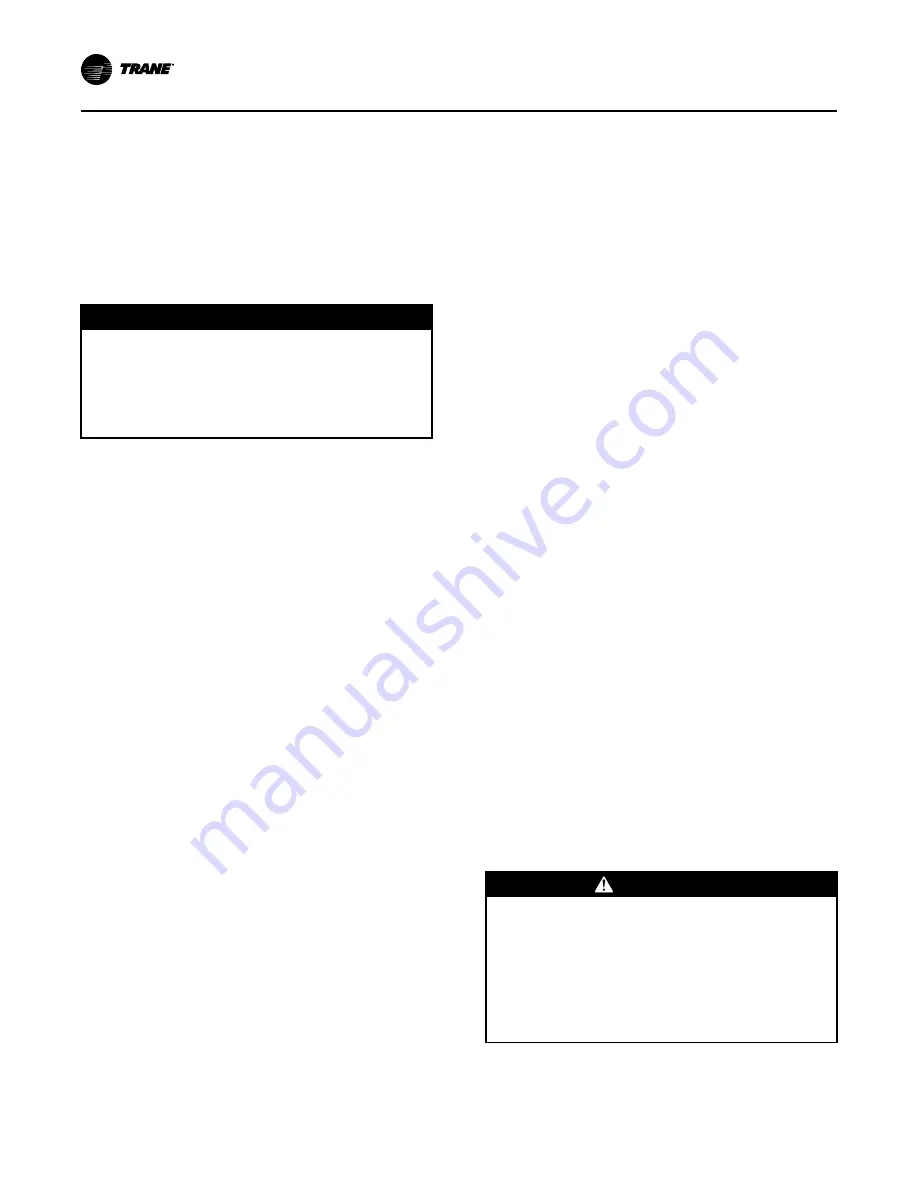
60
ARTC-SVX005B-EN
9. For R134A refrigerant, low pressure refrigeration
gauge should read 35 to 50 psi and high pressure
refrigeration gauge should read 100 to 120 psi.
IIm
mp
po
orrtta
an
ntt:: For R134A, suction pressures below 25 psi
can cause extensive damage to a
compressor.
10. Check the refrigeration liquid line sight glass for
persistent bubbles (“flashing”) in conjunction with
a half-full glass may represent a low refrigerant
charge.
N
NO
OT
TIIC
CE
E
E
Eq
qu
uiip
pm
me
en
ntt D
Da
am
ma
ag
ge
e!!
F
Fa
aiillu
urre
e tto
o rre
em
mo
ov
ve
e m
mo
oiissttu
urre
e ffrro
om
m ssy
ysstte
em
m cco
ou
ulld
d
cca
au
usse
e cco
orrrro
ossiio
on
n w
wiitth
hiin
n tth
he
e cch
hiilllle
err//h
he
ea
atte
err
cco
om
mp
po
on
ne
en
nttss,, a
an
nd
d d
de
eg
grra
ad
de
e p
pe
errffo
orrm
ma
an
ncce
e..
P
Pe
errffo
orrm
m v
va
accu
uu
um
m e
ev
va
accu
ua
attiio
on
n o
off ssy
ysstte
em
m tto
o rre
em
mo
ov
ve
e
m
mo
oiissttu
urre
e..
