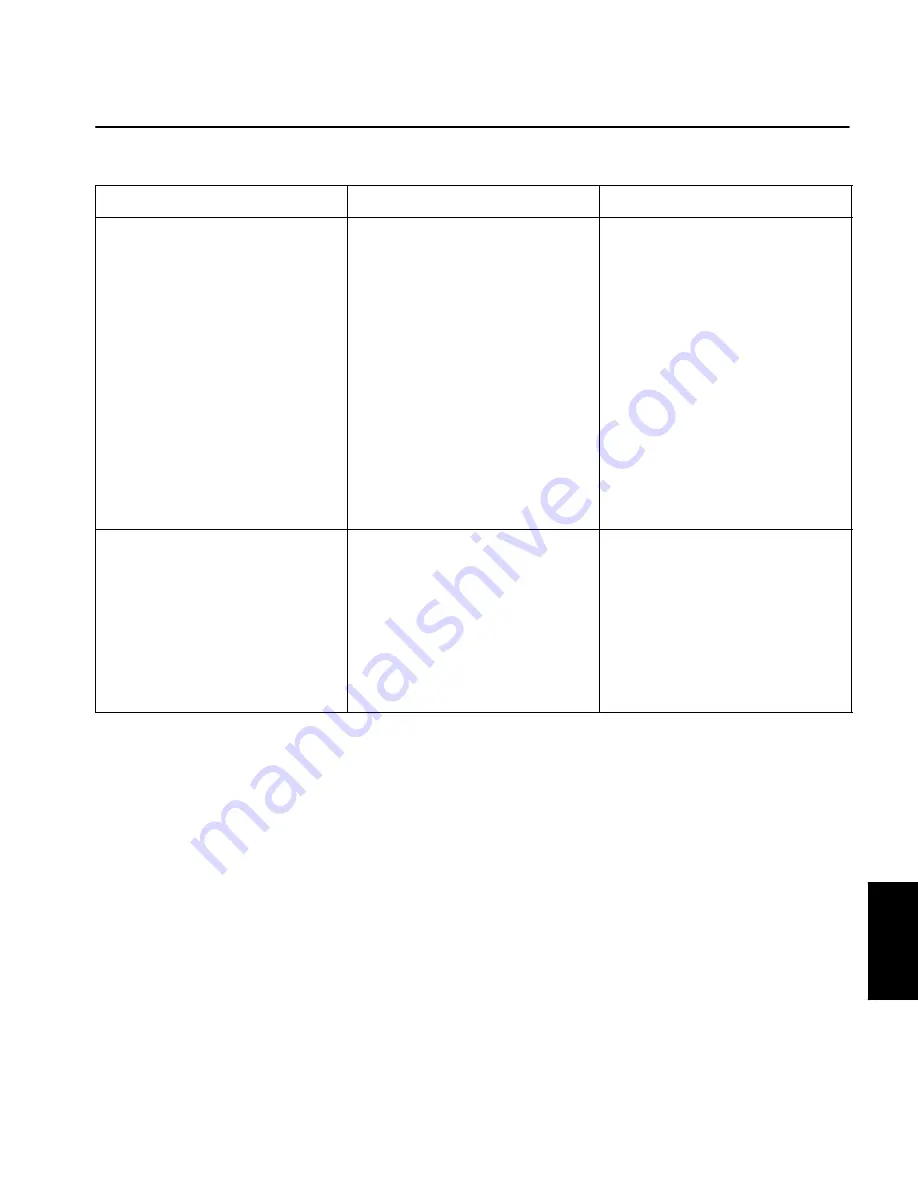
Reelmaster 5010 Series
Groomer
Page 8 -- 3
Troubleshooting
Groomer Reel Mechanical Problems
Problem
Possible Causes
Correction
No rotation of the groomer reel.
The groomer drive belt needs to be
adjusted.
Seized groomer reel or idler bear-
ing(s) in groomer side plate(s).
Broken or damaged idler spring.
The groomer drive belt is worn, bro-
ken or damaged.
Grooming depth is too deep.
Adjust groomer drive belt.
Identify and replace faulty bear-
ing(s).
