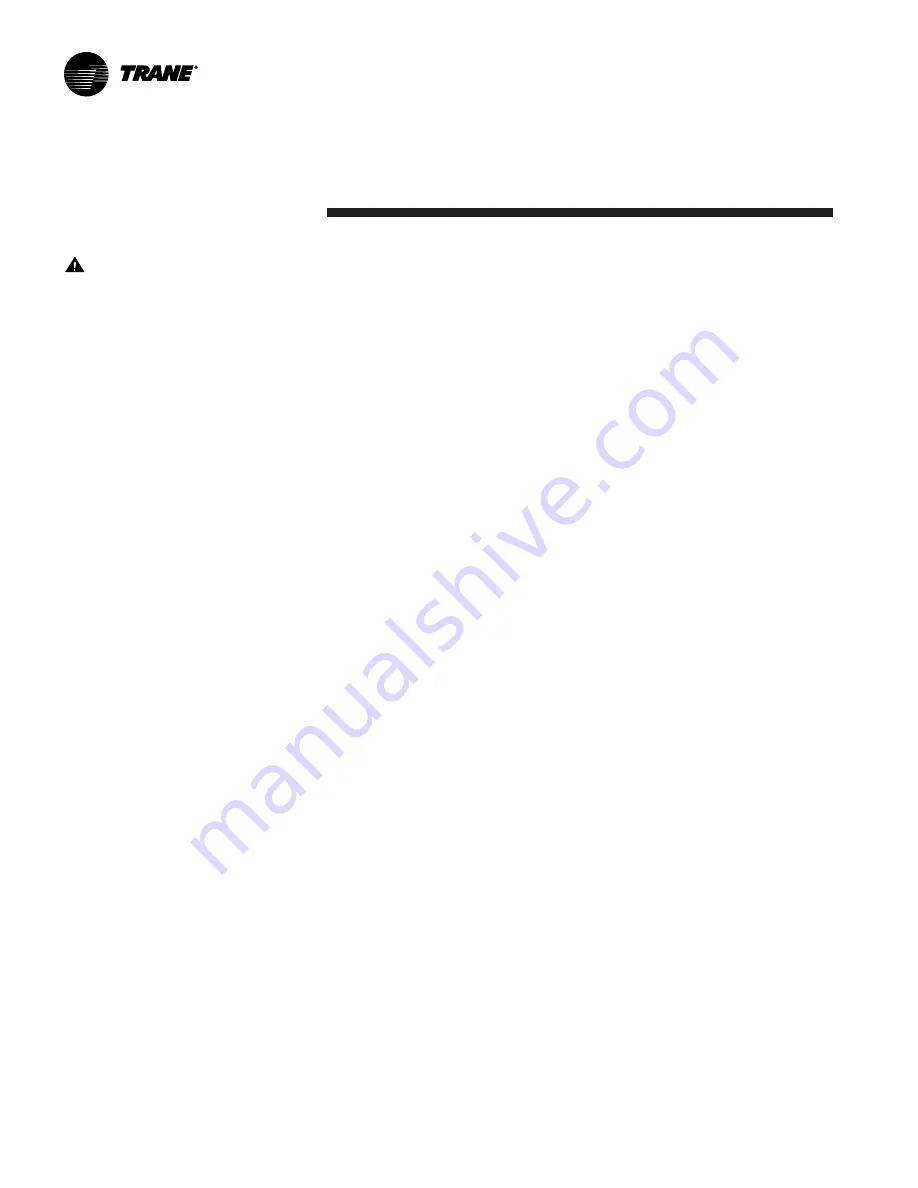
PTEC-M-1A
46
Disassembly
Procedures
Reversing Valve
1. Remove the chassis from the wall
sleeve.
2. After capturing the refrigerant
from the system, debraze the
outdoor coil, indoor coil, and
compressor tubing from the
reversing valve. Remove reversing
valve.
Drain Valve
1. Remove the chassis from the wall
sleeve.
2. Remove the mounting screw and
remove the drain valve.
WARNING!
To avoid possible electrical shock,
personal injury or death, disconnect
the power before servicing.
Vent Door
1. Remove Chassis from wall sleeve.
2. Remove P clamp securing vent
door control cable to center
partition and disconnect cable
from vent door.
3. Remove vent door by opening
door and pulling hinge tabs out of
slots in center partition.
4. Remove the door by pulling hinge
tabs out away from the center
partition.
Содержание PTEC-070
Страница 22: ...PTEC M 1A 22 Refrigeration System PTEC Refrigeration System...
Страница 54: ...PTEC M 1A 54 Schematic Diagrams PTEC and PTHC Condensate Pump One Stage Heat...
Страница 55: ...55 PTEC M 1A Schematic Diagrams PTEC and PTHC Condensate Pump Two Stage Heat...
Страница 56: ...PTEC M 1A 56 Schematic Diagrams PTEC and PTHC Power Vent One Stage Heat...
Страница 57: ...57 PTEC M 1A Schematic Diagrams PTEC and PTHC Power Vent Two Stage Heat...
Страница 58: ...PTEC M 1A 58 PTEC and PTHC Power Door One Stage Heat Schematic Diagrams...
Страница 59: ...59 PTEC M 1A Schematic Diagrams PTEC and PTHC Power Door Two Stage Heat...
Страница 60: ...PTEC M 1A 60 Schematic Diagrams PTEC and PTHC Condensate Pump with Power Vent One Stage Heat...
Страница 61: ...61 PTEC M 1A Schematic Diagrams PTEC and PTHC Condensate Pump with Power Vent Two Stage Heat...
Страница 62: ...PTEC M 1A 62 Schematic Diagrams Hydronic...
Страница 63: ......