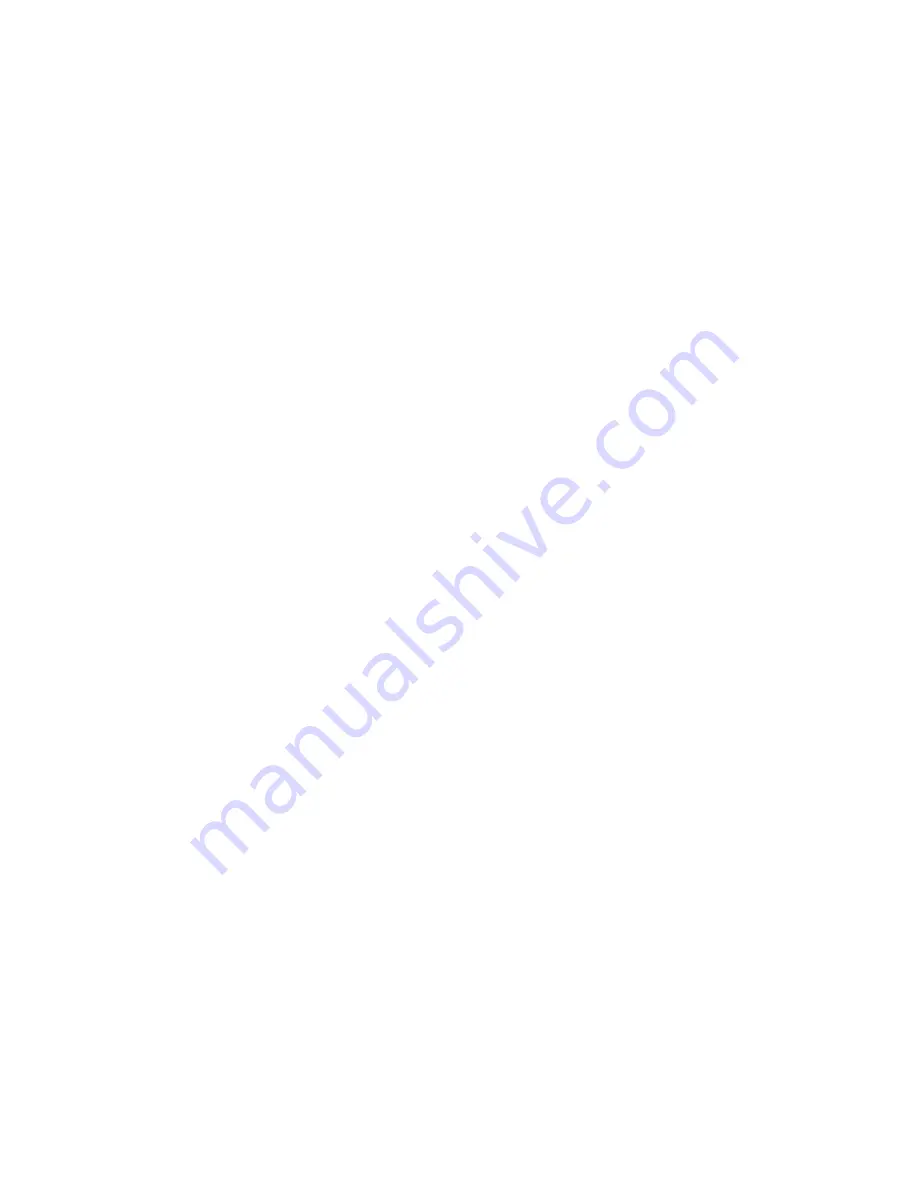
7
Clamping pressure, or cam-over pressure, is adjustable. Having a lot of it is often thought
to be a good thing. Try this when the middle is not bending the same as the ends; instead
of adding more clamping pressure reduce it. Consider the possibility that any brake is
naturally stiffer near the ends than the middle. When cam pressure is added more than a
very light touch, the material being formed has more pressure applied to it on the ends
than the center before the bend is even started (because the brake will flex slightly more
in the center than it will at the ends). So both the material and the brake are in a distorted
condition from the get go. Adding more clamping pressure makes it worse. You may
have noticed a wavy condition to the material hanging out the back of the brake when
clamped. Try reducing truss pre-load, and reduce clamp pressure. See if you get a better
bend, and if it is much easier to pull the cam over. Try zero clamp pressure next. With
little or zero clamp pressure, you will see the entire clamp or head assembly of the brake
lift at the start of a bend, but that is ok since it is all lifting evenly.
OIL APRON PINS, CLAMPING CAMS, & VERTICAL GUIDES BEHIND THE
CLAMP FREQUENTLY.
RADIUS SET BACK OR BEAM ADJUSTMENT
When you are forming light material, set your clamp back from the edge of the table at
least 1.5 times the thickness of the material being formed. When forming maximum rated
material use at least 2 times, and better to try 3 times material thickness for your set back.
Set back allows a radius. Up to a point, more radius results in needing less pressure to
make the bend. Less pressure means everything is distorting less and you get more
consistent bends.
USING A “BOOT” TO INCREASE INSIDE BEND RADIUS
When forming some materials, such as aluminum, it is desirable to bend against an edge
that is not so sharp as the standard edge. This will decrease the tendency of aluminum to
stress crack, or fracture, when forming it. You can make a ‘boot’ from about any light
gauge material, say about 4’ wide by the length of your brake. Something like 22ga –
24ga mild steel is good. Put the material in the brake so that you are bending a 2’ flange,
but bend it all the way over until it lies against the top of the brake. Now you can tape it
or use other means to keep that piece in place. With this ‘boot’ in place, you will increase
the inside radius of the bends you make. An additional ‘boot’ will increase the inside
radius of bends even more. Note that as you add one or more ‘boots’, you must also
adjust the clamp set back, so to maintain the 1.5 –3 times material thickness as your
minimum radius set back, also called beam set back. And, clamping pressure will need to
be adjusted. Remember that less pressure is usually better than too much pressure.
OIL APRON PINS, CLAMPING CAMS, & VERTICAL GUIDES BEHIND THE
CLAMP FREQUENTLY.
Содержание TK 422
Страница 8: ...8...