Replace spring.
If the drive belt slips, it probably is
out of adjustment or worn.
Repair or replace drive belt if nec-
essary. A broken or worn belt could
be the result of improper belt rout-
ing or seized bearings in groomer
assembly.
Change grooming depth.
The turf is damaged or has uneven
grooming.
The groomer reel blades are bent,
damaged or missing.
The groomer reel shaft is bent or
damaged.
Grooming depth is not equal on
both ends of groomer reel.
Repair or replace blades if neces-
sary.
Replace groomer reel shaft.
Adjust depth if necessary. Check
and adjust cutting unit set up (level
bedknife to reel, level rear roller to
reel, set height--of--cut, etc.).
Groomer
Содержание Reelmaster 5210
Страница 2: ...Reelmaster 5010 Series This page is intentionally blank ...
Страница 4: ...Reelmaster 5010 Series This page is intentionally blank ...
Страница 10: ...0 09375 Reelmaster 5010 Series Page 2 2 Product Records and Maintenance Equivalents and Conversions ...
Страница 32: ...Reelmaster 5010 Series Page 3 18 Kubota Diesel Engine This page is intentionally blank ...
Страница 59: ...Reelmaster 5010 Series Hydraulic System Rev C Page 4 27 This page is intentionally blank Hydraulic System ...
Страница 95: ...Reelmaster 5010 Series Hydraulic System Rev C Page 4 63 This page is intentionally blank Hydraulic System ...
Страница 103: ...Reelmaster 5010 Series Hydraulic System Rev C Page 4 71 This page is intentionally blank Hydraulic System ...
Страница 105: ...Reelmaster 5010 Series Hydraulic System Rev C Page 4 73 This page is intentionally blank Hydraulic System ...
Страница 111: ...Reelmaster 5010 Series Hydraulic System Rev C Page 4 79 This page is intentionally blank Hydraulic System ...
Страница 127: ...Reelmaster 5010 Series Hydraulic System Rev C Page 4 95 This page is intentionally blank Hydraulic System ...
Страница 133: ...Reelmaster 5010 Series Hydraulic System Rev C Page 4 101 This page is intentionally blank Hydraulic System ...
Страница 141: ...Reelmaster 5010 Series Hydraulic System Rev C Page 4 109 This page is intentionally blank Hydraulic System ...
Страница 148: ...Reelmaster 5010 Series Hydraulic System Rev C Page 4 116 This page is intentionally blank ...
Страница 204: ...Reelmaster 5010 Series Page 5 56 Electrical System This page is intentionally blank ...
Страница 207: ...Reelmaster 5010 Series Page 6 3 Chassis Rev C This page is intentionally blank Chassis ...
Страница 215: ...Reelmaster 5010 Series Page 6 11 Chassis Rev C This page is intentionally blank Chassis ...
Страница 230: ...Reelmaster 5010 Series Page 6 26 Chassis Rev C This page is intentionally blank ...
Страница 251: ...Reelmaster 5010 Series Cutting Units Rev C Page 7 21 This page is intentionally blank Cutting Units ...
Страница 255: ...Reelmaster 5010 Series Cutting Units Rev C Page 7 25 This page is intentionally blank Cutting Units ...
Страница 259: ...Reelmaster 5010 Series Cutting Units Rev C Page 7 29 This page is intentionally blank Cutting Units ...
Страница 270: ...Reelmaster 5010 Series Cutting Units Rev C Page 7 40 This page is intentionally blank ...
Страница 279: ...Reelmaster 5010 Series Groomer Page 8 9 This page is intentionally blank Groomer ...
Страница 288: ...Reelmaster 5010 Series Foldout Drawings Page 9 2 This page is intentionally blank ...
Страница 297: ...Rev B Page 9 11 This page is intentionally blank ...
Страница 298: ...Rev B Page 9 12 Reelmaster 5010 Series Main Wire Harness Drawing ...
Страница 300: ...Rev B Page 9 14 Reelmaster 5010 Series Seat Wire Harness Drawing ...
Страница 302: ...Rev B Page 9 16 Reelmaster 5010 Series Engine Wire Harness Drawing ...