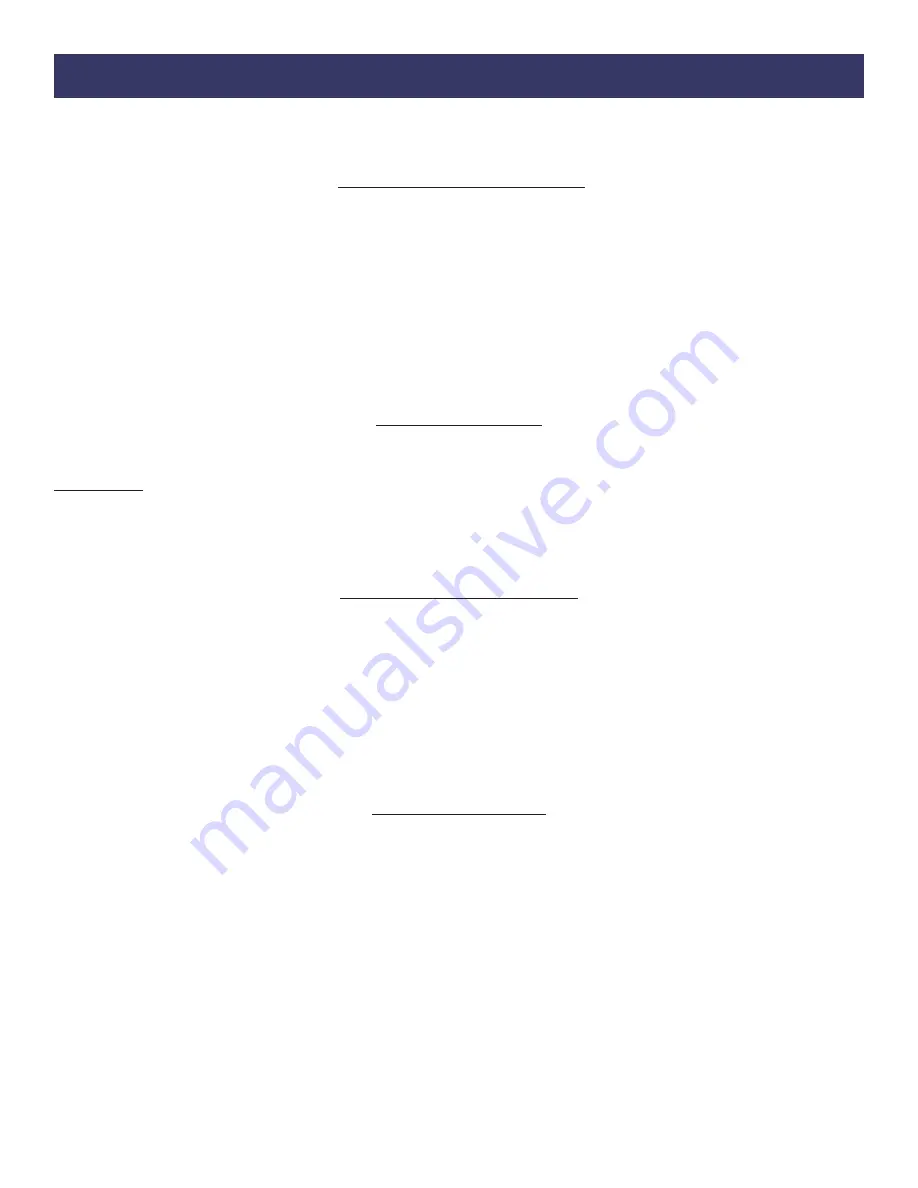
Following the guidelines will help you to ensure the pneumatic tools your company uses are operating
and are maintained in the very best of condition.
Initial Inspection of a New Tool
When a new tool is delivered to your facility, it is important to inspect the tool for any signs of damage
that may have occurred during shipping. Here is a list of things to inspect:
● With the tool disconnected from the air supply, depress the throttle lever or trigger. The device
should move freely and not become caught.
● Inspect the guard of the tool, if so equipped. The guard should be free of any chips, nicks or
dents.
● Inspect the spindle of the tool. The threads should show no signs of bends or chips. Grasp the
spindle by hand and spin. The spindle should turn freely with no resistance.
Plumbing Installation
The tool must have fittings and connectors installed into the air inlet in order to connect with your
companies air system. Your choice of fittings can greatly affect the performance of the tool.
Fitting Size
The size of the air inlet of the tool is the minimum size of fitting that will allow for proper airflow into the
tool. Should a smaller fitting size be used such as reducers or adapters, this will constrict the airflow
into the tool and reduce the overall performance.
Coupling Size and Installation
The coupling size should be equal to or larger than the inlet size of the tool. If a smaller size coupling
is used then the air supply volume may be reduced which may lead to reduced performance from
the tool.
The coupling should be installed near to the tool. It is important that the tool receive internal lubrication
on a regular basis. Having the connection closer to the tool will promote regular lubrication, as the
connection is easily accessible. Hose whips are often used between the tool and the coupling.
Use thread sealant on all pipe threads and ensure a tight fit.
Operating Speed Test
After your initial inspection and installation of the plumbing connections, it is important to test for
the operating speed of the tool. This test should be performed before you install any abrasive or
tooling. Each tool is stamped with a maximum operating speed. This speed determines the highest
rotational speed in R.P.M.’s that the tool will turn when it is functioning properly. This speed was set
from the factory and is closely related to the operating speed of the abrasive used with the tool. This
relationship will be discussed in the “mounting abrasives” section.
Find the maximum operating speed stamped onto the tool. Connect the tool to an air supply that
provides 90 psi and secure the tool in a vise. A lower or higher air pressure will result in a false
speed test and may create a hazardous situation. Depress the throttle lever or trigger and run the tool.
Use a properly calibrated tachometer to determine the actual operating speed of the tool. The actual
operating speed on the tachometer should not exceed 95% of the maximum free speed stamped on
the tool. If this is not the case then contact the distributor or tool manufacturer immediately. The tool
must not be put into service if the actual speed is over 95% of the stamped maximum speed.
Installation and Maintenance Tips
Содержание 467BRA1
Страница 4: ...Maintenance...