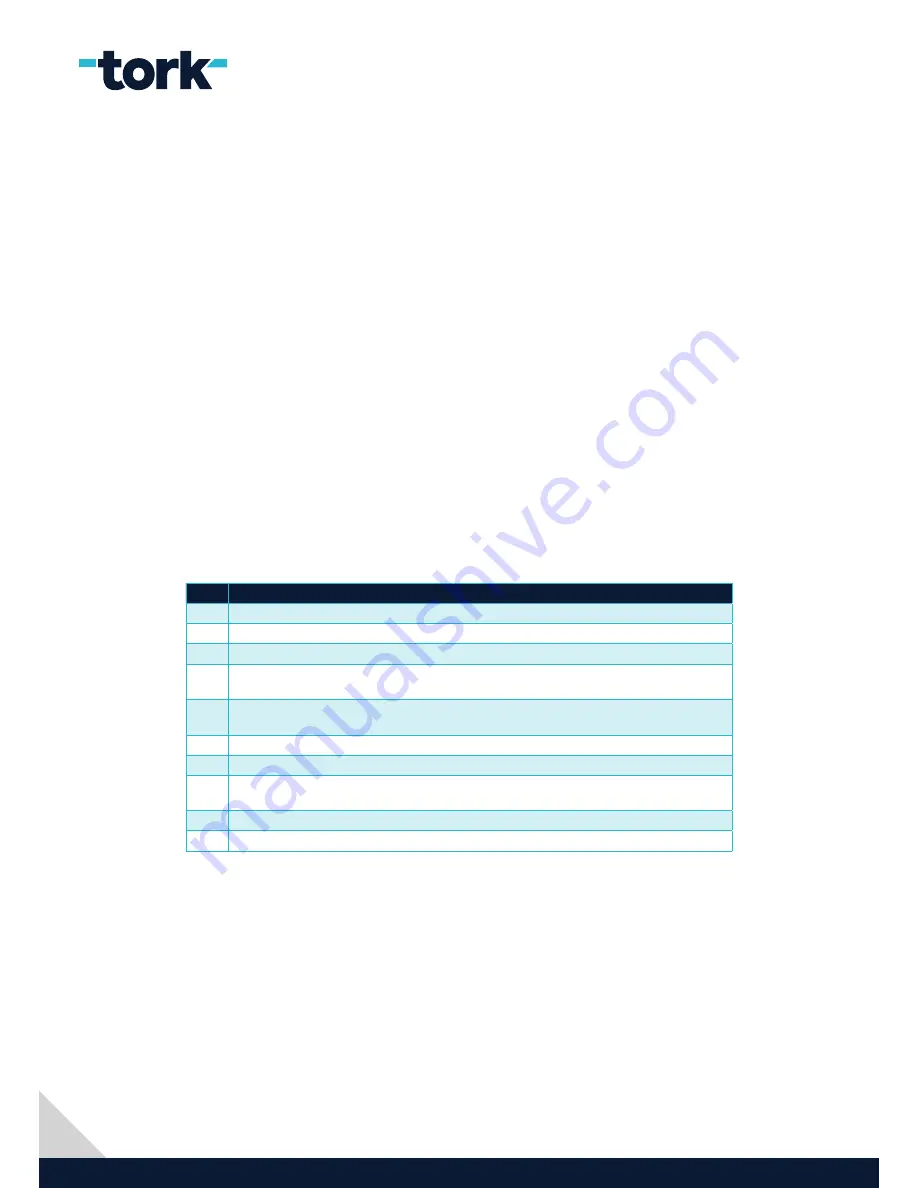
6) OPERATION AND MAINTENANCE
• It is recommended that pneumatic actuators are operated every 3 months in case of long-term storage and inactivity. This will
prevent the flexibility of the sealing equipment and prevent permanent deformations.
• The amount of oil in the body should be checked once a year in working products and piston and moving surfaces must be
lubricated with grease.
• All air inlets and outlets should be closed for prevent pollutants or abrasive substances from entering not only in the actuator but
also in all equipment such as directional control valves or locators. All openings, such as the power line to the junction boxes, must
also be closed.
• Use appropriate silencers on actuator or directional valves.
• Actuators should not be stored in an atmosphere which is harmful to the sealing material. If it is, closed warehouse must be
preferred.
• It is recommended to replace piston and shaft sealing and lining elements once every 2 years in working products.
• The air quality to be used for the actuator must be comply with ISO 8573-1: 7-4-4 (Particle - Water - Oil) standards.
6.1 Proof Test Interval
The objective of proof testing is to detect failures within the device that are not detected by any automatic diagnostics of the system.
Of main concern are undetected failures that prevent the SIF from performing its intended safety function.The proof tests must be
performed at every year. The suggested proof test consists of the steps as described in the table 3.
Proof test coverage factor (PTC) = 95 %
6.2 Maintenance
After five years a complete maintenance and overhauling should be performed. Within this procedure aged and worn components
should be changed. The device must be maintained inaccordance to Installation, Operation and Maintenance manual.Due to the
intensive proof the Maintenance Coverage Factor can be set to: MTC = 100 %
6.3 Repair and Replacement
Repair procedures in the device Installation, Operation and Maintenance manual must be followed. The SIL rating of the device may
be voided if the repair is not performed with OEM parts and serviced by unqualified personnel.
Step
Action
1
Bypass the safety function and take appropriate action to avoid a false trip
2
The actuator is brought to the half-open position.
3
Closing time and pressure values from both channels are measured
4
Pressure values from both channels are measured again after nearly 10 seconds have
elapsed.
5
Determined if there is any air leakage. Air leakage shows to determine if the actuator
is damaged or the seals are broken.
6
The actuator is brought to the full-open position. The opening time is measured
7
The opening and closing times show to determine if the actuator is jammed or normal.
8
Inspect the appliance and other last components for any leakage, visible damage or
contamination.
9
Record the test results and any failures in your company’s SIF inspection database
10
Remove the bypass and restore normal operation
Tab 16.
Proof test
SMS-TORK Endüstriyel Otomasyon Ürünleri San. Tic. Ltd. Şti.
26
valve & automation