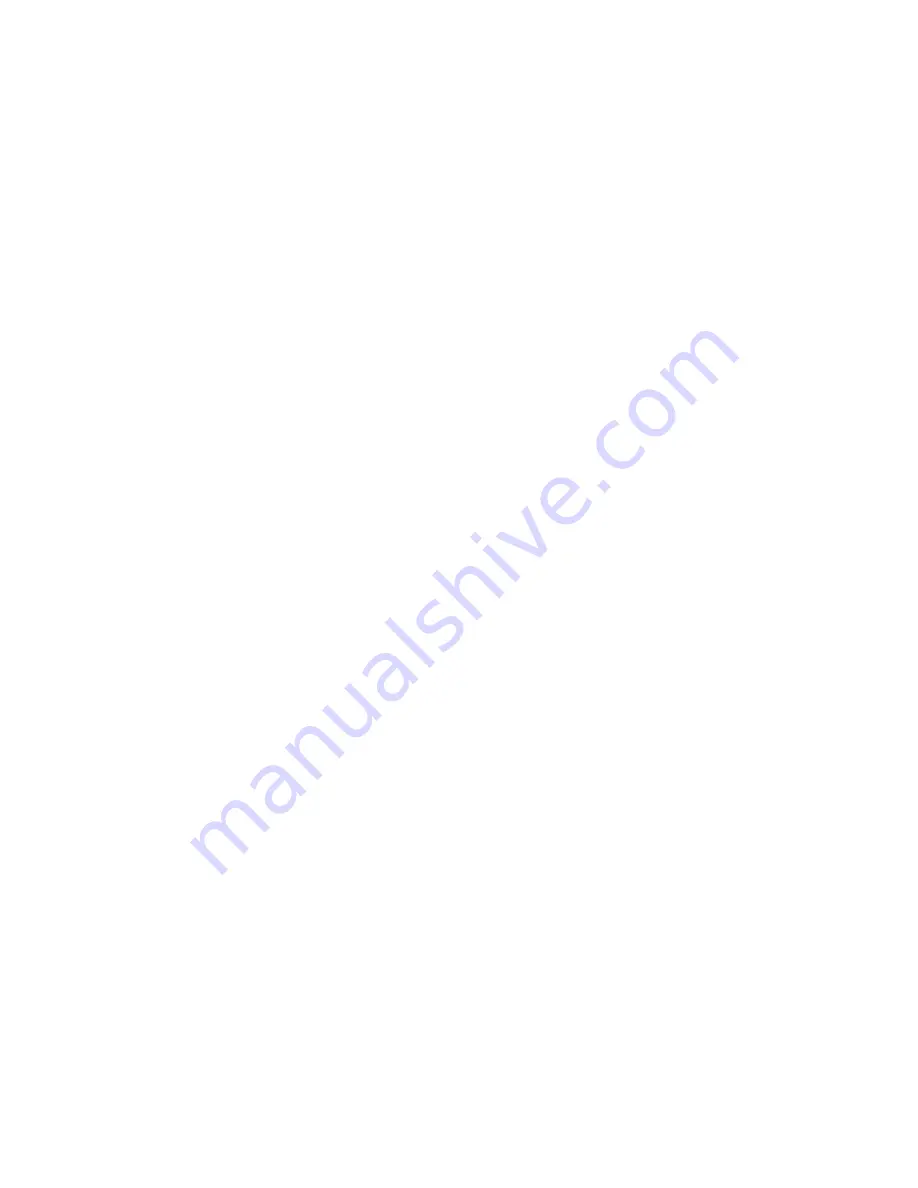
BEARING ASSEMBLY LUBRICATION
A. Initial Lubrication
The Timken
®
Sheave Pac
®
assembly is prelubricated, presealed, and
unitized at a Timken manufacturing facility. Accordingly, one of the
unique features of the assembly is its maintenance free, self-contained
design. As a result, regreasing of this assembly is not an option due to
the bearing component geometry. Therefore, it is suggested that the
grease line ports to sheaves that contain the Sheave Pac assembly
be plugged to eliminate any effort to grease these assemblies
during operation. Note that the lines to sheaves containing standard
assemblies must remain operational for regreasing per the current
process. Please contact your Timken representative if specialized
equipment is used that may require additional lubricant or subsequent
lubricant in service.
NOTE:
This assembly contains the optimum amount of grease from Timken.
Grease must not be added or removed.
B. Operating Grease Purge
Please note that although this assembly cannot be regreased once
installed, minimal grease will be purged from the assembly during the
initial run-in period. This leakage will decrease to a normal “weeping”
after this period. This is normal and expected for this kind of assembly
during application operation.
SUGGESTED INSTALLATION PROCEDURE
NOTE:
This procedure is to be viewed as a form of general suggestion and as
a means of communicating concerns about potential installation issues
only. It is not to be viewed as a declaration of installation methods to
be followed. Because these instructions are merely suggestions, they
may or may not be altered as the customer and/or installer sees fit.
Therefore, it is the responsibility of the customer and/or installer to
ensure careful and accurate assembly handling and installation. Any
and all damage incurred as a result of the handling and installation
procedure shall void all bearing Limited Warranty.
NOTE:
Any information and/or guidelines from any oil field
governing body should take precedence over and supplement
this information for roller bearings operated under
the jurisdiction of that governing body.
NOTE:
Typical bearing lifting practices utilizing straps/chains around
the bearing must not be employed. Doing so will cause
damage to the seals.
NOTE:
Lifting holes have been incorporated into the cup outer diameter
(O.D.) to aid in lifting. Please refer to Step 3 of the
Mounting of the
Bearing into Sheave
section for further details.
A. Mounting of the Bearing into Sheave
General Installation Information
A. Installation Methods:
• The preferred method of overcoming the tight fit between
the bearing outer diameter and the sheave inner diameter is
with press force and appropriate tooling. This document
focuses on this method.
• Installation methods that do not use press force need to be
reviewed by Timken before use. Press force is the preferred
method. Other methods can damage Sheave Pac bearing
assemblies.
B. Required Equipment:
• Press capable of handling sheave and providing the
required assembly installation force (see tables on pg. 2).
• Size-specific assembly installation tooling.
• Crane/hoist and lifting/handling fixture designed to safely
handle Sheave Pac assembly to ensure that no contact is
present with the entire seal.
C. General Cautions:
• Sheave Pac assembly must not be cooled to facilitate
installation unless process is reviewed by Timken. Contact
your Timken representative to facilitate this review.
•
Sheave must not be heated to facilitate installation unless the
customer and/or end user utilizes a procedure that verifies no
damage has been inflicted upon the sheave components.
• If customer selects sheave heating as an option, the
sheave bore must not exceed 200º F (93.3º C).
• Special care must be used during the removal of the bearing
packaging. Use of sharp objects may cause damage to the
assembly components. Particular care must be taken to
ensure no seal damage results from the use of sharp objects
or cutting tools.
• Typical bearing lifting practices utilizing straps/chain around
the bearing must not be employed. Doing so will cause
damage to the seal. For additional details, refer to Step 3 of
the section entitled
Mounting of the Bearing into Sheave.
• Overcoming the interference fit between the bearing
and sheave by use of impact process (hammer/drift/etc.)
is not suggested. Doing so will cause damage to the seals.
Step 1
Ensure that the sheave bore, lead-in chamfers and snap ring grooves
are in acceptable dimensional condition and free of sharp corners,
raised material, dents, nicks, burrs, gouges, and corrosion.
NOTE:
Any surface imperfections on the sheave bore must be carefully
filed and/or stoned down completely prior to assembly. These
imperfections can cause difficulty in assembly, create stress risers
during application loading, as well as cause excessive installation
damage to the seal outside diameter (O.D.), which may directly
increase the chance of contamination ingress and cause premature
damage to both the bearing assembly and the sheave.
3