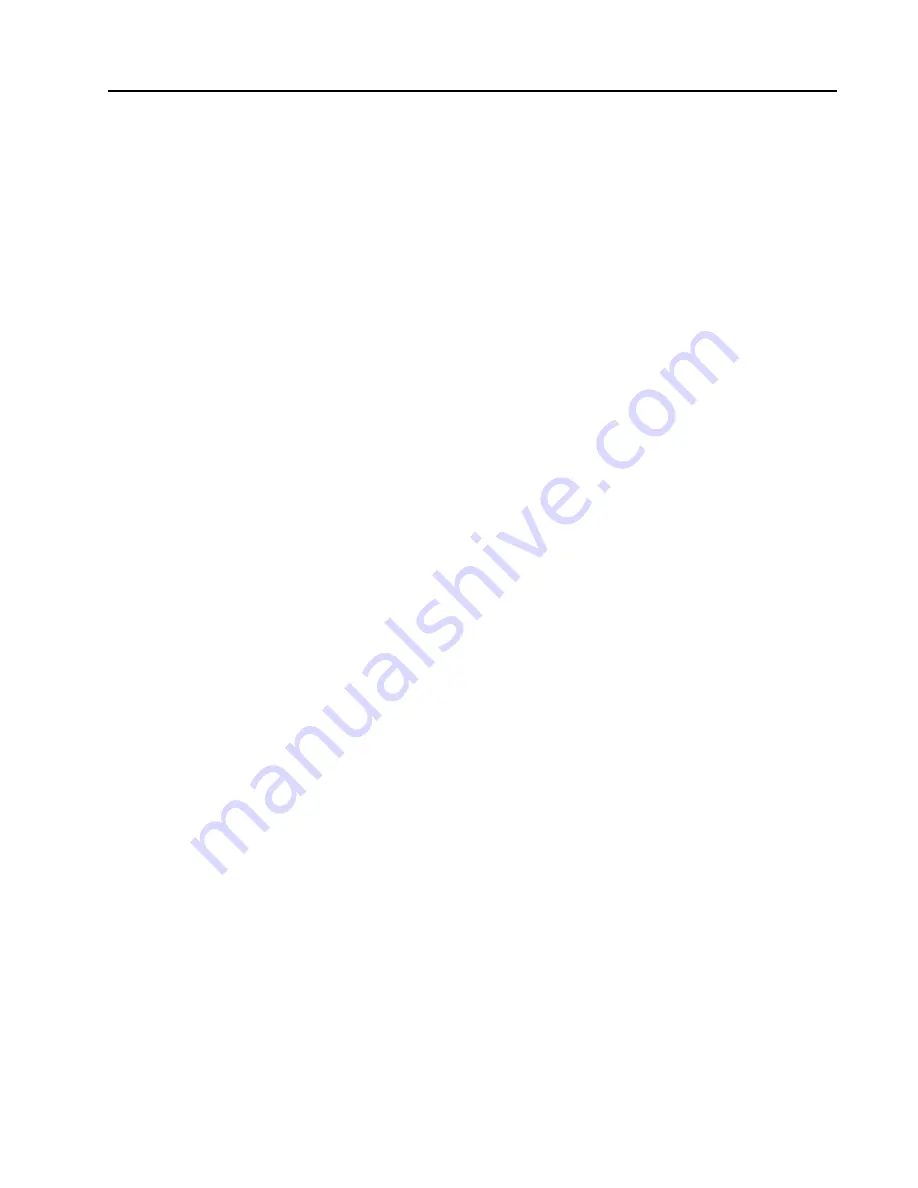
Toyota Pallet Truck Service Manual
Systems Overview
Theory of Operation
00700-CL390-04, Issued: 2 February 2004
3-7
Theory of Operation
Lift/Lower
The lift/lower system consists of an electrically
operated hydraulic pump and related
components.
The hydraulic pump assembly consists of a
positive displacement rotary gear pump with
reservoir mounted to an adapter. A DC electric
motor is mounted to the opposite side of the
pump adapter. An adjustable relief valve, check
valve, and a solenoid operated release valve are
located within the adapter.
With the forks elevated, the normally-closed
solenoid valve and the check valve prevent
hydraulic fluid from returning to the reservoir.
Lift
When the battery is plugged in, the key switch
(SW1) is ON and the lift button is pressed:
•
the lift switch closes
•
the lift pump contactor closes, causing the
lift pump to operate
•
Hydraulic fluid is drawn through the
screen in the reservoir into the lift
pump and is forced into the lift
cylinders.
•
As the pump rotates, oil is forced out
the pressure port through the lift hose
to the lift cylinders. Oil cannot return to
the reservoir because of the closed
pressure relief valve and closed
lowering solenoid valve.
•
Hydraulic pressure in the lift cylinders
raises the forks. Lift cutout switch will
interrupt power to the lift motor when
the forks reach a preset lift limit.
When the lift switch is open:
•
the pump contactor coil is de-energized,
stopping the lift motor and pump. The
forks are held in position by hydraulic
fluid trapped in the lift cylinders by the
check valve (static position of the relief
valve) and the closed lowering solenoid.
The relief valve will open if the hydraulic
pressure exceeds the preset limit.
Lower
When the battery is plugged in, the key switch
is ON and the lower button is pressed:
•
the lower switch is closed
•
the lowering solenoid opens
•
hydraulic fluid in the lift cylinders returns
to the hydraulic reservoir through the
lowering valve and the flow control valve
•
the forks lower
Directional/Speed Control
The directional/speed control descriptions
assume the battery is charged and connected
and the key switch is ON.
The control handle must be in the correct
position to close the brake (deadman) switch
(SW2) and release the brake. See “Brake
Switch” on page 6-18. When the brake switch is
closed, the main contactor (M1) is energized.
N
OTE
:
When the control handle is released and
the brake (deadman) switch opened, the
main contactor (M1) will remain
energized for several seconds before
de-energizing.
Forward
When the directional/speed control is rotated in
the forward direction from neutral:
•
the forward directional switch (SW3) is
closed and B+ is applied to PMC-10 of the
motor controller
•
resistance across the throttle
potentiometer (VR-4 to VR-2) increases
from zero ohms to a maximum of 6,500
ohms. Throttle input voltage is then
generated at PMC-16 with respect to (wrt)
PMC-14. As throttle input voltage rises
above the neutral band threshold, the
motor controller begins to provide current