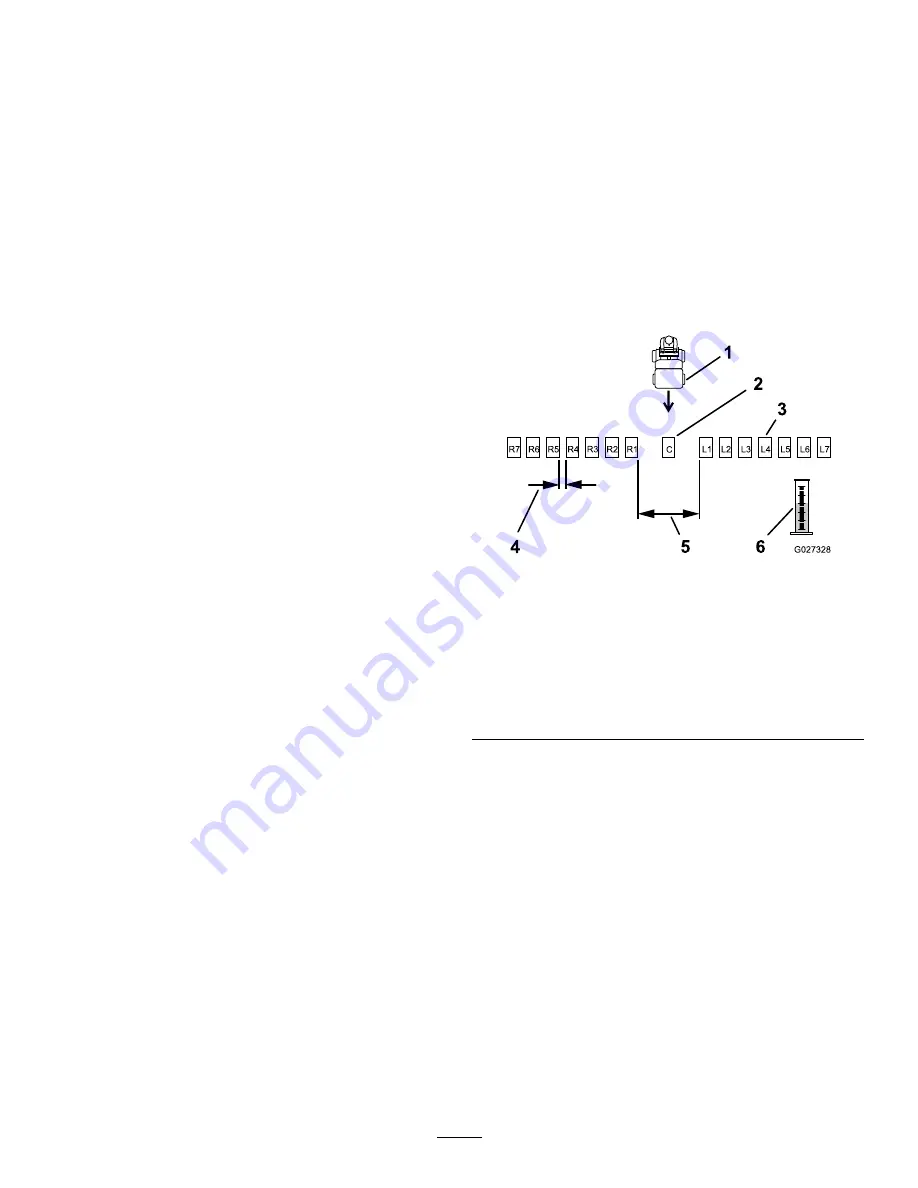
•
Pull the handle to broadcast granular product
from the left side of the impeller.
•
Push the handle to block granular product
from broadcasting at the left side of the
impeller.
3.
Rotate the handle of the deflector control
clockwise to lock the control (
Adjusting the Diffuser Control
Use the diffuser control to adjust the spread granular
product heavier to the left, consistent in the middle, or
heavier to the right.
1.
Rotate the handle of the diffuser control
counterclockwise to unlock the control (
2.
Adjust the diffuser control as follows:
•
Pull the handle to broadcast more granular
product from the right side of the impeller.
•
Center the handle to balance the broadcast
granular product evenly.
•
Push the handle to broadcast more granular
product from the left side of the impeller.
3.
Rotate the handle of the diffuser control
clockwise to lock the control (
Before Operating the Spreader
Before you start using the spreader, calibrate the
spreader for the material that you will disperse; refer
to
Calibrating the Spreader (page 26)
.
Important:
Prior to filling the hopper, verify that
you have set the proper spreader-application rate.
Calibrating the Spreader
Calibrate the spreader each time you change granular
materials. The spreader broadcasts material in a
pattern 1 to 7.6 m (3 to 25 ft) wide depending on the
material particle size, volume/density, impeller-motor
speed, rate of travel, and wind conditions.
Use the
Spreading Charts (page 30)
along with
information from
Determining the Distribution Pattern
(page 27)
,
Determining the Effective Spreading Width
(page 27)
, and
Calculating the Application Rate (page
when calibrating the spreader.
Preparing the Test Site and Machine
Operator supplied equipment:
15 shallow collection
pans and 15 graduated measuring cylinders
Note:
The most accurate method to measure
the distribution uses shallow collection pans and
graduated measuring cylinders. In the example below,
the 15 shallow collection pans approximately 30 cm
(12 inches) wide, 91 cm (36 inches) long, and 5 cm
(2 inches) tall.
1.
Place one pan in the center of the drive path.
Arrange the next two pans, one on each side,
far enough apart to allow adequate room for the
drive tires of the machine to pass around the
center pan.
2.
Place the remaining pans in a straight line as
shown in
or
.
•
For larger granule materials:
Space 6 additional pans, on each side, 12
inches (30 cm) apart (
).
g027328
Figure 20
Pan spacing for larger granule materials
1.
Spreader moving toward
pans
4.
L1 and R1 collection pan
gap (spread apart to allow
machine to pass through)
2.
Center pan
5.
30 cm (12 inch) gap
3.
Collection pans (gap
between each)
6.
Graduated measuring
cylinder
•
For small granule materials:
Place 6 additional pans, on each side, with
no gap in between each pan (
26