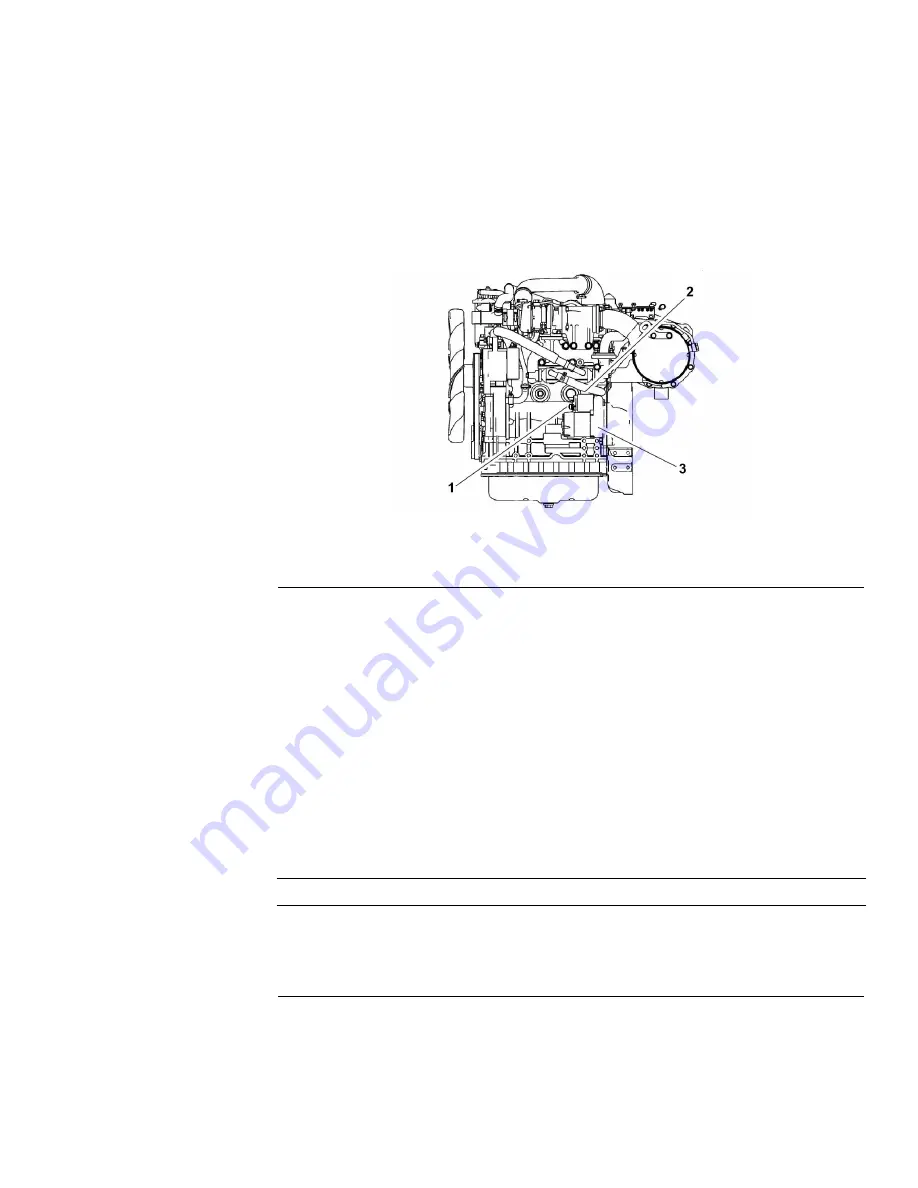
Priming the Hydraulic Pumps (continued)
(traction) pump have sufficient fluid during initial start-up and running. The
pumps can be primed by using a remote starter switch (refer to
) to crank the engine which allows the pumps to prime.
Use the following procedure to prime the hydraulic pumps:
1. Ensure that the key switch is in the O
FF
position and the key is removed
from the key switch.
2. Check the hydraulic-fluid level in the hydraulic reservoir and add correct
quantity of fluid if necessary; refer to the
Operator’s Manual
.
g193733
Figure 142
1.
B+ terminal
2.
Starter solenoid
3.
Starter motor
Note:
A blue wire connects to the starter motor solenoid B+ terminal (
). It is not necessary to remove this blue wire from the solenoid terminal
for hydraulic pump priming.
3. Connect the remote starter switch electrical leads to the starter motor
solenoid B+ terminal and positive post of the battery.
4. Engage the remote starter switch and crank the starter for 30 seconds to
prime the hydraulic pumps. Wait for 30 seconds to allow the starter motor and
starter solenoid to cool. Repeat the cranking procedure for the second time.
5. Disconnect the remote starter switch leads from the starter motor solenoid
terminal and positive post of the battery.
Flushing the Hydraulic System
IMPORTANT
Flush the hydraulic system whenever there is a severe component
failure or the system is contaminated (for example, the fluid appears
milky, black, or contains metal particles).
Reelmaster
®
5410/5510/5610 Series
Page 6–147
Hydraulic System: Service and Repairs
15216SL Rev C
Содержание Reelmaster 5510 Series
Страница 4: ...NOTES NOTES Page 4 Reelmaster 5410 5510 5610 Series 15216SL Rev C...
Страница 10: ...Preface Page 10 Reelmaster 5410 5510 5610 Series 15216SL Rev C...
Страница 18: ...Safety Safety and Instructional Decals Page 1 8 Reelmaster 5410 5510 5610 Series 15216SL Rev C...
Страница 118: ...Kubota Gasoline Engine Service and Repairs Page 5 26 Reelmaster 5410 5510 5610 Series 15216SL Rev C...
Страница 136: ...g230013 Figure 64 Hydraulic System Hydraulic Schematics Page 6 18 Reelmaster 5410 5510 5610 Series 15216SL Rev C...
Страница 137: ...g213698 Figure 65 Reelmaster 5410 5510 5610 Series Page 6 19 Hydraulic System Hydraulic Schematics 15216SL Rev C...
Страница 356: ...Hydraulic System Service and Repairs Page 6 238 Reelmaster 5410 5510 5610 Series 15216SL Rev C...
Страница 366: ...g213684 Figure 198 Electrical System InfoCenter Display Page 7 10 Reelmaster 5410 5510 5610 Series 15216SL Rev C...
Страница 488: ...Electrical System Service and Repairs Page 7 132 Reelmaster 5410 5510 5610 Series 15216SL Rev C...
Страница 594: ...Cutting Unit Service and Repairs Page 9 64 Reelmaster 5410 5510 5610 Series 15216SL Rev C...
Страница 620: ...Belt Driven Groomer Optional Service and Repairs Page 10 26 Reelmaster 5410 5510 5610 Series 15216SL Rev C...
Страница 640: ...Universal Groomer Optional Service and Repairs Page 11 20 Reelmaster 5410 5510 5610 Series 15216SL Rev C...
Страница 650: ...Page A 10 15216SL Rev C Reelmaster All Models Drawing 120 6356 Rev D Sheet 1 of 2 Wire Harness Drawing Main g219150...
Страница 651: ...Reelmaster All Models Drawing 120 6356 Rev D Sheet 2 of 2 15216SL Rev C Page A 11 Wire Harness Drawing Main g219151...
Страница 652: ...Page A 12 15216SL Rev C Reelmaster All Models Drawing 115 8081 Rev C Sheet 1 of 2 Wire Harness Drawing Seat g219152...
Страница 653: ...Reelmaster All Models Drawing 115 80812 Rev C Sheet 2 of 2 15216SL Rev C Page A 13 Wire Harness Drawing Seat g219153...
Страница 662: ......