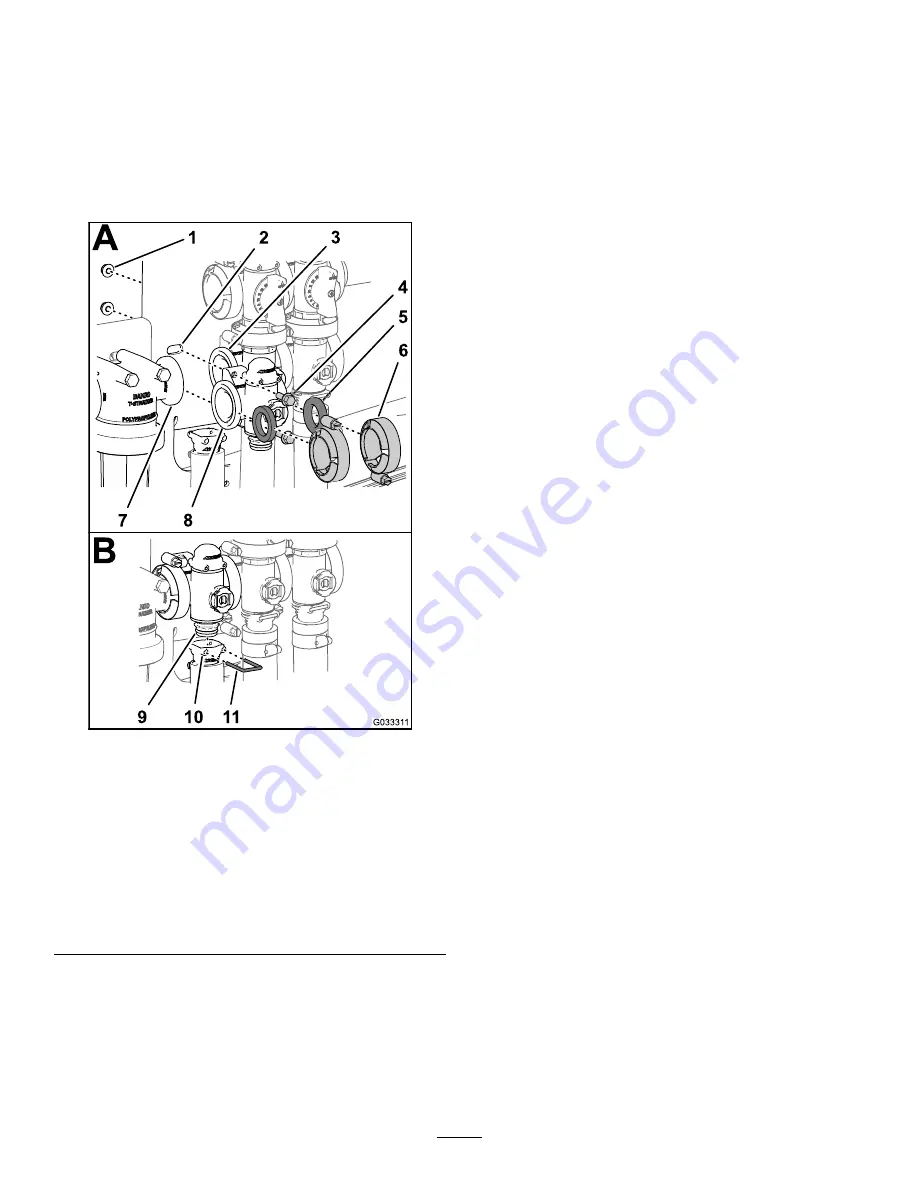
Installing the Rate Control
Manifold Valve
1.
Align a gasket between the flanges of the rate
control valve manifold and the pressure filter
head (
Note:
If needed, loosen the mounting hardware
for the pressure filter head as needed to provide
clearance.
g033311
Figure 80
1.
Locknut (1/4
inch)
5.
Gasket
9.
Coupling
(manifold-valve)
2.
Valve mount
6.
Flange clamp
10.
Socket (outlet
fitting)
3.
Flange
(agitation-valve)
7.
Flange
(pressure filter
head)
11.
Retainer
4.
Flanged-head
bolt (1/4 x 3/4
inch)
8.
Flange (rate
control valve)
2.
Assemble the rate control valve manifold,
gasket, and pressure filter head with a flange
clamp and tighten by hand (
3.
Align a gasket between the flanges of the rate
control valve and the agitation-valve manifold
(
A).
4.
Assemble the rate control valve manifold,
gasket, and agitation-valve manifold with a
flange clamp and tighten by hand (
A).
5.
Assemble the rate control valve to the valve
mount with the 2 flanged-head bolts and 2
flanged locknuts (
A) that you removed
in step
of
Removing the Rate-Control-Manifold
and torque the nut and bolt to
10 to 12 N∙m (90 to 110 in-lb).
6.
Assemble the outlet fitting onto the coupling
fitting at the bottom of the manifold for the rate
control valve (
7.
Secure the outlet fitting coupling fitting by
inserting a retainer into the socket of the outlet
fitting (
B).
8.
If you loosened the mounting hardware for the
pressure filter head, tighten the nut and bolt to
10 to 12 N∙m (90 to 110 in-lb).
Installing the Agitation-Manifold
Valve
1.
Align the flange of the agitation-valve manifold,
1 gasket, and the flange of the agitation-bypass
valve (
Note:
If needed, loosen the mounting hardware
for the master-section valve as needed to
provide clearance.
68