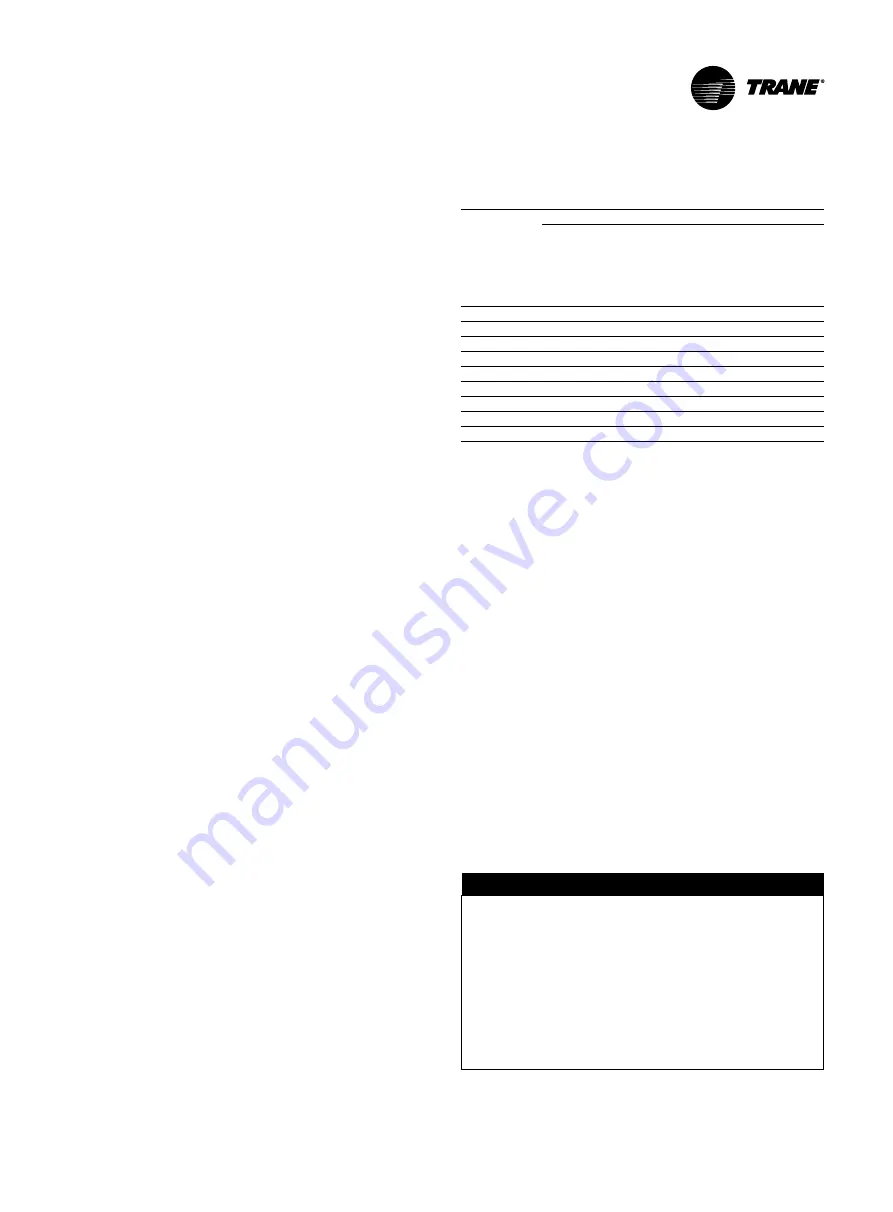
Insulation
Unit Insulation Requirements
Factory-installed insulation is available as an option for
all units.
In those instances where the chiller is not factory-insulat-
ed, install insulation over the areas outlined and high-
lighted with dashed lines. It may also be necessary to
insulate the compressor suction cover and motor barrel
if the unit is installed in an area subjected to high humid-
ities.
Insulate all 1/4” (6.4 mm) eductor lines, one from the
suction cover and one from the evaporator to prevent
sweating.
The quantities of insulation required based on unit size
and insulation thickness are listed in
. Insulation
thickness is determined at normal design conditions
which are:
• • standard comfort-cooling leaving chilled water tem
-
perature
•
85°F Dry bulb ambient temperature
•
75% Relative humidity
Note:
If the unit is not factory insulated: install insula-
tion around the evaporator bulbwells and ensure
that the bulbwells and connections for the water
box drains and vents are still accessible after
insulation is applied. The sensor modules (LLIDs)
and interconnecting four
wire cable (IPC Buss) must
be raised up above the field-installed insulation. Secure
the IPC
Buss to the insulation top/outer surface after
insulation is completed. Do not insulate over the wiring
or sensor devices.
Important:
Do not insulate the motor housing, unit
wiring, or sensor modules.
Table 7. Evaporator insulation requirements
EVSZ
(Note 1)
Standard Unit
Free Cooling
3/4”
(19 mm)
Insulation
(Note 1)
(Square
Feet)
3/8”
(9.5 mm)
Insulation
(Note 2)
(Square
Feet)
3/4”
(19 mm)
Insulation
(Note 1)
(Square
Feet)
3/8”
(9.5 mm)
Insulation
(Note 2)
(Square
Feet)
050 Short
385
63
398
72
050 Long
420
63
436
72
080 Short
505
84
515
97
080 Long
553
84
566
97
142 Medium
555
98
555
133
142 Long
578
98
578
133
142 Extended
603
104
629
133
210 Long
700
98
710
133
250 Extended
770
97
780
133
Notes:
1.
3/4” (19 mm) sheet insulation is installed on the evaporator, evapora-
tor water boxes, compressor motor, suction elbow and suction cover.
2.
3/8” (9.5 mm) sheet insulation is installed on all economizers. All liq-
uid lines and other pipes require the use of 1/2” (13 mm) pipe insulation
or 3/8” (9.5 mm) sheet insulation. Copper oil eductor tube lines require
pipe insulation.
3.
Refrigerant Pump equipped units are NOT insulated on the motor or
refrigerant drain lines.
Insulation Thickness Require-
ments
Factory applied insulation. All low temperature surfac-
es are covered with 3/4” (19 mm) Armaflex II or equal
(thermal conductivity = 0.28 BTU/hr-ft sq.) (1.59 W/m2-
K), including the evaporator, water boxes and suction
elbow. The economizer and motor cooling lines are
insulated with 3/8” (10 mm) and 1/2” (13 mm) insulation
respectively.
Insulation is Armaflex or equivalent closed cell elasto-
meric insulation, to prevent the formation of condensa-
tion up to a dew point rating of 74°F K = 0.25. Chillers
in high humidity areas or ice storage, low leaving water
temperature (less than 36-degree chilled water tempera-
ture/glycol) units may require double thickness to pre-
vent formation of condensation.
D
NOTICE
Insulation Damage!
To prevent damage to factory installed insulation:
- Do not allow the insulation to be exposed to exces-
sive sunlight. Store indoors or cover with canvas to
prevent exposure.
- Do not use thinners and solvents or other types of
paint. Use only water base latex. Failure to follow
these recommendations could result in insulation
damage.
RELEASED 10/Mar/2020 06:59:20 GMT