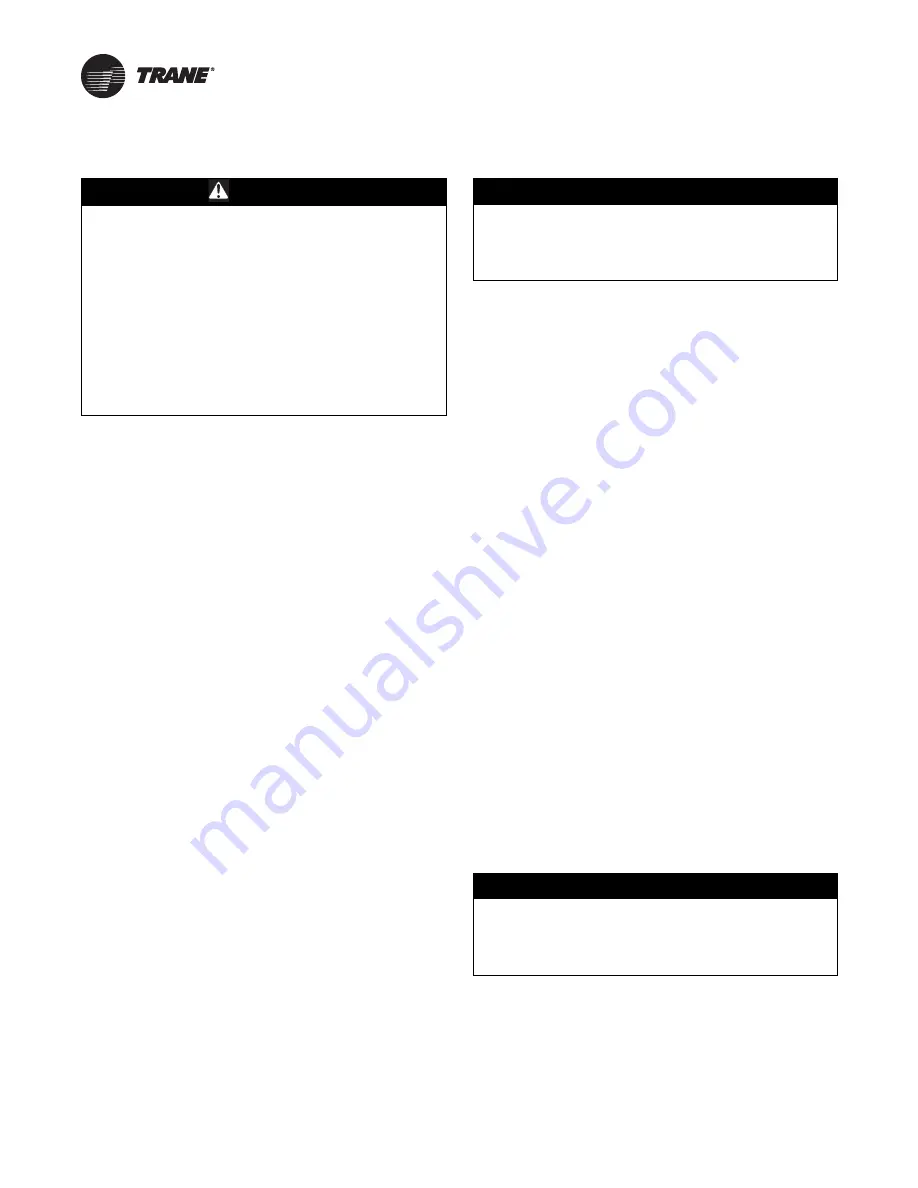
72
RTAF-SVX001K-EN
Maintenance
This section describes the basic chiller preventive
maintenance procedures, and recommends the intervals
at which these procedures should be performed. Use of a
periodic maintenance program is important to ensure the
best possible performance and efficiency from a
Sintesis™ chiller.
Use Operator Log in Log and Check Sheet chapter to
record an operating history for unit. The log serves as a
valuable diagnostic tool for service personnel. By
observing trends in operating conditions, an operator can
anticipate and prevent problem situations.
If unit does not operate properly during inspections, see
Diagnostics chapter.
Recommended Maintenance
Perform all maintenance procedures and inspections at
the recommended intervals. This will increase the life of
the chiller and minimize the possibility of costly failures.
Weekly
•
At AdaptiView™ TD7 or Tracer™ TU service tool, check
pressure for evaporator, condenser and intermediate
oil.
•
Observe liquid line sight glass on EXV. If liquid line
sight glass has bubbles measure the subcooling
entering the EXV. Subcooling should always be
greater than 10°F.
Important:
A clear sight glass alone does not mean that
the system is properly charged. Also check
the rest of the system operating conditions.
•
Inspect the entire system for unusual operation.
•
Inspect the condenser coils for dirt and debris. If the
coils are dirty, see
“Microchannel Condenser Coils,”
.
•
Ensure exterior of panel enclosures (including remote
VFD, if installed) are clear of any dust or debris.
Important:
Panel cooling air lets must be regularly
inspected and kept clean and free of debris.
Failure to do so can cause reduced cooling
to drives, resulting in unit trips on drive
over-temperature.
Monthly
•
Perform all weekly maintenance procedures.
•
Record the system subcooling.
•
Record the system superheat.
•
Make any repairs necessary.
Annual
•
Perform all weekly and monthly procedures
•
Check the oil level while the unit is off. See
•
Routine changing of the oil is not required. Make an
oil analysis to determine the condition of the oil.
•
Have Trane or another qualified laboratory perform a
compressor oil analysis to determine system moisture
content and acid level.
•
Contact a qualified service organization to leak-test the
chiller, to check operating and safety controls, and to
inspect electrical components for deficiencies
•
Clean and repaint any areas that show signs of
corrosion.
•
Clean the condenser coils. See
.
•
Clean the air filters in the bottom inlet hoods that
extend from the back of the electrical panel.
•
Check and tighten all electrical connections as
necessary.
WARNING
Hazardous Voltage w/Capacitors!
Failure to disconnect power and discharge capacitors
before servicing could result in death or serious injury.
Disconnect all electric power, including remote
disconnects and discharge all motor start/run
capacitors before servicing. Follow proper lockout/
tagout procedures to ensure the power cannot be
inadvertently energized. For variable frequency drives or
other energy storing components provided by Trane or
others, refer to the appropriate manufacturer’s literature
for allowable waiting periods for discharge of
capacitors. Verify with a CAT III or IV voltmeter rated per
NFPA 70E that all capacitors have discharged.
NOTICE:
Coil Damage!
Use of detergents could cause damage to coils.
Do not use detergents to clean coils. Use clean water
only.
NOTICE:
Coil Damage!
Use of detergents could cause damage to coils.
Do not use detergents to clean coils. Use clean water
only.