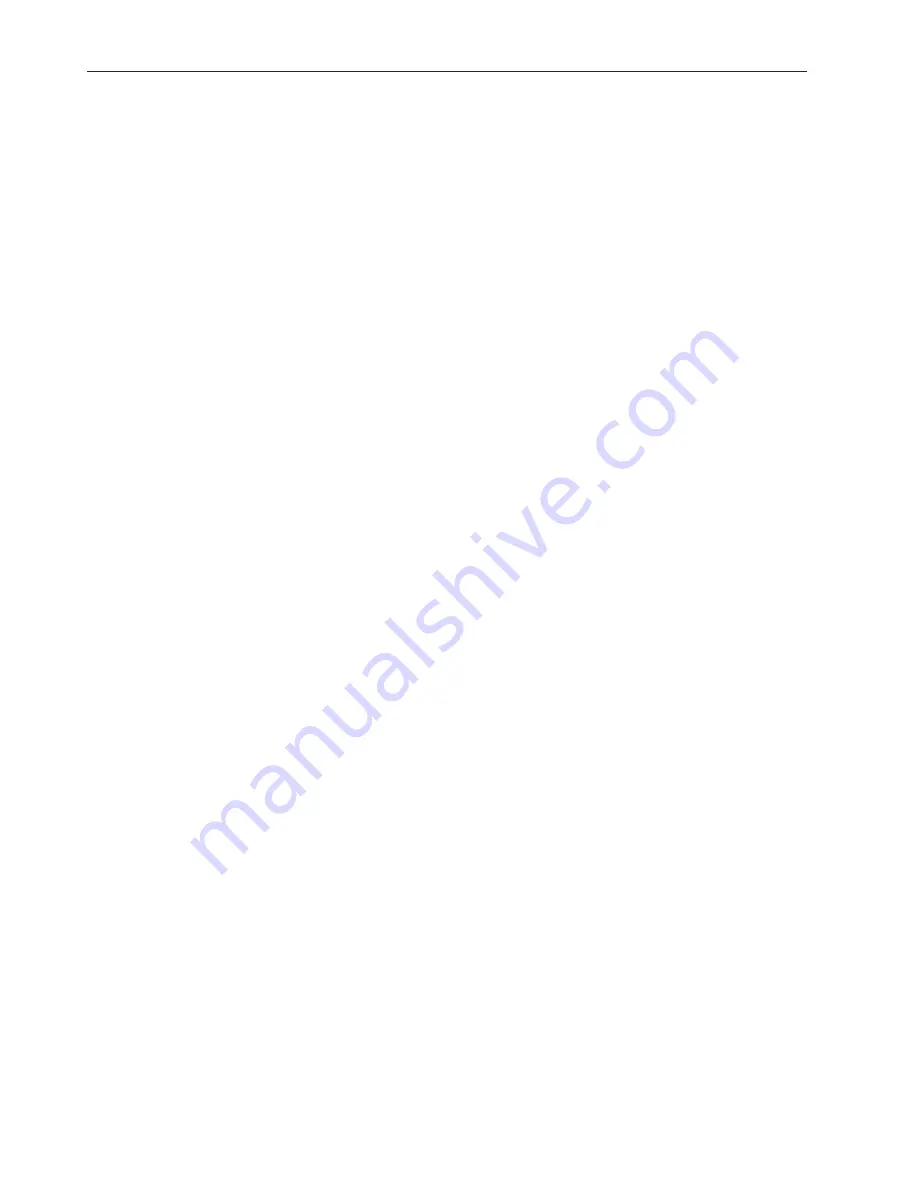
5. SYSTEM START-UP, OPERATION AND MAINTENANCE
5.6 GENERAL MAINTENANCE
STANDARDS
NOTE
It is the task of the Maintenance
Serviceman to keep the boiler
plant book updated. He must
note down every visit in this
book, indicating the date and the
work that was performed.
1- All operations must be done with
the burner off and the boiler at
room temperature.
2- We recommend, to prevent
accidental start-up, that you take
outelectric line fuses or put a
warning card on the control
switch.
3- If maintenance is to be done by,
several persons at once then
before starting to work first agree
on the person who is to actuate
the control switches.
4- Close the fuel supply pipeline
(fuel oil, gas).
5- Wear suitable garments, goggles,
gloves and masks during
cleaning. Comply with all the
safety regulations
specified for each type of job.
6- Protect all instruments from dust
and dirt (control board, electronic
board, probe sheath, control
gauges and instruments).
7- Use aspirating flue brushes and
vacuum cleaners for cleaning.
8- Carefully inspect all seals when
reinstalling parts that were
detached for cleaning. Replace
them if necessary.
9- Protect screws and nuts with
graphite grease to make it easier
to remove them later.
10-When the boiler has been shut
down for an extended time period
put message cards on the
switches and the boiler that
clearly specify procedures to
perform prior to start-up.
11- When re-starting the boiler, before
igniting the burner, check that the
boiler recirculation and heating
system circulation pumps
function properly.
WARNING
The baffles in the central ducts
must be reinstalled on all models
before reclosing the top
hatchway.
5.7 INSPECTION AND
MAINTENANCE
Burner-boiler operating characteris-
tics and conditions are highly
variable, depending on the type of
fuel, the burner, ignition frequency,
etc.As a consequence standard
maintenance intervals cannot be set.
The Maintenance Serviceman must
determine maintenance intervals
based on monthly inspection of soot
deposits in the smokestack. These
checks are performed by opening the
front hatchways and checking the
cleanliness of the furnace and the up-
per smoke ducts. If there are carbon
deposits on the furnace walls then
check the burner nozzles and adjust
the combustion head. Maintenance
consists of carefully cleaning smoke
passages using flue brushes (the
baffles must be removed on all models
to do this). The furnace must be brus-
hed out to eliminate deposits of sulphur
or other solid matter.
5.8 CHECKING HATCHWAY SEAL
Combustion gas leaks from front
hatchway seals can be eliminated by
increasing the pressure of the
hatchway on the seals.
Seals themselves may be ruined if
their surfaces are cut by seal lips.
In this case replace the seals.
20
Содержание CTC Maxi 100
Страница 2: ......
Страница 4: ......
Страница 15: ...13 3 INSTALLATION 3 7 WIRING DIAGRAM CTC MAXI 80 200 ...
Страница 23: ......
Страница 24: ......