N
No
otte
e:: Bubbles in the sight glass do not necessarily
indicate loss or lack of refrigerant charge.
Bubbles (commonly know as ‘flashing’) will
occur until the expansion valve settles out the
refrigerant flow. If the refrigeration pressures are
in the normal range, the unit is most likely
adequately charged. ‘Flashing’ could also
indicate excessive superheat adjustment of the
thermal expansion valve.
Quarterly
The quarterly maintenance inspection is a
comprehensive event that examines all aspects of the
chiller to identify early problems before they can
damage a chiller and require major repair or
refurbishment:
1. Inspect refrigerant pressures and temperature set
points.
2. Inspect chiller/heater superheat and sub-cooling.
System superheat should be 10 °F to 12 °F (5 °C to 6
°C). System sub-cooling should be 10+ °F (5 °C)
depending on the ambient conditions.
3. Inspect the approach evaporative - entering
evaporator water/glycol mixture temperature and
leaving evaporator water/glycol mixture
temperature as well as the condenser approach.
4. Inspect strainers.
5. Collect chilled water/glycol mixture sample for
professional analysis. Check for cleanliness. Drain
and refill with clean solution if excessive sludge or
dirt is present. Flush the chiller prior to refilling.
6. Inspect water/glycol mixture levels. Add glycol as
required.
7. If equipped, inspect crankcase heaters for proper
operation.
8. Inspect the water piping for signs of leaks at joints
and fittings.
9. Inspect refrigerant piping circuit for signs of oil or
refrigerant leakage. Conduct “sniffer test” to find
refrigerant leaks. Inspect all pressure switch
bellows.
10. Tighten all refrigeration piping connections (e.g.
rotalocks stems and packing nuts, Schrader valves,
and ball valves).
11. Install a manifold and gauge set to observe chiller/
heater’s refrigeration operating pressures.
a. Verify that the pressure controls (low pressure
and high pressure switches) are “cutting in” and
“cutting out” at the appropriate pressures.
b. Verify refrigerant charge by recording the
superheat and sub-cooling temperatures and
visually inspect the sight glass..
c. Observe head pressure for signs of improper
condensing from clogged strainers, or a
modulating expansion valve issue.
12. Check compressor motor amperage draws and
voltage supplies and maintain a record of those
values. Verify that they are within the name plate
rating. Also, check for voltage imbalance. The
chiller/heater’s phase monitor will open if the
voltage imbalance exceeds 4%.
13. Check for excessive wear or burned contacts on
motor starters. Replace contacts, if in doubt.
Annually
The annual chiller maintenance inspection is critical to
the long-term performance of the chiller/heater.
Whether a chiller has a service life of 15 years or 30
years is almost entirely dependent upon how
consistently and how diligently the annual
maintenance inspection and tasks are performed. The
annual event is a comprehensive inspection that
examines all aspect of the chiller/heater to identify and
repair small problems before they can become major
issues that damage a chiller and require significant
repair or refurbishment.
1. Inspect all electrical connections for damage and
ensure terminals are tight. Inspect all contactors for
pitting and corrosion and replace as necessary.
W
WA
AR
RN
NIIN
NG
G
H
Ha
azza
arrd
do
ou
uss V
Vo
olltta
ag
ge
e!!
F
Fa
aiillu
urre
e tto
o d
diisscco
on
nn
ne
ecctt p
po
ow
we
err b
be
effo
orre
e sse
errv
viicciin
ng
g cco
ou
ulld
d
rre
essu
ulltt iin
n d
de
ea
atth
h o
orr sse
erriio
ou
uss iin
njju
urry
y..
D
Diisscco
on
nn
ne
ecctt a
allll e
elle
eccttrriicc p
po
ow
we
err,, iin
nccllu
ud
diin
ng
g rre
em
mo
otte
e
d
diisscco
on
nn
ne
eccttss b
be
effo
orre
e sse
errv
viicciin
ng
g.. F
Fo
ollllo
ow
w p
prro
op
pe
err
llo
occkko
ou
utt//tta
ag
go
ou
utt p
prro
occe
ed
du
urre
ess tto
o e
en
nssu
urre
e tth
he
e p
po
ow
we
err
cca
an
n n
no
ott b
be
e iin
na
ad
dv
ve
errtte
en
nttlly
y e
en
ne
errg
giizze
ed
d.. V
Ve
erriiffy
y tth
ha
att n
no
o
p
po
ow
we
err iiss p
prre
esse
en
ntt w
wiitth
h a
a v
vo
ollttm
me
ette
err..
2. Inspect fuses to ensure they are secure, of correct
amperage ratng, undamaged and functioning.
Содержание Arctic PolyTherm TM Series
Страница 82: ...82 ARTC SVX005B EN N No ot te es s ...
Страница 83: ...ARTC SVX005B EN 83 N No ot te es s ...