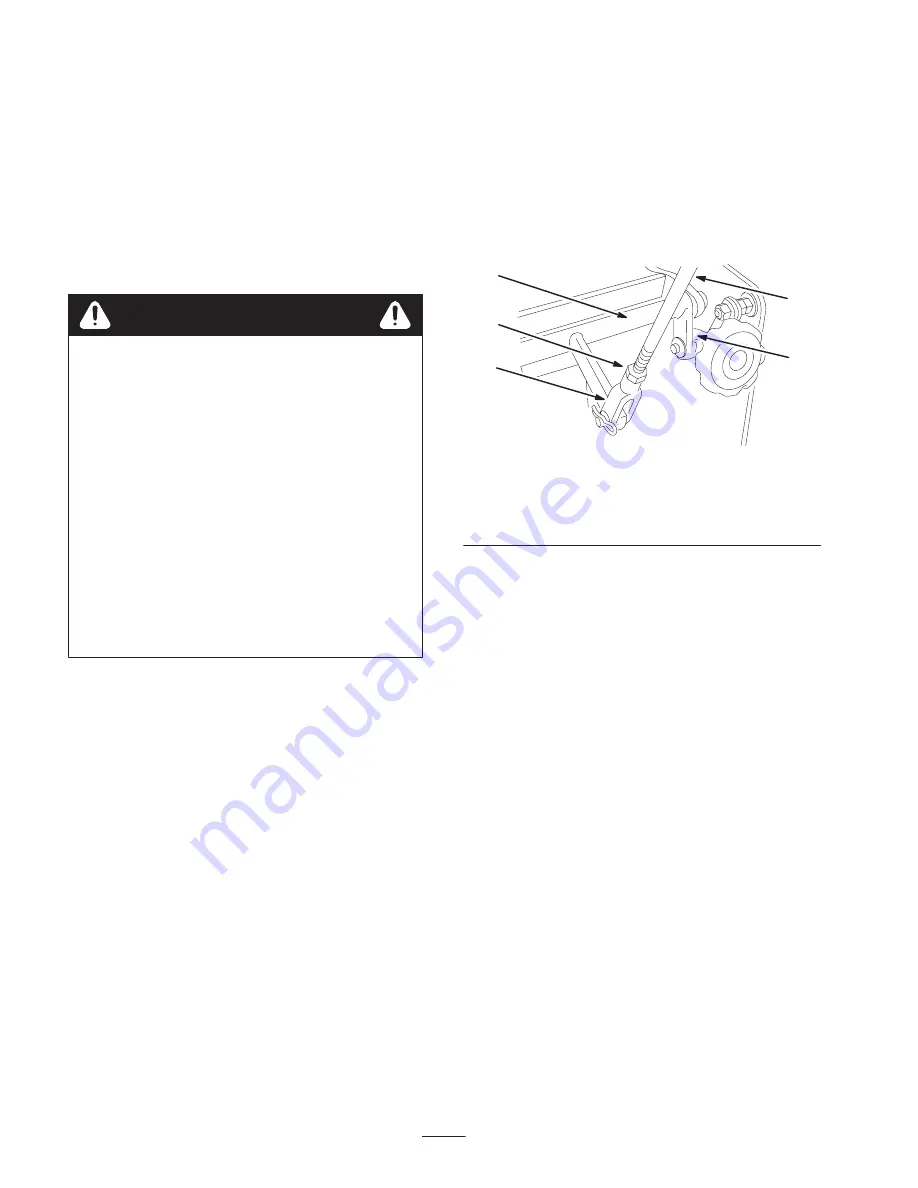
36
10.
Check the hydro control linkage adjustment. Refer to
Adjusting the Hydro Control Linkages on page 38.
Checking the Hydraulic Lines
After every 100 operating hours, check hydraulic lines and
hoses for leaks, loose fittings, kinked lines, loose mounting
supports, wear, weather and chemical deterioration. Make
necessary repairs before operating.
Note:
Keep areas around hydraulic system clean from grass
and debris build up.
Hydraulic fluid escaping under pressure can
penetrate skin and cause injury.
•
If hydraulic fluid is injected into the skin it must
be surgically removed within a few hours by a
doctor familiar with this type of injury.
Gangrene may result if this is not done.
•
Keep body and hands away from pin hole leaks
or nozzles that eject high pressure hydraulic
fluid.
•
Use cardboard or paper to find hydraulic leaks.
•
Safely relieve all pressure in the hydraulic
system before performing any work on the
hydraulic system.
•
Make sure all hydraulic fluid hoses and lines are
in good condition and all hydraulic connections
and fittings are tight before applying pressure to
hydraulic system.
Warning
Performing the Hydro Linkage
Adjustments
Perform the following linkage adjustments when the
machine needs maintenance. Perform steps Adjusting the
Speed Control Linkage through Adjusting the Tracking. If
an adjustment is needed, do them in the order that they are
listed.
Adjusting the Speed Control
Linkage
1.
Disengage the PTO and set the parking brake.
2.
Stop the engine and wait for all moving parts to stop
before leaving the operating position.
3.
Move the speed control lever (located on the console) to
the full forward position.
4.
Check the orientation of the tabs on the ends of the
speed control crank. These tabs should be pointing
straight down at the 6 o’clock position approximately
(Fig. 48).
5.
Adjust the threaded yoke at the bottom of the speed
control linkage until the tabs are at the 6 o’clock
position (Fig. 48).
3
5
2
4
1
Figure 47
1. Speed control rod
2. Yoke
3. Speed control crank
4. Tabs, 6 o’clock position
5. Jam nut
6.
Pull the speed control lever back to neutral.
7.
Check to make sure the safety switch is depressed and
there is a 5/16 inch (8 mm) space between the actuating
tab and the switch. (Fig. 48).
8.
If needed, adjust switch location to create the 5/16 inch
(8 mm) space (Fig. 48).