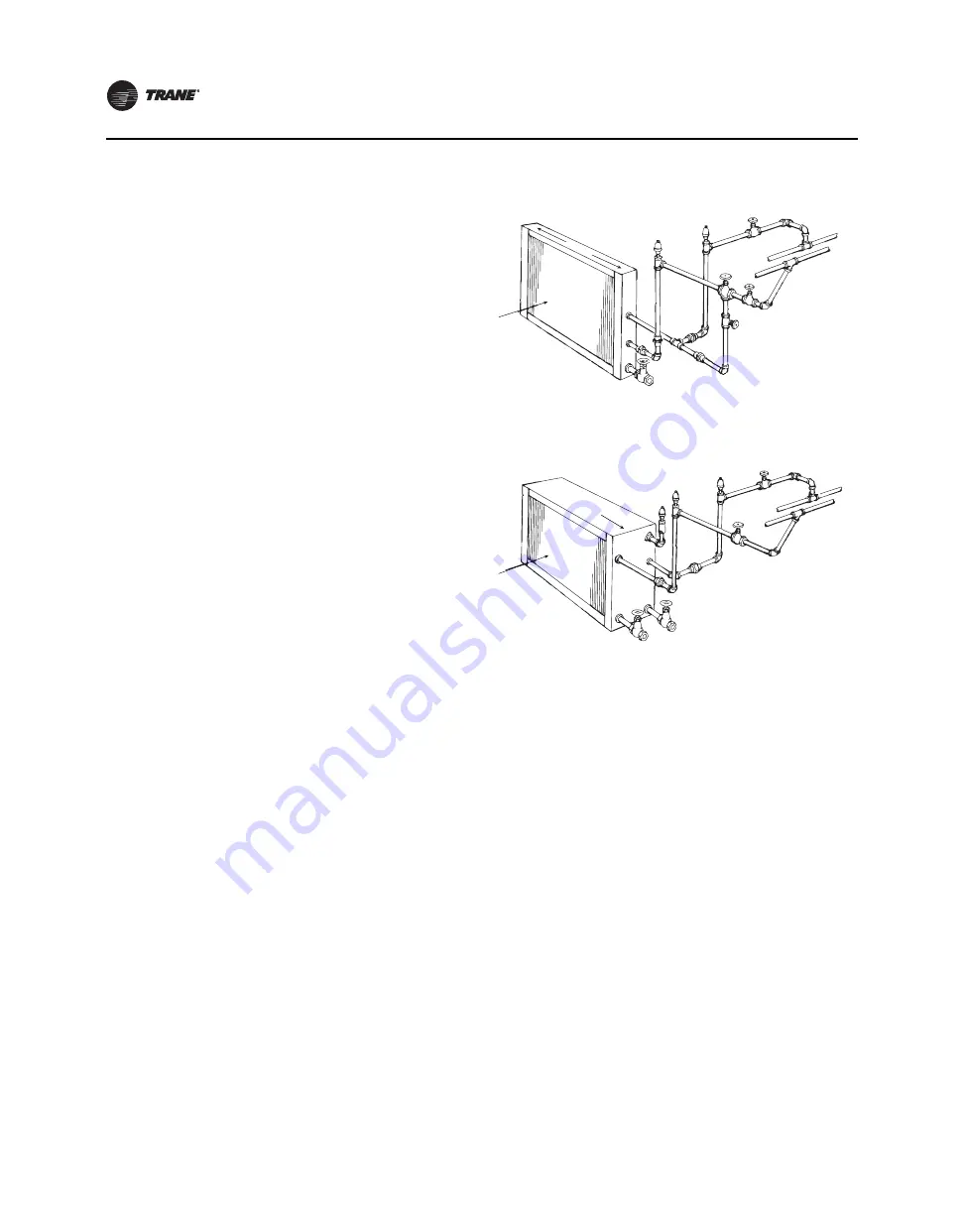
Piping and Connections
40
CLCH-SVX010A-EN
Water Coil Piping
Figure 49
and
Figure 50
illustrate typical water coil piping
configurations.
Water coils are self-venting only if the water velocity
exceeds 1.5 feet per second (fps) in the coil tubes. See the
unit submittals for coil water velocity. If the water velocity
is below these minimums, vent the coil by one of the
following methods:
1.
Install an air vent in the top pipe plug tapping of the
return header.
2. When the return line rises above the top of the coil,
vent from the top of the return header horizontally to
the return piping.
Figure 49.
Typical piping for one-row water coil
Figure 50.
Typical piping for 2 - 8-row water coils
GV
GV
GV
AV
AV
Water supply
main
Water
return main
Drain
Lev
el
Airflow
AV
AV
AV
GV
Water supply
main
Wa
ter
return main
Drain
Pitch down
Airflo
w