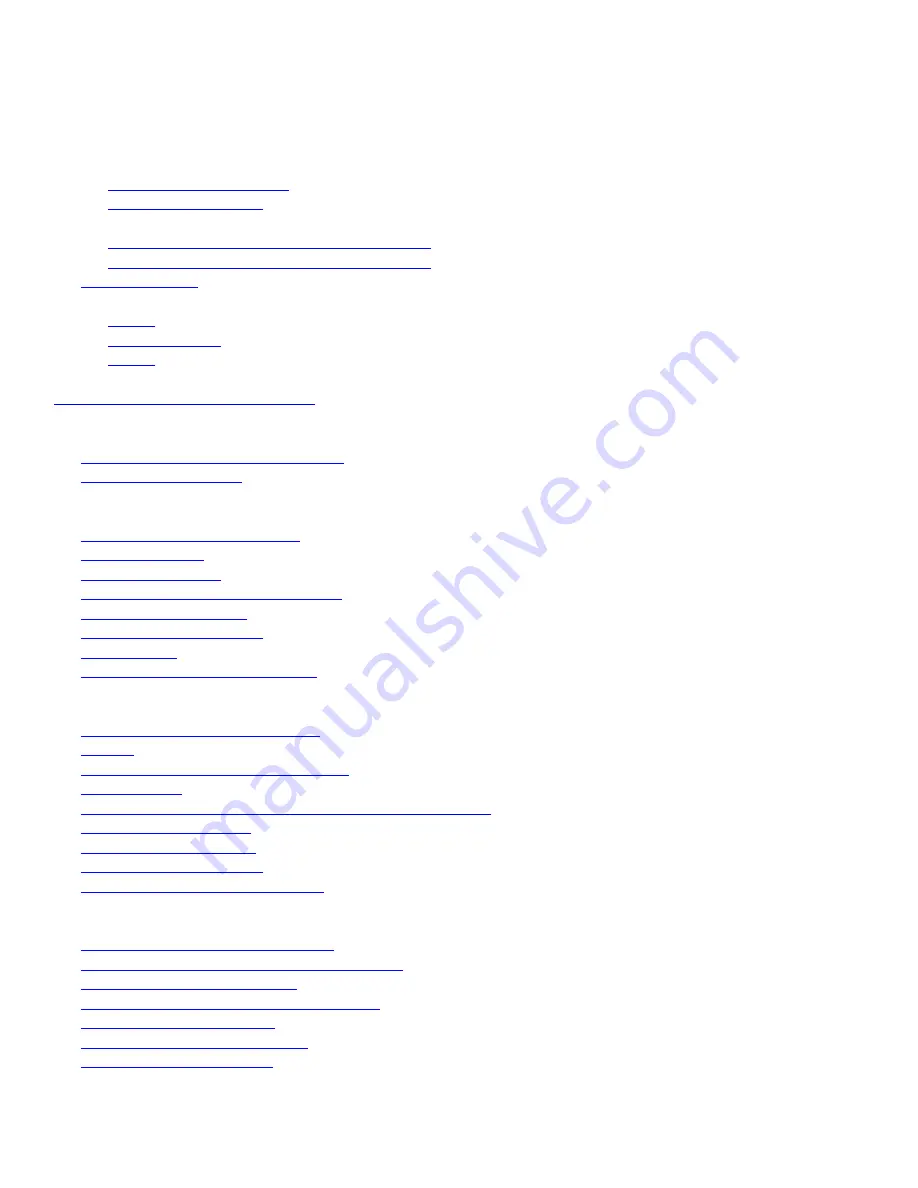
TORO TIMECUTTER Z SERVICE MANUAL
Table of Contents – Page 1 of 2
QUICK REFERENCE
SAFETY INFORMATION
GENERAL INFORMATION
THINK SAFETY FIRST
SPECIFICATIONS
ENGINE SPECIFICATIONS - (Z16-44 & Z17-44)
ENGINE SPECIFICATIONS - (Z17-52 & Z18-52)
MAINTENANCE SCHEDULE
GREASING AND LUBRICATION
SERVICE INTERVAL/SPECIFICATION
LUBRICATION POINTS
ENGINE
BRIGGS & STRATTON ENGINE
KOHLER ENGINE
KAWASAKI ENGINE
BRIGGS & STRATTON AIR CLEANER
KOHLER AIR CLEANER
KAWASAKI AIR CLEANER
SPARK PLUG
ENGINE REMOVE AND REPLACE
TRANSAXLE
TROUBLESHOOTING CHECKLIST
FLUIDS
REMOVE AND REPLACE TRANSAXLE
REASSEMBLY
CONTROL HANDLE-RETURN TO NEUTRAL ADJUSTMENT
PURGING THE SYSTEM
NEUTRAL ADJUSTMENT
TRACKING ADJUSTMENT
CONTROL HANDLE ADJUSTMENT
CHASSIS
REMOVE AND REPLACE DAMPERS
REMOVE AND REPLACE CONTROL LINKAGE
REPLACE CONTROL LINKAGE
REMOVE AND REPLACE BRAKE LINKAGE
REPLACE BRAKE LINKAGE
PARKING BRAKE ADJUSTMENT
REPLACE TRACTION BELT
Содержание TimeCutter Z Series
Страница 3: ...TimeCutter Z TimeCutter ZX Service Manual ...
Страница 24: ...1 10 TimeCutter Z Service Manual THIS PAGE INTENTIONALLY LEFT BLANK ...
Страница 28: ...THIS PAGE INTENTIONALLY LEFT BLANK 2 4 TimeCutter Z Service Manual ...
Страница 70: ...A5 26 TimeCutter ZX Service Manual 5 TRANSAXLE THIS PAGE INTENTIONALLY LEFT BLANK ...
Страница 114: ...8 8 TimeCutter Z Service Manual ELECTRICAL SYSTEMS 8 Electrical Schematic Briggs Stratton ...
Страница 115: ...ELECTRICAL SYSTEMS TimeCutter Z Service Manual 8 9 8 Electrical Schematic Kawasaki ...
Страница 116: ...8 10 TimeCutter Z Service Manual ELECTRICAL SYSTEMS 8 Electrical Schematic Kohler ...
Страница 117: ......
Страница 118: ...492 4736 Revised 5 07 ...