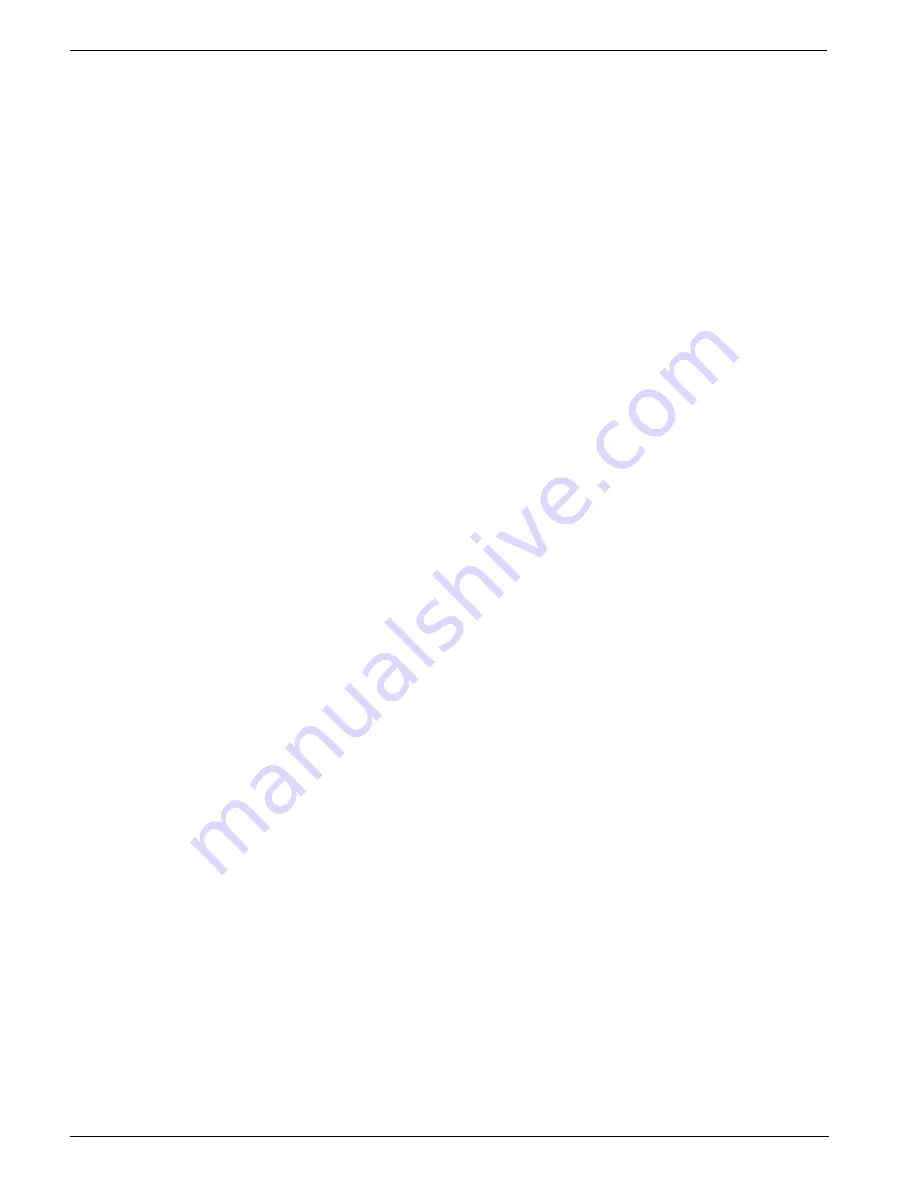
TIC-LF620E
2
DO1 and DO2 functions
— One of the following
functions can be assigned to DO1 and/or DO2
•
Pulse output (available only for DO1,DO2)
Pulse rate: Max 10kHz (10,000pps) (DO1)
Max 100Hz ( 100pps) (DO2)
(Over 1kpps, auto-setting)
Pulse width: 0.3 to 500ms (but less than half of
the period for 100% flow rate)
Note: The same and simultaneous
pulse is not
available between DO1 and DO2.)
•
Multi-range selection outputs (Note 1)
•
High, High high, Low, and/or Low low alarm
outputs (Note 2)
•
Empty pipe alarm output (Note 2)
•
Preset count output
•
Converter failure alarm output(Note 2)
Note 1:
Two outputs (DO1 and DO2) are needed for
4-range switching and forward/reverse
2-range switching.
Note 2:
Normal Open (default set) or Normal Close
is selected for alarm outputs when
programming.
When power failure occurs, unit will be
fault to Normal Open.
Communications output
:
・
HART(std.)
Digital signal is superimposed on 4–20mAdc
current signal as follows:
• Conforms to HART protocol
Load resistance: 240 to 750
Load capacitance: 0.25µF maximum
Load inductance: 4mH maximum
•
PROFIBUS (opt.)
Protocol : PROFIBUS-PA
Baurate : 31.25kbps
Bus voltage : 9-30VDC
Consumption electric current of bus:less than 16mA
Manufacture Ident-No. : 093B
HEX
Standard Ident-No. : 9740
HEX
Slave address : 0-126 (Default address is 126)
Profile : Profile Ver.3.01 for Process Control
Devices
Function blocks : AI(Flow)
×
1 , Totalizer
×
1
• Modbus(opt.)
Physical layer : RS485
Protocol : Modbus
Mode : RTU
Baudrate : 4800, 9600, 19200bps
Data length : 8bit
Parity bit : None, Odd, Even
Stop bit : 1bit, 2bit
Error check : CRC-16
Max. station number : 32(with Master device)
Max. cable length : 1.2km (Note)
Note: This length is specification of 3 line
connection.
LCD display:
Full dot-matrix 128×128 dot LCD
display (back-light provided)
A parameter change will rotate the display.
Parameter settings
— Parameters can be set as
follows:
• IR Switches
: Three key switches are provided to
set configuration parameters.
• Digital communication
: HART, PROFIBUS or
Modbus is needed to set parameters.
•Zero adjustment:
Zero point adjustment can be
started by pressing the switch in the converter.
Damping:
0.5 to 60 seconds (selectable in one
second increments)
Zero and span calibration:
Built-in calibration
signal source allows converter unit check.
Conditions when power fails:
Parameter setting
values are stored in non-volatile memory and the
values will be restored when the power returns to
normal condition. The outputs and display will
remain as follows when power fails.
• Current output: 0mAdc
• Digital output: OFF
• LCD display: No display
• PROFIBUS:
No communication
Power supply:
One of the following can be selected:
• 100 to 240Vac, 50/60Hz
(allowable voltage 80 to 264Vac)
110Vdc
(allowable voltage 90 to 130Vdc)
• 24Vdc (allowable voltage 18 to 36Vdc)
Surge protection:
Arresters are installed in the
power supply, and a current signal output circuit.
Structure:
IP 67 and NEMA 4X Watertight
Case:
Aluminum alloy (equivalent of IP 67)
Coating:
Acrylic resin-baked coating, pearl-gray
colored
Cable connection ports:
Cable glands
—
LF620 and LF622 without cFMus Approval:
Provided as standard
OD of cable
φ
11~13mm
Material Nylon 66
G (PF) 1/2 male threads..
Note: When PROFIBUS or Modbus option is
specified , cable gland size is
φ
6
~
8mm for signal cable,
φ
11
~
13mm
for power cable
LF620F and LF622F with cFMus Approval:
Not provided, 1/2-14NPT male
threads are required.