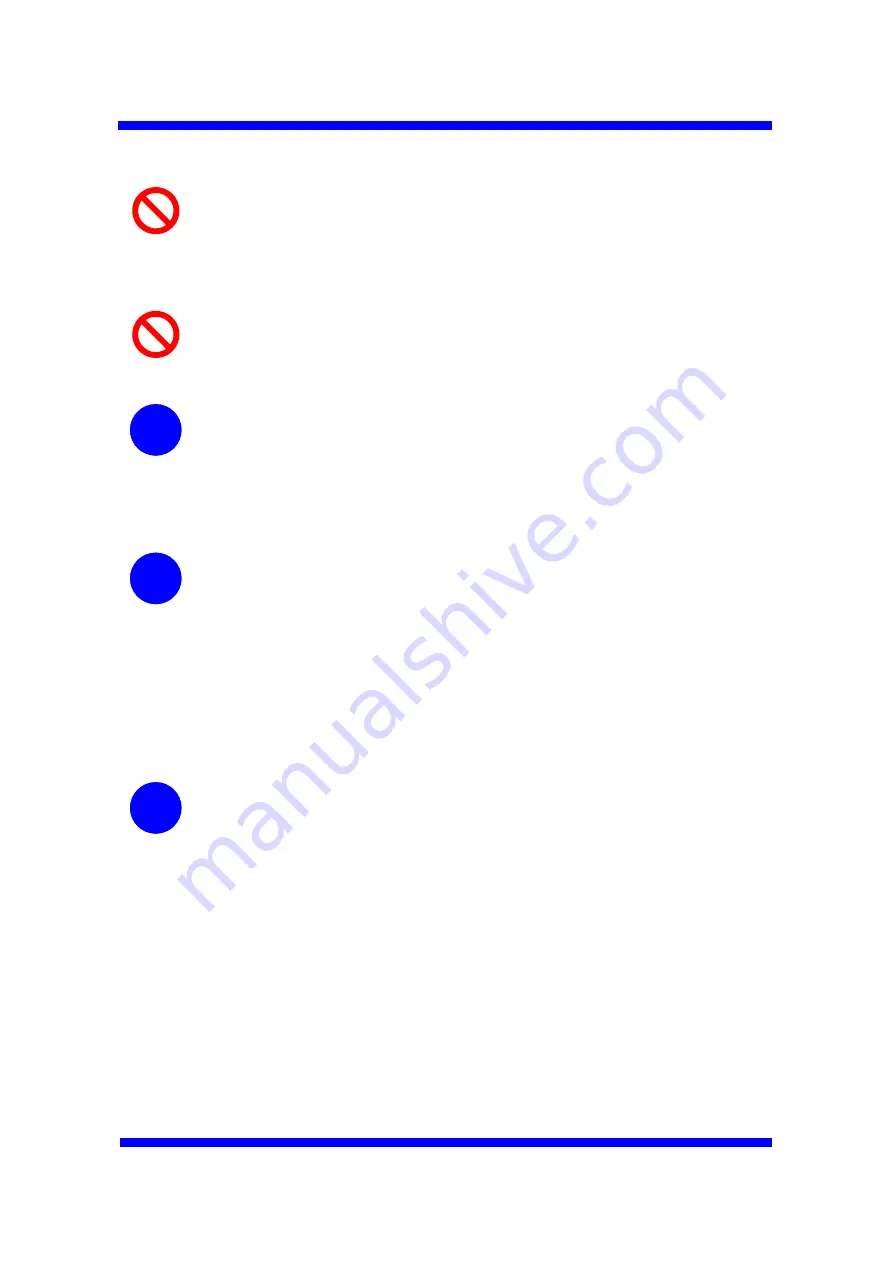
7
Do not exceed the maximum applicable pressure of 300 kPa (43.5
PSI). Higher pressures can damage the modules. Do not exceed
the maximum temperature of 40 degree C (104 degree F). The
higher temperature damages the modules.
Do not freeze the membrane modules.
The operating conditions, including the filtration flux and the periodical
physical cleaning, must be properly set-up otherwise the
trans-membrane pressure may rise too quickly. The operation range
is described in the latter section of this manual.
Do not overfeed air to the modules. Excessive scrubbing air
damages the membranes and/or shortens the membrane life.
The air flow rate should be within the range below for each module
type.
HFUG-2020AN: 4.8 – 9.0 Nm
3
/h (2.8 – 5.3 scfm)
The maximum required air pressure during the air-scrubbing for inside
of the module will be 40 kPa (6 PSI).
At the integrity tests, such as Pressure Decay Test (PDT) or Diffusive
Air Flow (DAF) Test, keep the air pressure below 130 kPa (18.9 PSI).
Keep the source air pressure lower than 200 kPa (29 PSI), to prevent
excess air inflow. All the air used for air scrubbing and integrity
testing must be dry oil-free air.
Prohibited
!
!
Instruction
!
!
Instruction
!
!
Instruction
Prohibited