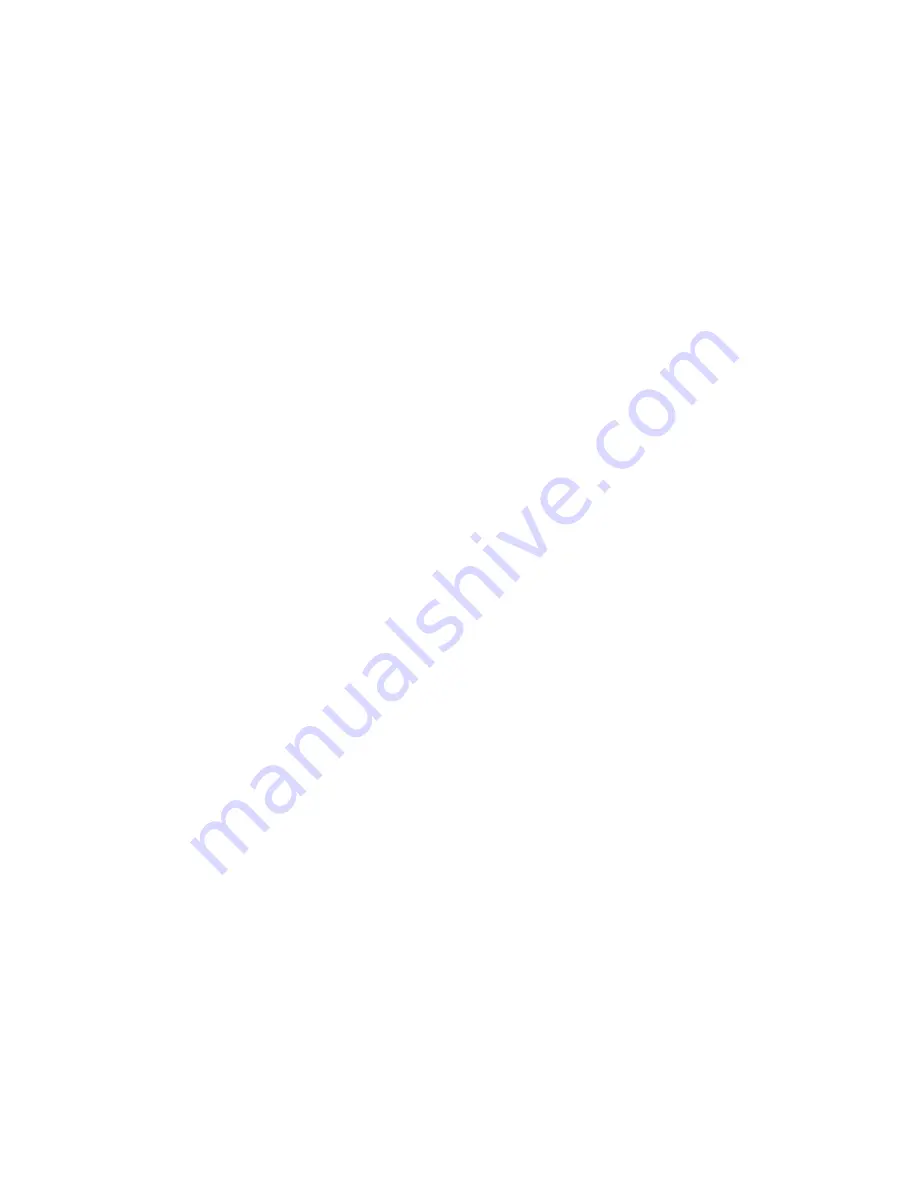
①
Features and application scope of the process
The pulse type argon tungsten welding is different from the continuous (DC) argon welding.
The welding current is pulsed. The wave form of the current is shown in the sketch above. Ip
and Ib and their continuous time tp and tb can be regulated according to requirements of the
process. The amplitude value of electric current changes periodically with certain frequency in
case of the pulse current, molten base will be formed in the work piece and the molten bath will
solidify. The welding seam is formed by reciprocal overlaps. Welding heat input can be
controlled by regulating pulse frequency, pulse current amplitude, size of base current,
continuous time of pulse current and base current and therefore the welding seam, size and
quality of the zone influenced from heat can be controlled.
②
Advantages and application scope of pulse argon gas tungsten arc welding
a. Precisely control the size of the bath inputting heat to the material to increase penetration
resistance of molten seam and preservation of bath. It is easy to obtain even fusion deepness.
b. Heating and cooling of each welding point is very fast. Therefore, the process is applicable for
the material with great difference of heat conductivity and thickness.
c. Pulse arc can obtain greater fusion deepness with lower heat input. Therefore under the same
condition, the zone influenced from the welding heat reduces the possibility of distortion from
welding. This is very important for sheet and ultra-thin sheet welding.
d. Fast cooling of the bath metal and short duration time of high temperatures during welding can
reduce cracks caused to the thermo-sensitive materials during welding.
③
.Selection of welding parameters
Except for pulse current, width time (width ratio) and pulse frequency, welding parameters of
pulse argon gas tungsten arc welding are the same as general tungsten DC argon arc welding.
Increasing pulse current means electric arc can obtain greater penetration ability. However, too
much current can cause local melting of tungsten electrode. Generally, welding current required
for DC tungsten argon arc welding uses greater current. The arc holding current and base current
influences the cooling and crystallizing of the metal in the bath. The range is determined by the
performance of the welding materials. When the sheet is being welded, smaller arc holding
current (base current) is usually used in order to reduce t h e p o s s i b i l i t y o f blowing holes
through the sheet/material and reduce the possibility of sheet/material distortion. When pulse
width ratio (holding time of pulse current and base current) is selected, both the heat input and
features of pulse welding should be considered. Usually, it can be selected between 10
%
- 90
%
.
Selection of pulse frequency (periodical change time of pulse current) mainly depends on the
thickness of the sheet and welding speed. The customized settings of the operator should also be
considered for the pulse width ratio.