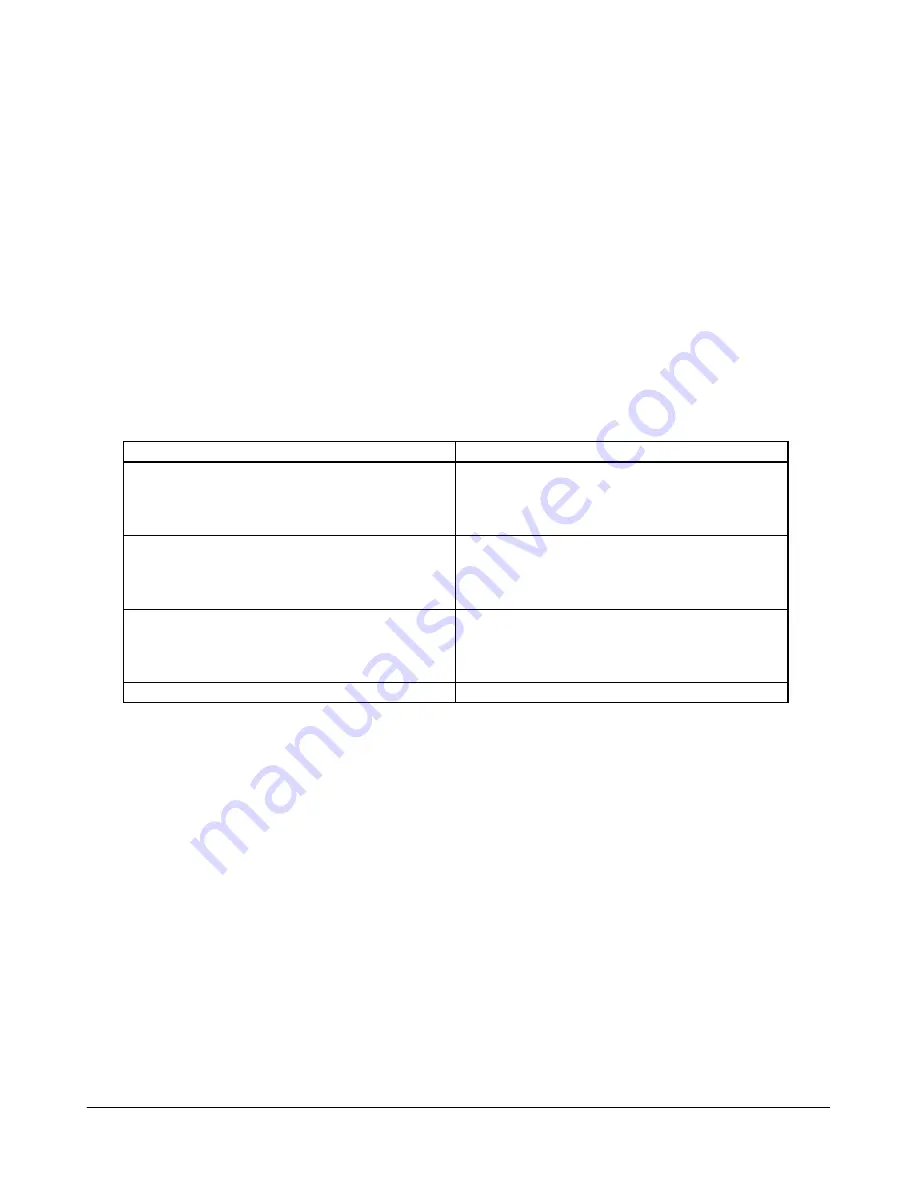
56
TRAK Machine Tools
Southwestern Industries, Inc.
ProtoTRAK SMX, K2, K3 & K4 & Retrofit Safety, Installation, Maintenance, Service and Parts List Manual
Defective or scarred gibs must be replaced. Shimming of gibs may not yield acceptable results.
It is good machining practice to avoid the use of shop air to clean the chips off a machine. This risks blowing chips into
the sliding way surfaces and compromising the performance of the machine.
Gibs that are not adjusted correctly will affect the performance of the machine. It will lead to positioning and
repeatability problems. The gibs should be adjusted at least twice a year.
See
Gib Adjustments Section 5.2.1.
4.1.3 Lubrication
Lubrication is one of the single, most important maintenance issues and plays a key role in assuring the performance
and durability of the Knee mill. At the beginning of each day manually supply oil to the way surfaces.
Lack of lubrication can lead to a variety of problems with your machine motion due to increased friction in the sliding
ways. This increased friction may lead to part inaccuracies and decreased life expectancies of your ball screws and way
surfaces.
4.1.4 Machining Set-Up
The machining set-up itself is always something that can greatly influence the performance of the your mill. The
following are some things to keep in mind.
Problems With
Can Contribute To:
Feed and Speeds (spindle rpm)
See below
Poor finish
Machine chatter
Excessive speeds and feeds can break cutting
tools or wear tools prematurely.
Tooling
Using the wrong cutter for an application
Entering the wrong size diameter and
programming with tool compensation.
Poor finish
Parts incorrect size
Cutting too deep
Part dimensions incorrect
Driving and cutting forces cause deflections,
since no material is totally rigid
Machine chatter
No coolant
Poor finish, decrease the life of the cutter
4.1.4.1 Spindle Speeds
Spindle speeds are influenced by a number of variables:
Material
Rigidity of the Machine Setup
Coolant
Cutter type, material and diameter
Cutting Depth
As a general rule:
Lower spindle speeds are used to machine hard or tough material or where heavy cuts are taken.
Higher spindle speeds are used to machine softer materials in order to achieve better surface finishes.
Higher speeds also apply when using small diameter cutters for light cuts on frail work pieces and delicate
setups.
Note: Cutter diameter greatly affects spindle speeds. The larger the diameter, the lower the spindle speed.