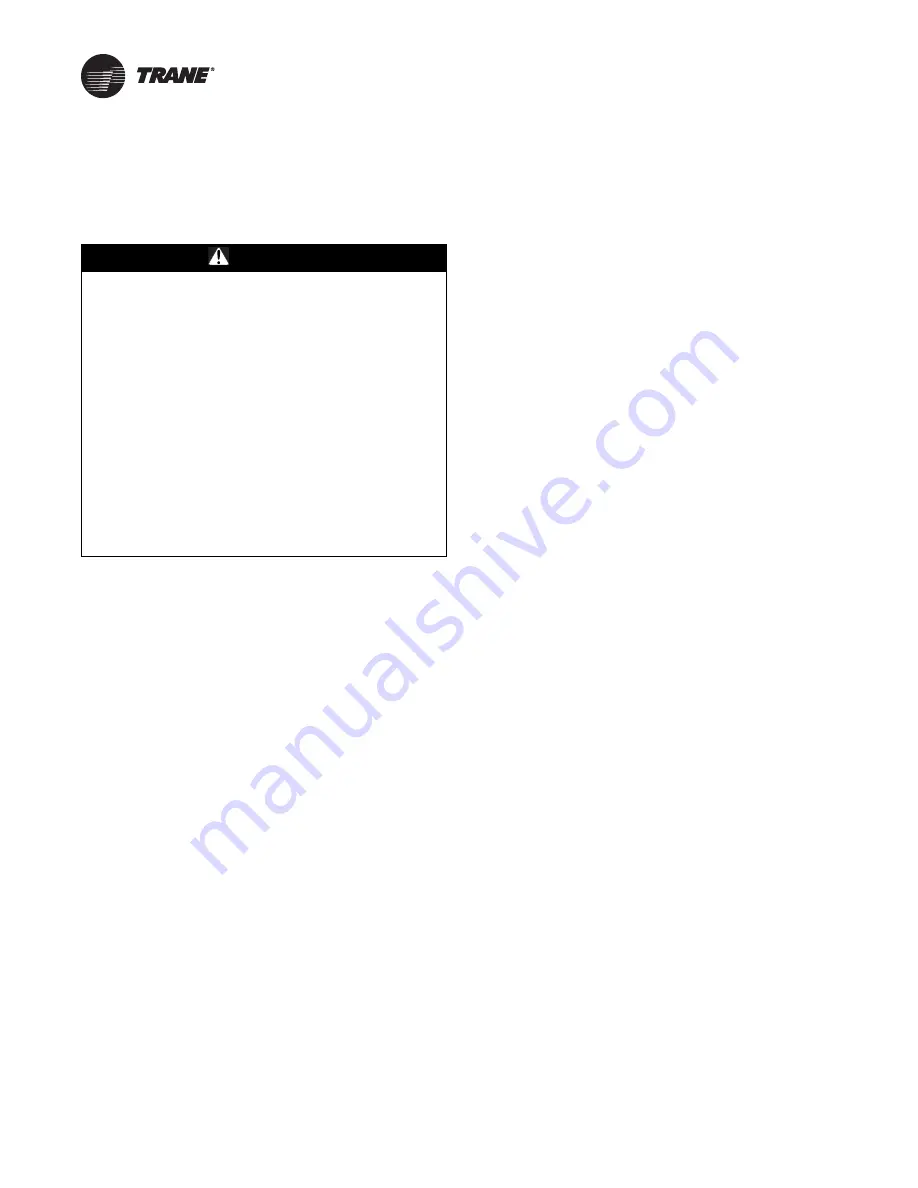
PART-SVN234B-EN
31
Troubleshooting
Important:
Check the unit
Installation, Operation, and
Maintenance
manual for additional
information regarding diagnosis and
causes.
WARNING
Hazardous Service Procedures!
Failure to follow all precautions in this manual and on
the tags, stickers, and labels could result in death or
serious injury.
Technicians, in order to protect themselves from
potential electrical, mechanical, and chemical hazards,
MUST follow precautions in this manual and on the
tags, stickers, and labels, as well as the following
instructions: Unless specified otherwise, disconnect all
electrical power including remote disconnect and
discharge all energy storing devices such as capacitors
before servicing. Follow proper lockout/tagout
procedures to ensure the power can not be
inadvertently energized. When necessary to work with
live electrical components, have a qualified licensed
electrician or other individual who has been trained in
handling live electrical components perform these
tasks.
Compressor will not start
•
Refer to the unit
Installation, Operation, and
Maintenance
manual for possible diagnostics codes
and corrective action.
•
Verify:
– Compressor voltage is correct.
–
182–361 nominal capacity compressors
—Motor
protection module is the correct voltage.
– All safety switches are closed.
– All the contacts on the contactor are pulled in.
–
090–181 nominal capacity compressors
—The
internal motor overloads may be open. Disconnect
power to the unit and disconnect the wires from the
compressor terminals. With an ohm meter, check to
ensure that there is resistance between T1-T2 and
T3.
Compressor will not build up pressure
•
090–181 nominal capacity compressor
is wired
incorrectly
—It will be noisy and draw 1/2 the expected
amps. Shut the compressor off immediately. Running
in this condition for more than 5 seconds may damage
the compressor.
•
182–361 nominal capacity compressor is wired
incorrectly
.
•
Check to ensure that any bypass valves in the system
are not open.
•
Four-way reversing valve may be stuck and not
switched properly bypassing from the high side to the
low side of the system; this situation is indicated by an
extremely warm suction inlet to the compressor.
•
360–361 nominal capacity compressors contain an
internal pressure relief that may have opened.
It may
take two to three hours to reset. The oil sump will be
very warm and the compressor will be tripped out on
the motor protection module. This is caused by a very
high 625–715 psid difference between the high side
and low side of the system. This could occur with either
a blocked high side or low side.
Abnormal running noise
•
Compressor is running backwards—Immediately shut
off the compressor and check wiring and proper
phasing.
•
Excessive floodback—The superheat should be a
minimum of 16°F at full load and oil sump temperature
should be at least 20°F above the saturated suction
temperature. Measure the sump temperature at the
bottom center of the compressor. Chillers with
electronic expansion valves may operate with lower
superheats; check the unit
Installation, Operation, and
Maintenance
manual for proper operating superheats.
•
Compressor is full of liquid on startup—The crankcase
heater either was not energized for a minimum of
eight hours, or it is defective.
•
Mechanical damage to the compressor has occurred—
Check compressor amperage. It may also trip the
compressor motor protection module or other unit
electrical protection devices such as circuit breakers.
High-pressure control opens
•
Check the unit
Installation, Operation, and
Maintenance
manual for possible diagnostics codes
and corrective action.
•
Also check for:
– Defective condenser fan motors or controls.
– Dirty air-cooled or water-cooled condensers.
– Restricted air flow.
– Insufficient water flow.
– System overcharged with refrigerant. Check
superheat and system subcooling.
– Non-condensables in the system.
Low-pressure control opens
•
Check the unit
Installation, Operation, and
Maintenance
manual for possible diagnostics codes
and corrective action.
•
Also check for:
– Defective evaporator fan motors, belts, or controls.
– Defective TXV valve.
– Plugged liquid line filter.