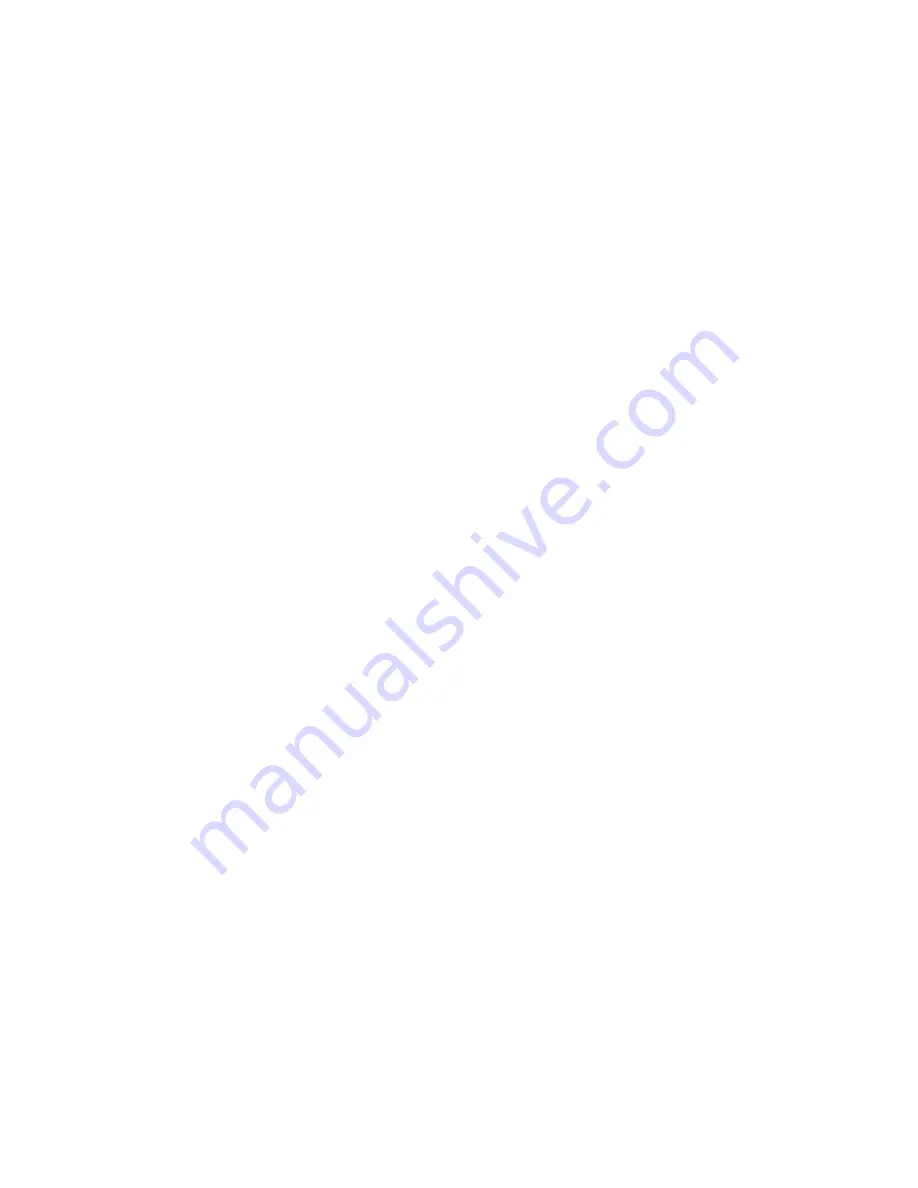
9
1. Wands and Tools
Rinse opening of tool with water to eliminate any debris.
Wand only - open and clean in-line strainer.
A. Disconnect the In-line Strainer by using the quick disconnect coupler.
B. Remove the filter and rinse with water.
C. Remove any debris from the strainer.
D. Keep o-ring and threads of the plug lubricated.
DEFOAM for use in this extractor is a good lubricant or use a non-petroleum based lubricant. This will ensure
a tighter seal.
E. Wipe tool with damp cloth and store with head up to prevent clogging of nozzle.
2. Filters
A. In-Line Strainer Filter - Disconnect the In-line Strainer Filter on the wand by using the quick disconnect
coupler. Remove the filter and rinse with water. Remove any debris from the strainer. Keep o-ring and
threads of the plug lubricated. DeFoam for use in this extractor is a good lubricant or use a nonpetroleum
based lubricant. This will ensure a tighter seal.
B. Gross Debris Filter - Remove the gross debris filter. Dump and clean debris at the end of each cleaning
job.
C. Disposable Inlet Filter - Remove the filter and rinse out and clean thoroughly or replace with part# 72776B.
D. In-Tank Filter - Unscrew this filter and rise thoroughly with water. Be sure to rinse both inner and outer
filter media. When finished screw cartridge filter back in place.
Periodic Maintenance
1. Check power cord for any breaks, separations, or cuts. Make sure the ground pin on the connector
is intact or the machine will be unsafe. Make sure the ground pin on all three prongs on the twist lock
connector are intact.
2. Check for plugged nozzles when using tools. If streaking occurs during cleaning, a plugged nozzle may be
the cause. A plugged or partially plugged nozzle can be identified by holding the tool 5-7” above the surface
and checking for an even spray pattern. To clean a plugged nozzle, remove the nozzle and direct pressurized
air backwards through the nozzle or backwash the nozzle with water. A convenient method is to insert
the nozzle into a garden hose ball valve, tighten the ball valve to a faucet, and turn on the water. (Ball valves
are available, part #7AX020). Inspect nozzle and repeat cleaning procedure, if necessary. Discard
nozzles that cannot be cleared. Tool nozzles wear and must be replaced after 200-250 hours of use.
3. Occasionally open the base and inspect hose and other connections for leaks. Repair or replace any
leaking parts. Always disconnect power cord, before removing side panels. Circuit Breakers: Overload
circuit breakers are placed in both the pump and vacuum circuits to protect against unusually heavy current
(ampere) loads. If either breaker trips, the pump motor or vacuum motor is overloaded.
4. It is very important to monitor machine operating hours for proper maintenance of the motors and
pumps. After 700 hours of operation, the vacuum motor brushes should be inspected by an authorized
repair station and replaced if worn (length is .5 inches or less).
5. Check vacuum motor performance using a vacuum gauge. Place this gauge on the tank inlet fitting with
the vacuum turned on. Water lift should be between 190 and 210 inches. If the reading is lower, check for
air leaks in the tank, cover gasket, and drain hose.
6. Check pump performance occasionally against built-in pressure gauge. Maximum pump running pressure
on the ECO-500 AW Series should be 500 ± 10 p.s.i, If the pumping pressure is outside of this range, call
your dealer or authorized station. After 400 hours, the pump valves should be replaced. After 700 hours of
operation the pump cam bearing and plunger should be replaced. The pressure regulator should be rebuilt
after 400 hours of operation.
Содержание 98825
Страница 12: ...12 This page intentionally left blank ...