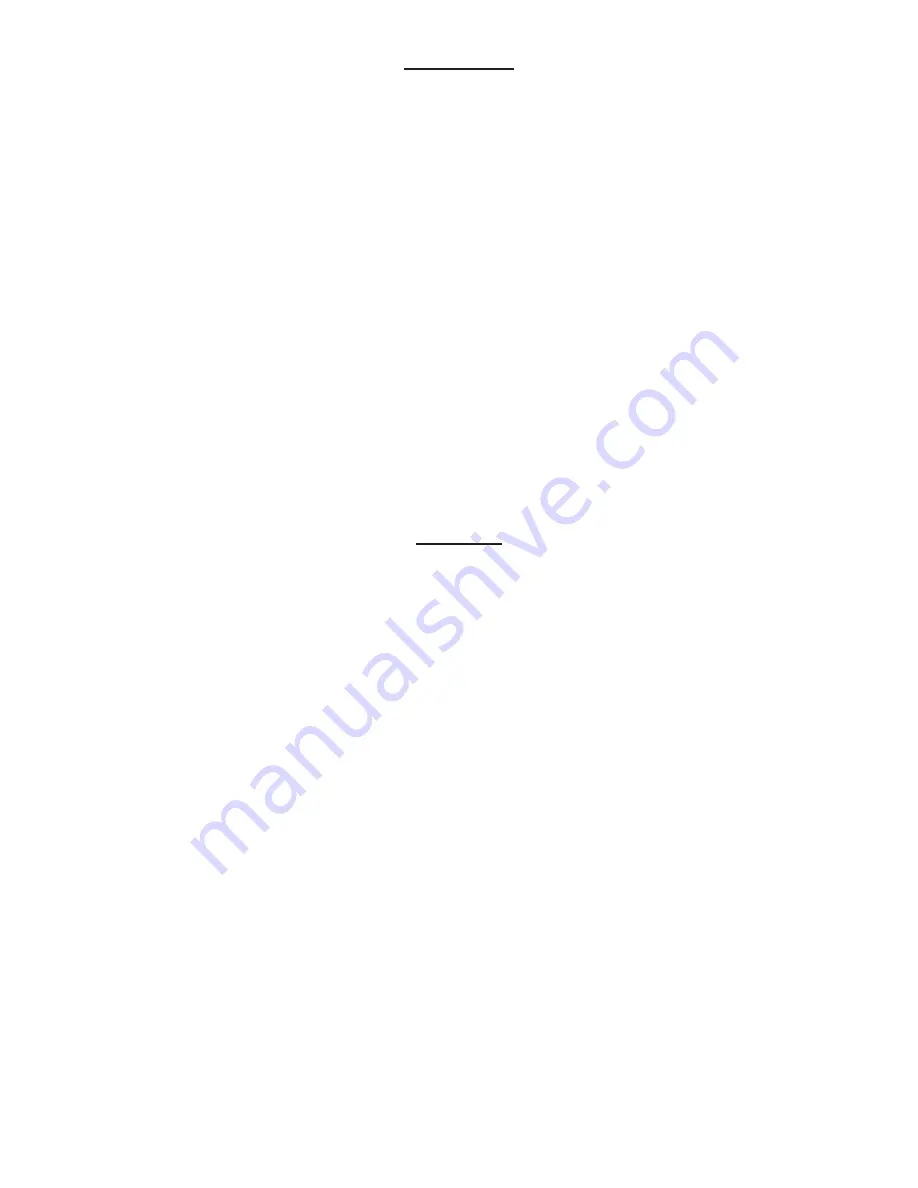
Disassemble
1. Disconnect air and remove all burrs, and accessories.
2. Remove collet nut (310-3 or 400-G-38). Remove nose piece (310-2), and insert (310-xx) if present.
3. Secure tool in vise vertically with output of tool upward. Clamp onto the flats toward the rear of the
motor housing.
4. Unscrew exhaust guard (320-38[S] or 320-39[S]), and exhaust deflector (320-40) if present.
Unscrew bearing cap (320-37[S]) from motor housing (320-1[S]) and slide motor out. Remove motor
housing from vise and take wafer (320-9W) and o-ring (320-9R) out of motor housing.
5. Slip snap ring (592016) from groove at rear of rotor (320-5).
6. Install brass jaws on vise. Secure motor assembly into vise vertically with output pointed down.
Clamp lightly the outside diameter of the cylinder (320-2) and rear endplate (320-3).
7. Use a 3/16” punch to tap spindle out of rear bearing (400-9). Be careful not to drop the front motor
assembly when it is free. Remove from vise.
8. Remove 3 blades (320-6).
9. With brass jaws still in vise, firmly clamp rotor in vise with output pointed upward. Using a wrench,
unscrew the collet body (310-1 or 310-13).
10. Support the rotor assembly vertically on a suitable drill block. Press spindle through front bearing
(320-11) with an arbor press. Remove spacer (320-5-R).
11. Remove bearing (320-11) from front endplate (320-7) with a small punch.
12. To check throttle valve unscrew throttle valve cap (320-41). Lift out valve spring (320-34) and
throttle valve (320-29). Remove and replace o-rings (844302 and 200-16) if cracked or worn.
Assembly
1. Be sure that all parts are clean and free of any abrasive.
2. Install the spacer (320-5-R) onto the threaded end of the rotor. Ensure that the spacer sits flush
against the rotor.
3. Press bearing (320-11) into recessed area of front endplate (320-7)
4. Support the front bearing assembly on a suitable drill block. Press the rotor (320-5) into the rear of
front endplate and through front bearing.
5. With brass jaws in vise, clamp firmly onto rotor (320-5) with output upward. Install the collet body
(310-1 or 310-13) onto the threaded end of the rotor and tighten with a wrench. Remove from vise.
6. Place 3 blades (320-6) into rotor slots.
7. Slip cylinder (320-2) over rotor. Be sure the alignment pin is oriented away from the front for the
motor assembly.
8. Install rear endplate (320-3) locating cylinder pin in the small hole of the rear endplate and the
cutaway on the side of the endplate over the air inlet of the cylinder.
9. Place bearing (400-9) over rear endplate. Tap in place with bearing driver (1100-802).
10. Place snap ring (592016) in spindle groove.
11. Grasp the collet body in one hand with the output downward. Place o-ring (320-9R) and then
wafer (320-9W) onto top of rear bearing. Carefully place motor housing (320-1[S]) over motor
assembly, taking care that the cover and o-ring stay in position on top of bearing. Insure that the
motor is fully into the case, then carefully turn the assembly over, so that the output points upward.
12. Secure tool in vise vertically with output of tool upward. Clamp onto the flats toward the rear of the
motor housing. Screw on the bearing cup (320-37[S]) and tighten with a wrench.
13. On 2-piece collet models, install collet nut (400-G-38). On 4-piece collet models install collet insert
(310-xx), nose piece (310-2) and collet nut (310-3).
14. On front exhaust models install exhaust guard (320-38[S]). On side exhaust models install
deflector (320-40) and exhaust guard (320-39[S]).
15. Check the operating speed with a reliable tachometer. The speed must be at or below the
stamped speed on the tool.
Reinstall all safety devices and accessories.
Содержание 36G-2
Страница 4: ...Maintenance ...