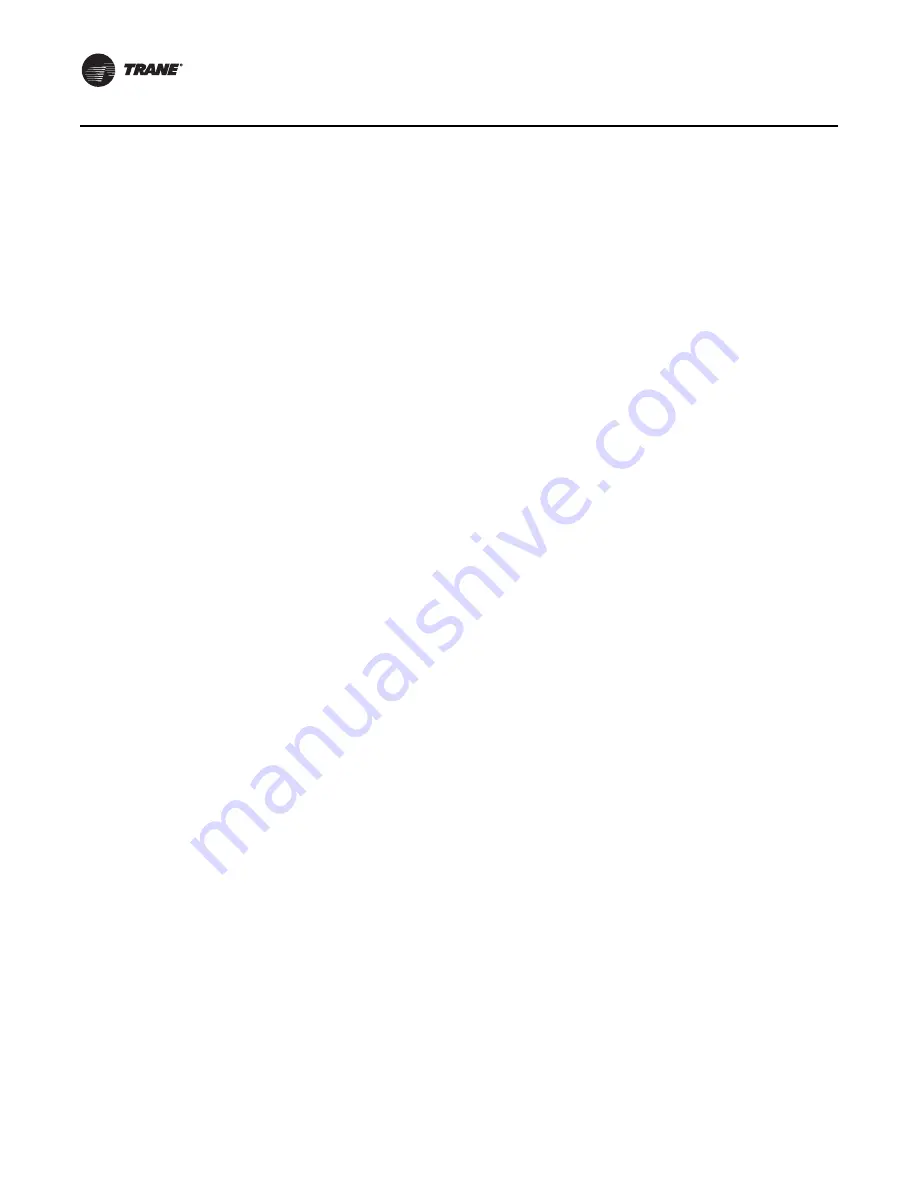
20
MS-SVN052E-EN
System Operation
Tf sensor is required for:
–
Protection against module temperature (high temperature)
A pressure transducer (PT) is required for:
–
Operating speed control
–
Outdoor electronic expansion valve (heat pump only)
–
High pressure protection (heating mode heat pump only)
–
Low pressure protection (cooling mode)
Defrost Description (Heat Pump Only)
Defrost control (when ordered) measures coil temperature with the use of a sensor located on the
heat pump coil. In order to measure outdoor ambient temperature, a second sensor is located on
the outside of the outdoor coil.
Defrost cycle starts with the reading of various parameters, i.e., outdoor unit coil temperature (T3
temperature sensor), outdoor environment temperature (T4 temperature sensor), cummulative
time of operation, coil temperature and high pressure (when high pressure is found to be lower
than a specific value).
Defrost cycle starts under one of 3 conditions as follows:
1.
When temperature differential (Delta T) between outdoor temperature (T4) and coil
temperature (T3) reaches a duration of 5 minutes, that is:
•
T4
≥
39ºF, Delta T = 18ºF
•
T4
≥
30ºF, Delta T = 16ºF
•
T4
≥
19ºF, Delta T = 14ºF
•
When T4
˂
19ºF, T3
˂
9ºF
2. When minimum time of operation (MRT) based on outdoor temperature is for example:
•
MRT - 4 hour duration when: T4
˂
23ºF
•
MRT - 2 hour duration when: 23ºF
≤
T4
˂
42ºF
3. When saturation temperature descends below 82ºF during a period of 20 minutes.
Defrost cycle ends under the following conditions:
1.
When outdoor coil temperature (T3) reaches 64ºF during a period of 1 minute or when defrost
period exceeds 8 minutes.
2. The adjustment of SW5 switch offers various defrost cycle options depending upon
geographical conditions and/or outdoor area conditions.
Содержание 4TXK6524D1000AL
Страница 25: ...MS SVN052E EN 25 System Operation ...
Страница 26: ...26 MS SVN052E EN System Operation ...
Страница 30: ...30 MS SVN052E EN Troubleshooting Troubleshooting Table 5 Troubleshooting ...
Страница 31: ...MS SVN052E EN 31 Troubleshooting Table 6 Fault Codes ...
Страница 33: ...MS SVN052E EN 33 Troubleshooting For model 24 36k ...
Страница 34: ...34 MS SVN052E EN Troubleshooting For model 48 60k and board Board ...
Страница 35: ...MS SVN052E EN 35 Troubleshooting ...