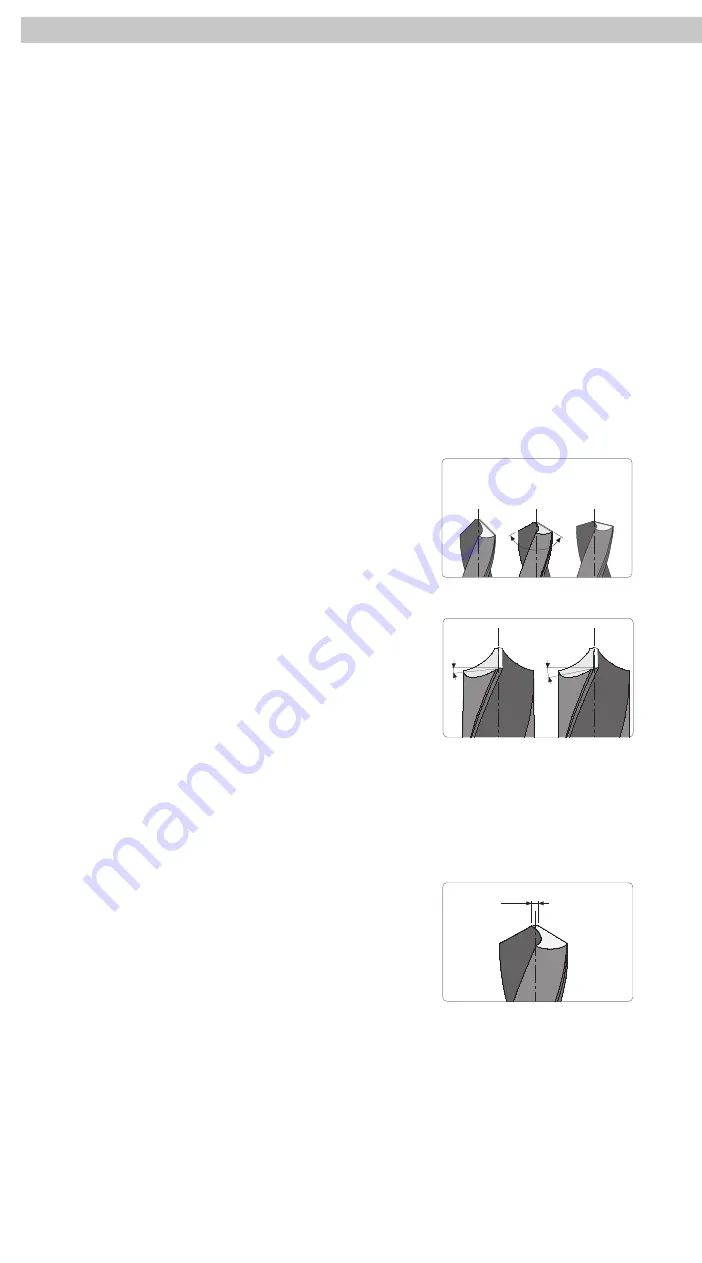
EN
4
Grinding, Shaping and Sharpening
The word
sharpening
is usually used for the final finishing of edge tools. Like all edge
tools, a drill bit needs to have the right
shape
before you can start to sharpen it.
Creating the initial shape often means that quite a lot of steel needs to be removed
when for example, you change the point angle of a drill or you shape a broken or
heavily worn drill. Once the geometry of the point is established, you maintain the
sharpness by sharpening. With the Tormek system you can exactly replicate an
existing shape and therefore you just need to touch up the edges.
The word
grinding
usually stands for both
shaping
and
sharpening
. In some opera-
tions, these slide into each other. With the Tormek System you can both shape and
sharpen your drill bits. Throughout this manual we use the word grinding, which
can mean both shaping and sharpening depending upon how much steel needs to
be removed.
Drill Point Geometry
Drill bits usually have a point angle of 118° or 130°.
There are also 120°, 135°, 140° and 150° point an-
gles. Hard steel and stainless steel require larger
point angles. Also aluminium is best drilled with a
larger point angle. When drilling plexiglass, the risk
of cracks when the drill goes through the mate-
rial is reduced with a larger point angle. Centering
drills usually have a 90° point angle.
A drill bit needs to have the right lip clearance
angle to cut the material. The clearance angle
varies from 7° to 14°. A drill with a larger clear-
ance angle cuts more easily, but if the angle is too
large, vibrations will occur and the drill will cut
irregularly and quickly become dull. If the clear-
ance angle is too small, the drill will not cut at all,
but will become hot and rapidly destroyed.
The optimal clearance angle for the job depends on the material – a harder material
requires a drill with a smaller clearance angle while a softer material can have a larger
angle. The size of the drill is also a determinant for the selection of the optimal clear-
ance angle. A larger drill should have a smaller clearance angle while a smaller should
have a larger one.
Many new drill bits are ground with a basic cone
point. The two cutting lips meet in the centre and
form a chisel edge,
C
. This point geometry is not
ideal, since the chisel edge needs to be pressed
into the material without cutting. The friction of the
chisel edge creates much heat, which decreases
the life of the drill bit. Since the chisel edge has no
tip, the drill walks when drilling a new hole, which
is not pre-drilled.
More expensive drill bits are ground with special points of various types. These
drills must be re-sharpened in their original production machines or in special ma-
chines, which are available only at a few specialist sharpening shops. They can also
be re-shaped to a 4-facet point with the Tormek attachment.
����
���
����
���
��
