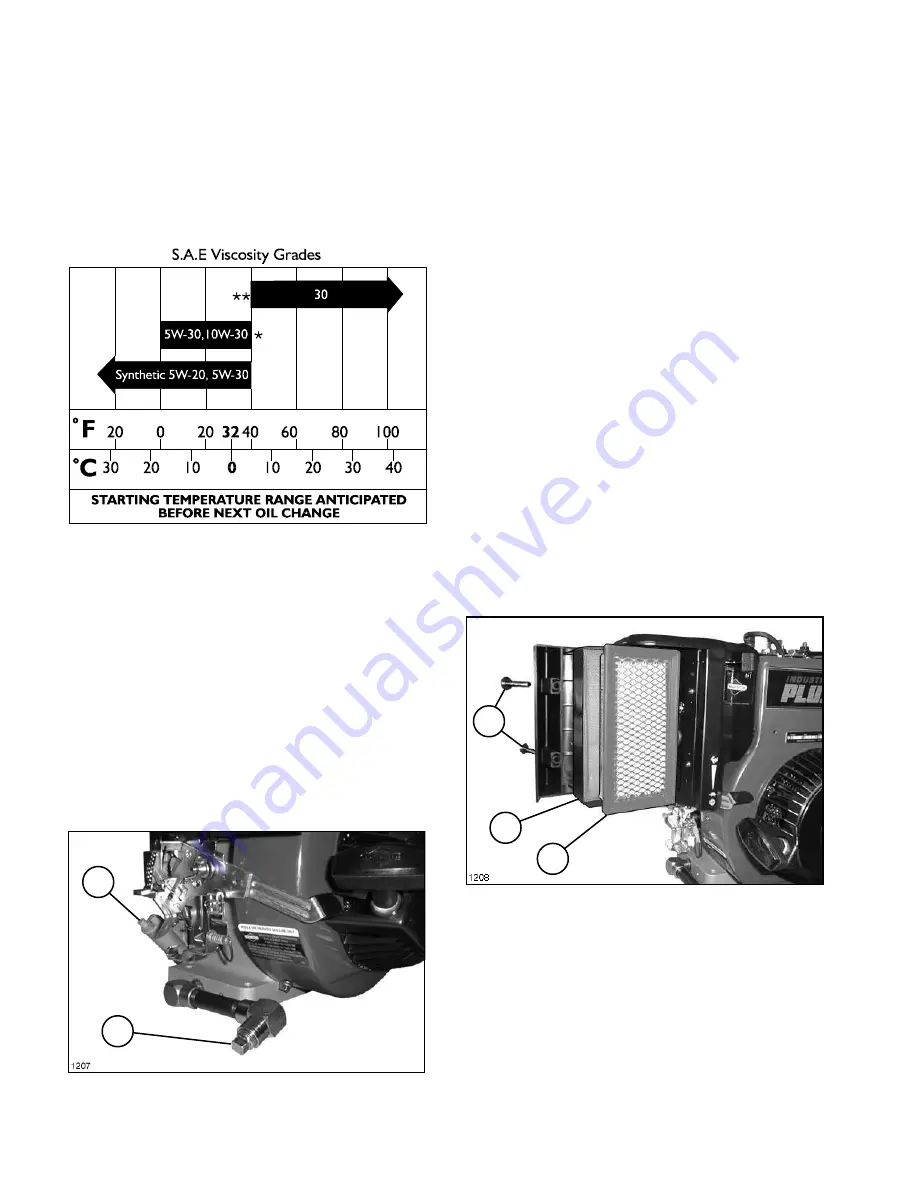
12
ENGINE LUBRICATION:
IMPORTANT! AFTER THE INITIAL RUN-IN
PERIOD (APPROXIMATELY 5 HOURS) AND
EVERY 25 HOURS THEREAFTER.
1.
Change the oil in the engines crankcase.
Change oil while the engine is warm. Refill with
new oil as recommended in the chart below.
ENGINE MAINTENANCE
* Air cooled engines run hotter than automotive
engines. Use of multi-viscosity oils (10W-30, etc.)
above 40 F (4 C) will result in high oil consumption
and possible engine damage. Check oil more
frequently if using these type oils.
** SAE 30 oil, if used below 40°F (4°C) will result
in hard starting and possible engine bore damage
due to inadequate lubrication.
Oil Capacity: Approximately 44 ounces or 1.3
liters.
2.
Remove the pipe plug in the end of the oil drain
pipe and let oil flow into a drain pan. When oil
stops, reinstall drain plug. See FIG. 2.
FIG. 2
1. Oil Fill
2. Drain Plug
AFTER EVERY 5 HOURS OR DAILY:
1.
Check the oil level in the engines crankcase
before engine start-up, while engine is cool. Have
the machine on a level surface.
2.
Clean the area around the oil/fill check plug
and remove it.
3.
The level should be up to but not over, the point
of overflowing the filler neck.
4.
If the level is low, add API service
classification SE, SF or SG. See viscosity chart
for the recommended weight.
5.
Reinstall the oil fill/check plug and tighten
securely. Make sure it is tightened to 13 ft. lbs.
(17.6 Nm) torque.
IMPORTANT! Keep the area around the fill tube
clean, to prevent dirt from falling into the engine.
AIR CLEANER:
Clean the Pre-Cleaner after every 25 hours of
operation. Clean more often in extreme dusty or
dirty conditions. Replace air cleaner parts if very
dirty.
1. Loosen Cover Screws and remove Cover,
Pre-Cleaner and Cartridge. See FIG. 3.
2. Wash Pre-Cleaner in liquid detergent and
water. Squeeze dry in clean cloth. Saturate in
engine oil. Squeeze in clean, absorbent cloth to
remove ALL EXCESS oil. If very dirty or damaged,
replace it.
3. Clean Cartridge by tapping gently on flat
surface. If very dirty or damaged, replace it. Do
NOT oil Cartridge.
4. Replace Cartridge, Pre-Cleaner and Cover.
Secure Cover with the (2) Cover Screws.
FIG. 3
1. Cover Screws
3. Cartridge
2. Pre-Cleaner
1
3
2
2
1
1205
Содержание 41440
Страница 30: ...30 Helping you put quality into...
Страница 31: ...31 Helping you put quality into...